Robotiq Featured at the DARPA Robotics Challenge
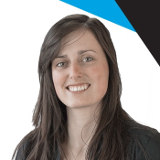
Posted on Jul 23, 2013 10:53 AM. 5 min read time
Every time a man-made or natural disaster occurs, humans risk their lives to handle the crisis. There will be limitations to what humans will be able to do to help remedy these situations due to health and safety hazards. Aren't robots created to handle the dull, dirty... and dangerous? Today, robotics can help but they are not yet ready, robust or efficient enough to perform the needed tasks in these extreme and unstructured environments. In order to be ready in case of a catastrophe, DARPA Robotics Challenge (DRC) will help in generating groundbreaking research and development. This research will improve actual robotic technologies and create more robust robots to help in case of a disaster. They would be useful for disaster response operations with human collaboration to help reduce casualties, avoid further destruction and save lives.
Challenge
The challenge has three different steps. The first one is the Virtual Robotic Challenge (VRC). This step occurred from June 17th to the 21st. Then, the second step is a physical challenge, where the robots will have to do individual disaster responses. This DARPA Robotics Challenge Trial will take place in December 2013. The DARPA Robotics Challenge Finals will be held in December 2014 and the teams will have a complete disaster scenario to master with their robot(s). Finally, the big winner of the DARPA Robotics Challenge will received $2,000,000 USD.
This is an example task that the robots will have to do - cross an uneven path.
Teams
The teams are separated into different categories where the details of the challenge may differ.
Track A Teams
These teams are developing both hardware and software for the challenge. This means they have to build their own custom robot. First, DARPA selected seven track A teams to receive funding. During the VRC, the DARPA staff visited each track A team to evaluate their platform design-and-build progress. Six teams were then selected to go to the trials with continued DARPA funding. Here is a video including all the track A teams selected:
Track B Teams
These teams only have to develop the software part of the robot. Eleven initial teams were selected to get DARPA funding. During the VRC, the teams software was evaluated and seven teams were selected to go on to the trials.
Track C Teams
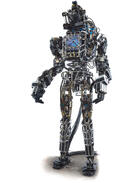
DARPA received over 100 entries for this category. These teams are similar to the track B teams, except that they don’t receive any financial support in the beginning. They will compete against track B teams for the chance to be selected for the trials with further support.
These selected teams will receive an Atlas robot donated by DARPA. Atlas is known as the most advanced humanoid robot ever built. The Track B and C teams will have to complete this physical shell by adding software brain and nerves. Moreover, they will also receive financial aid from DARPA and technical support from the creator of Atlas, Boston Dynamics.
Track D Teams
These teams will take part in the trials with their own robot(s). However, they won’t have any financial aid from DARPA. Moreover, they will be able to participate in the DARPA Robotics Challenge Finals in December 2014.
Robotiq Featured
One Track A team is worth mentioning and it is the team from Carnegie Mellon University. They were selected during the virtual challenge to continue towards the trials with DARPA funding.
Their robot is called CHIMP for CMU Highly Intelligent Mobile Platform. During the challenge, their human-size robot will have to accomplish tasks such as: climbing ladders, driving vehicles and closing valves. It will be five-feet, four-inches tall and 2.5 feet wide but will weigh just over 400 pounds. It will move around like a tank on its four rubber tracks (two as its feet and two on its forearms). Then, it will stand up to accomplish its tasks. Moreover, CHIMP has cameras, lasers and perception systems that will be used to produce 2-D and 3-D images of its environment. These images will help to guide the robot through the field.
In order to manipulate the various objects or valves, Robotiq supplied the CMU team with two 3-Finger Adaptive Grippers. These robust and flexible end effectors will allow CHIMP to grab any form or size of object, whether solid or compliant. Moreover, another team chose our Grippers to complete their robot and it is SHAFT Inc. in collaboration with the University of Tokyo. Robotiq is proud to be a part of this challenge to help further robotics research and development. This is also a voyage back to the origin of our hands (Gripper), which were initially developed for harsh, unstructured environments, such as space and nuclear site clean-up.
Leave a comment