The Ultimate Guide To Identifying Different Types Of Palletization
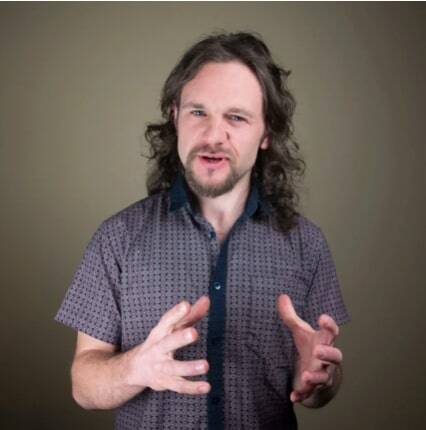
Posted on Feb 03, 2023 2:07 PM. 5 min read time
Palletization is a core step in the supply chain process. On the surface, palletizing can seem very simple — you just stack boxes onto an empty pallets. But there are many different types of palletization and various ways to compare these types.
With so many different pallet types and materials, process layouts, and levels of automation, it's easy to become overwhelmed when trying to determine which type of palletization is best suited to your specific needs.
In this guide, we walk you through each of the different types of palletization. We compare each type's advantages and disadvantages to help you identify the best one for you.
How many types of palletization are there?
Given their supposed simplicity, pallets can be surprisingly complex.
It's hard to say exactly how many distinct types of palletization there are. Depending on who you are talking to, they may have different ways of categorizing pallets and the processes surrounding them.
For example, a pallet manufacturer may differentiate pallets by material, shape, or industry – different industries sometimes require specific pallets for regulatory reasons. A process engineer might instead look at how pallets can fit into the packing processes in different ways. And an automation engineer will probably look at the different levels of automation.
As a pallet user, it's helpful to understand these different categorizations so you can make more informed choices for your end of line processes.
4 ways to compare different types of palletization
There is no definitive "standard" that describes different types of palletization.
However, here are 4 useful ways that you can differentiate between them:
1. By pallet type
One handy way to compare pallets themselves is to look at the type of pallet.
For example, you could compare them by the material that the pallet is made from, such as wood, metal, or plastic. You can also compare the design of the pallet, such as winged, stringer, or nested.
You can find out more about different pallet types in our article 10 Types of Pallet You Should Definitely Know About.
2. By palletizing pattern
Another common method of comparing pallets is by their palletizing pattern. This means looking at the order and orientation in which you placed boxes on the pallet. Examples include interlocked, split, row, and pinwheel.
The pallet pattern has a strong impact on the stability of the boxes. You can find out more about palletizing patterns in our article 7 Palletizing Patterns for Your Cobot to Reduce Product Damage
3. By process layout
Another way of looking at palletizing is to not focus on the pallets themselves, but to look at how they integrate into the rest of your operations.
By choosing the right process layout, you ensure that the steps leading up to your palletizing operation are the most efficient possible. Examples of different palletizing process types include serial palletization, parallel palletization, and hub and spoke palletization.
4. By level of automation
Finally, a very helpful way to compare different types of palletization is to look at the level of automation.
Level of automation determines how much of the palletizing task you have given (or could give) to automated machinery.
What's the most useful way to compare palletization types?
With all these options, what's the most useful way to compare palletization types?
It depends on why you are looking to compare them.
Comparing by pallet type is useful when you are purchasing pallets. However, it is not such a useful comparison once you already know what pallets you will be using.
Comparing by pallet pattern can help you optimize your use of space on the pallets themselves. This is can be an ongoing process and it's helpful to check your pallet patterns regularly, especially if you are changing your pallet layouts often.
Comparing by process layout is most helpful when you are designing or improving your entire facility layout. After this, it's unlikely you will look at process layout very often.
For many people looking to improve their palletizing process, the most relevant is the level of automation. By comparing for level of automation, you can make the right decisions about what technological solutions would most help your palletizing process.
Palletization by level of automation: advantages and disadvantages
When you are comparing palletizing types by level of automation, there are 4 basic levels you can look at.
Here are the 4 types along with their advantages and disadvantages:
1. Manual palletization
The first and most common level of palletization automation is manual palletizing. This requires no automation and instead relies on a human operator to move, organize, and stack products onto the pallet.
The chief advantage of manual palletizing is its flexibility and simplicity. However, it has huge disadvantages, including being unsafe for human operators, costly in terms of labor, and inconsistent in quality.
2. Semi-automated or aided palletization
After manual palletizing, many companies add some level of automation or mechanical aids to help with the palletizing task. A semi-automated process might include a system to pack layers onto a pallet, but that still requires human input.
An advantage of semi-automated systems is that they are readily available and can be almost as flexible as humans. However, they are often costly, less flexible than other forms of automation, and take up a lot of space.
3. Conventional automated palletization
The conventional approach to automating palletization tasks is to use fully automated palletization machines. These are commonly used in mass production environments.
An advantage of conventional palletizing automation is that they palletize very quickly. However, a downside is that they are huge, complex to install, and inflexible to changes.
4. Robotic palletization
Robotic palletization involves using a robot to stack products onto the pallet. There are different types, from large industrial robotic palletizers (that share some of the same downsides as conventional automation) to collaborative robot palletizers.
Collaborative robot palletizers, in particular, are very flexible, cost effective, and easy to deploy. Although they are not as fast as their conventional counterparts, they offer the benefits of robotic palletization to many more environments than was possible previously.
Finding the best type of palletization for you
Which type of palletization is best for you?
It's helpful to first decide what you want for your palletizing. This will help you decide the best way to compare the different palletizing types on offer.
If you are looking at robotic palletizing, you can make your life much easier by choosing a palletizing application kit. This includes everything you need to get started with palletizing automation and removes many of the common roadblocks that hold people back.
How do you compare palletization types in your business? Tell us in the comments below or join the discussion on LinkedIn, Twitter, Facebook, or the DoF professional robotics community.
Leave a comment