Which Do You Need? Part-to-Process or Process-to-Part?
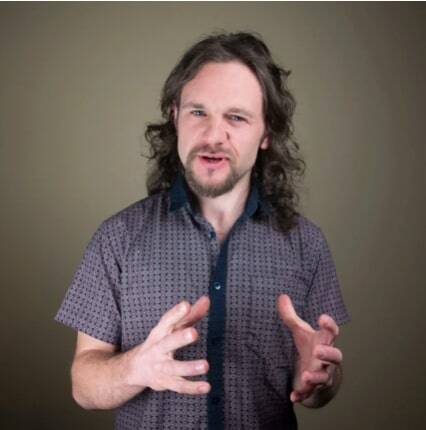
Posted on Dec 05, 2019 11:02 AM. 6 min read time
There are two ways to automate a task with a cobot: part-to-process or process-to-part. Which do you need for your cobot application? Here's how to decide.
It's becoming increasingly easy to automate with a collaborative robot. For some common tasks, there are now pre-packaged solutions which can cut days (or even weeks) off your integration time.
However, there is one big decision that you will need to make before you can get started: Will your task be part-to-process or process-to-part?
Your answer will determine the best way to deploy the cobot and which accessories might make the job easier. This choice is your first step towards picking the best solution.
Let's have a look at these two automation strategies and how you can decide which is the best one for you.
What is a "process" in this context?
The strategies of "part to process" and "process to part" both revolve around this word "process." This is a word that we use a lot in business, to refer to a variety of things, so it's worth defining our terms.
The two terms mean:
- Part — In this case, a part is any object that you are going to transform or inspect. It's most usually a product (or a component of a product). You could also call this the "workpiece."
- Process — In this context, "process" refers to the mechanical, chemical, or sensing operation that you want to perform on the part to transform or inspect it.
In both strategies, one of these is fixed and the other is moving. As we are talking about robotic automation here, the movement in this case is carried out by the collaborative robot. Either the robot moves the part whilst the process stays static, or vice versa.
Some examples
Let's take a look at a few example applications which I'll use throughout this article. These tasks are all achievable with a collaborative robot and can use either strategy.
- Sanding wood — This task involves moving some form of abrasive media over the surface of the wood. Manual sanding can be a tough and tiring job so is a perfect candidate for automation.
- Gluing electronics — This task involves dispensing a consistent stream of glue onto an electronic board or casing. Automation can improve the consistency and efficiency of the task.
- Driving screws — This task involves inserting screws into the part. Automation is particularly beneficial for parts which require many screws.
- Polishing metal — This task involves moving a soft polishing material over the surface of the metal to improve the part's finish. Automation can seriously improve the consistency of the finish.
With specially designed cobot application kits, it's now possible to integrate some of these tasks quickly and easily. However, first, you need to decide which automation strategy you will use.
Option 1: Part to process
As the name suggests, part-to-process involves moving the part and keeping the process fixed. The collaborative robot will hold the part (e.g. with a suitable 2-Finger Gripper) and move it towards the process machine which remains static.
This strategy is best with small parts. The gripper must be able to firmly grasp the part and hold it steady while the process machine is operating. The control software uses an External Tool Center Point (TCP) to make programming easier.
Sanding wood with part to process
A common example is to have a belt sander fixed in place. The robot moves small wooden parts onto the moving belt. For this, you would need an External Tool Finishing Kit.
Gluing electronics with part to process
Using a part-to-process strategy allows you to use an automatic glue dispensing machine. The robot holds the part and moves it in a controlled path to apply the glue to the electronic board.
Here is an example:
Driving screws with part to process
With a part-to-process strategy, driving screws is really a machine tending task as it involves moving the part to an automatic screwing machine. Unlike with the gluing application, the robot doesn't have to move along a tightly controlled path.
Polishing metal with part to process
A common polishing task which uses the part-to-process strategy is to hold small objects onto a polishing or buffing wheel. We demonstrated this task at Automate 2019 for a task which involved polishing metal door handles.
Option 2: Process to part
As the name suggests, process-to-part is the exact opposite of the previous strategy. It involves keeping the part fixed and moving the process itself. The collaborative robot will be fitted with a special process end effector.
This strategy is best with large parts which are difficult to move.
Sanding wood with process to part
Large wooden workpieces almost always require surface sanding. This is achieved by attaching a special sanding end effector to your cobot. You can get this application up and running very quickly, as demonstrated in this video:
Gluing electronics with process to part
Dispensing glue with a process-to-part strategy involves attaching a dispensing end effector to the robot. Some users design their own custom end effectors for this.
Driving screws with process to part
A nutrunner tool allows the robot to drive screws itself. This is a far more flexible approach than using an automated screwing machine, as in the part-to-process strategy. An automated screw dispenser can speed up this task considerably, as shown here:
Polishing metal with process to part
This is similar to the sanding task. In fact, the same sanding end effector as used in the wood sanding example can also be used for polishing. The only difference is in the type of abrasive media that is attached to it.
How to pick the right option for you
Which is the best automation strategy for your situation? Part-to-process or process-to-part?
Here are some questions you can ask yourself to help you arrive at an answer:
- Is your part big or small? — Big parts often work better with process-to-part and small parts with part-to-process.
- How do human workers currently do the task? — If they currently hold the part, it probably makes sense for the robot to do the same.
- What other automation do you already have? — It makes sense to utilize the machines that you use already. For example, if you have a fixed glue dispensing machine, a part-to-process gluing application would make the best use of it, rather than buying a new gluing end effector for the robot.
Once you've decided which strategy suits you, it's simply a case of picking the application kit that suits your task!
Which strategy do you prefer? Tell us in the comments below or join the discussion on LinkedIn, Twitter, Facebook or the DoF professional robotics community.
Leave a comment