How to Choose Between Analog and Digital I/O
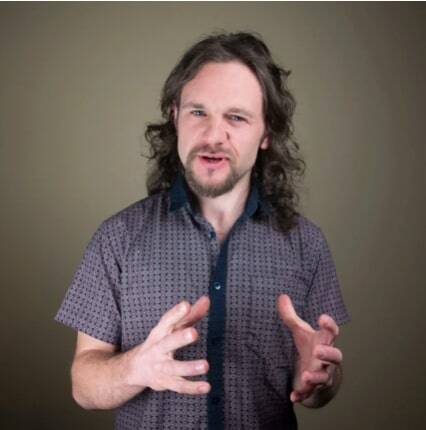
Posted on Jun 20, 2017 7:00 AM. 7 min read time
Which input or output device is the best for your robot application? Analog or digital? Here's how to choose the right I/O device for your needs.
It can be hard to decide whether to use a analog or digital device for your robotic application. Sometimes the decision is straightforward. Other times it seems like you have so many options which are all equally good.
Digital I/O tends to be easier to integrate, but it can restrict your control options. Analog I/O allows finer control, but this makes it more challenging to integrate.
Which is the best for your specific application?
In a previous article, we discussed the fundamental differences between analog and digital I/O. In this article, we describe a process for choosing the right I/O device for your application.
The Basic Difference Between Analog and Digital I/O
There are various differences between analog and digital, which we covered in detail in the previous article. For the purposes of selecting a robotic input or output device, the most important factor to consider is what type of event you are trying to detect or control:
- Analog I/O is used when you need to detect or control an event which involves a range of values.
- Digital I/O is used when you need to detect or control an event which is binary (yes/no, on/off, etc).
For example, imagine you were detecting the presence of a baked cookie for a robotic pick-and-place application. If you simply needed to detect whether the cookie was present or not, you could use a digital sensor. However, if you needed to measure the weight of the cookie, you would need an analog sensor.
A Complication: Analog Sensors With Digital I/O
Where this may get a little confusing is when your analog device has a digital interface.
For robotics, many of the analog devices we use have digital interfaces. This means that they convert the analog signal to/from a digital signal for easy integration into the control system. This process changes the properties of the signal (e.g. by reducing the resolution) so affects your choice of I/O device.
However, as long as you choose a device with sufficient performance for your application, you can usually consider an analog device with digital I/O to be the same as a pure analog device. This assumption is only true for the purposes of programming a simple robot — analog electronics engineers would probably object to such a gross simplification.
Five Questions for Choosing an Input Device
How do you choose an input device for your robotic application?
Here are five questions to ask yourself which can help you decide which device to choose:
- What do you want to detect/measure? — e.g. Do you want to detect the distance from the robot to a waiting part?
- What's the simplest way of achieving this? — e.g. Do you really need to detect the distance to the object? If so, you'll need an analog sensor. Or, is it sufficient to just detect the presence of the object? If so, a digital sensor could work.
- Could you detect it using the sensors already available? — e.g. If your robot already has a force sensor, could you use it to tap the object to check its presence? Would that make sense for your application?
- What type of sensor could you use? — e.g. If you do need a new sensor, what options do you have?
- How will you handle them in programming? — e.g. There may be different versions of the same sensor. Would some be easier to integrate than others?
Examples of Analog and Digital Input Devices
Let's have a look at some input devices which you may use for your robot. For a more detailed understanding of these, check out our eBook "Adding Extra Sensors to your Cobot."
Analog Input Devices
Many of the common sensors for robots are analog, though they often communicate via digital interfaces. Examples include:
- Force Sensors — Either attached to the robot or fixed elsewhere, these measure the magnitude of forces applied to them as an analog value, often in multiple axes at once.
- Potentiometers — These are used for a variety of applications, from simple control knobs to detecting the position of a motor.
- Light sensors — These can be single or multi-color sensors. They detect the amount of light hitting them and are used in photoelectric part detection sensors to measure the distance to objects.
- Vision sensors — Technically, these are analog input devices as they measure the amount of light hitting a sensor. However, they are often grouped separately from other sensors as they require special programming.
Digital Input Devices
Digital sensors are common for basic control needs. Examples of digital input devices include:
- Limit switches — These are used for a variety of purposes, such as detecting when a safety door is opened or when a robot reaches an external limit.
- Basic part detection sensors — There are a wide variety of these sensors, which detect when an object is present. See the eBook for a more complete list.
- Single-beam laser safety sensors — Often used in safety curtains, these sensors detect when a laser beam is broken, to indicate that someone has entered an unsafe area.
- Push buttons — A simple but important sensor. Push buttons are an effective way to start or stop a pre-programmed sequence.
Five Questions for Choosing an Output Device
Choosing output device involves slightly different decisions than choosing an input device.
Here are five questions to ask yourself which can help you decide which device to choose:
- What actions do you want to control? — e.g. Do you want to stop workers from entering an unsafe area when the robot is moving?
- What is the simplest way that you could do that? — e.g. Would it be sufficient to turn on a warning light when the robot was operational, or do you need more advanced warning signals?
- What outputs do you already have at your disposal and could you use them? — e.g. Does the robot teach pendant have an output screen which could display a warning message? Would this be a sufficient warning for your application?
- How complex do you need the output to be? — e.g. Would it be enough to simply turn on a warning lamp, or do you also need to set the brightness of the lamp?
- Is your chosen output the only way to solve this issue? — e.g. If you are using a collaborative robot at high speeds, could you reduce the speed of the robot and remove the need for a safe zone?
Examples of Analog and Digital Output Devices
Here are some output devices which you may use for your robot.
Analog Output Devices
The main output device for a robotic program is the robot itself. Examples of additional analog output devices include:
- Conveyor belt motor speed — For advanced conveyor applications, the speed of the belt can be integrated into the robot controller.
- Analog control valves — When a fluid is involved in a process, analog control valves are a way to precisely control the amount of fluid which is released. These are used in hydraulics, for example.
- Lamp brightness — The brightness of an LED or lamp can be set precisely.
Analog output devices involve more complex control. They often tend to be handled by a separate control system rather than being incorporated into the robot programming directly.
Digital Output Devices
Many of the analog output devices listed above can also be operated digitally. For example, a fixed-speed a conveyor belt could be controlled with a simple on/off signal. Digital output devices include:
- Relays — These are electronically controllable switches, which allow high-power circuits to be operated by low-power electronics. They can be used in a huge range of applications.
- Warning lights — Often used in circuits with safety sensors, these can be switched on to show that a robot is in operation and workers should not enter the area.
- Conveyor on/off — A simpler way of controlling conveyor belts than speed control is just to allow the robot controller to activate the belt.
- Audio alarms — Like warning lights, these are often used to indicate that a safety-related event has occurred.
Choosing Analog and Digital I/O Devices for Your Application
The main thing to remember when picking an I/O device is to keep it simple. Only add new devices when their functionality is absolutely necessary to your application. Always ask there is a simpler way of achieving the same effect.
What questions do you have about digital and analog I/O for robotics? Tell us in the comments below or join the discussion on LinkedIn, Twitter, Facebook or the DoF professional robotics community.
Leave a comment