What Does Collaborative Robot Mean ?
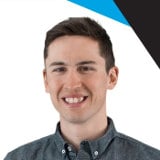
Posted on Aug 19, 2015 in Collaborative Robots
7 min read time
I recently put together an eBook on the risk assessment process and while I was doing it I found out that people are not totally understanding what a collaborative robot really is. The reason is quite simple, there is a lexicon confusion that needs to be clarified. I will try to make things clearer for you guys by referring (briefly) to standards and examples in the industry.
Collaboration
The literal definition of collaboration is: The action of working with someone to produce or create something. Which is the exact purpose of collaborative robots. However, the misunderstanding is not about the purpose or use of the robot, but its functionality or more precisely how it works. In fact, most people would think, a collaborative robot is a robot that is used without fencing and that can work around humans. Well, yes, this makes it collaborative, but no, it does not make it a collaborative robot! You should know that there are various types of collaborative robots and that only, uniquely, one type of collaborative robot can be used without any additional safety features. According the international standards ISO 10218 part 1 and part 2, there are four types of collaborative features for robots.
Safety Monitored Stop
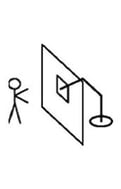
This kind of collaborative feature is used when a robot is mostly working on its own, but occasionally a human might need to enter its workspace. For example, when a certain operation must be performed on a part while it is in the robot’s space. Take a heavy part that has to be handled by a robot and a worker needs to do a secondary operation on it while the robot is still handling the part. This way the person can work on the part and still be in the robot’s space. If the human enters the restricted area in the pre-determined safety zone, the robot will stop all movement altogether. Notice that the robot is not shut down, but the brakes are on. Notice also that these types of robots are most efficient when people work mostly apart from the robot, but might get closer for a small amount of time. Otherwise, a lot of time could be lost as the robot continuously stops for human interruptions.
Photo from ISO 10218-2: 2011
Particular Features
- Uses regular industrial robots
- Safety devices that detect employee at proximity
- Used for sparse cooperative operations
- Basically stops when the safety zone is violated
Hand Guiding
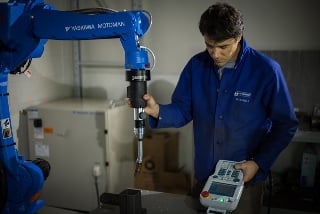
This type of collaborative application is used for hand guiding or path teaching. So if you want to teach paths quickly for pick and place applications for instance, you might use this type of application. However, you should notice that this type of collaboration uses regular industrial robots, but with an additional device that 'feels' the forces that the worker is applying on the robot tool. The most popular device to achieve such collaboration is a Force Torque Sensor such as the Robotiq FT 150. Notice that this type of device will simply read forces applied on the robot tool. This type of collaboration only applies to the robot while it is performing this particular function, which means that while the robot is functioning in its other modes, the robot still needs to have safeguarding in place.
Particular Features
- Uses regular industrial robots
- Needs end of arm device to detect applied forces
- Used for hand guiding and path teaching
- Does not make robot collaborative in other functions/modes
Speed and Separation Monitoring
Here the environment of the robot is monitored by lasers or a vision system that tracks the position of the workers. The robot will act within the functions of the safety zones that have been pre-designed for it. If the human is within a certain safety zone, the robot will respond with designated speeds (generally slow) and stop when the worker comes too close. So, when the workers are approaching the robot, it slows down, as the workers approach even closer, the robot slows down even more or stops. The video really shows how this type of collaboration is achieved.
So if you are wondering what's the difference between a Safety Monitored Stop and Speed and Separation Monitoring, it is quite simple. A Safety Monitored Stop is when the robot stops because someone or something has tripped its safety parameters. The robot must wait until the worker gives it the go ahead signal before it can resume operations. So it will wait until it receives feedback to continue. In the other case, the robot will constantly work at whichever speed is designated by the safety zones determined for it. The safety zones are gradated so that the robot produces different reactions according to the location of the worker within the different safety zones and might still result in a Safety Monitored Stop when the human comes too close to the robot.
Particular Features
- Uses regular industrial robots
- Needs vision system to detect the proximity of the worker
- Used for operations that require frequent worker presence
Power and Force Limiting
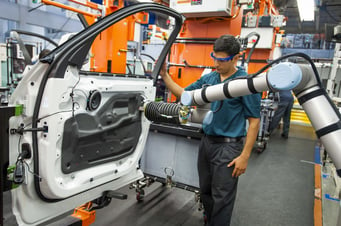
This is the type of robot that everybody calls a collaborative robot. So yes, this is probably the most worker friendly robot since it can work alongside humans without any additional safety devices. The robot can feel abnormal forces in its path. In fact, it is programmed to stop when it reads an overload in terms of force. These robots are also designed to dissipate forces in case of impact on a wide surface, which is one of the reasons why the robots are rounder. They also don't have exposed motors. A lot of these robots are certified by third parties who focus on industrial safety for human-robot collaboration. You should notice that technical specification ISO/TS 15066 will be released sometime soon and will specify the maximum forces (N) and energy (J) that can be applied on a human without any harm. This technical specification will clarify the safety requirements for human-robot collaboration for both regular industrial robots and force limited collaborative robots.
Particular Features
- Not your regular industrial robot
- Has force limited features
- Does not require additional safety devices (in most cases, still requires a risk assessment)
- Used for direct collaboration with the worker for various task
Force Limited Features
First of all the main feature of these robots is their ability to read forces in their joints. This allows them to detect when abnormal forces are applied on them while they are working. In these situations they can be programmed to stop or sometimes reverse positions mediating the initial contact. This means they can respond immediately if they come into contact with a human and perhaps dissipate some of the energy transferred from the impact.
This feature leads to another interesting feature that we have already discussed above; hand guiding. In fact, since these robots can feel forces, you can literally move them and show them positions or paths that they can repeat afterwards. While hand guiding helps with human-robot collaboration it does not make the robot intrinsically safe. The force limiting features are supposed to do this.
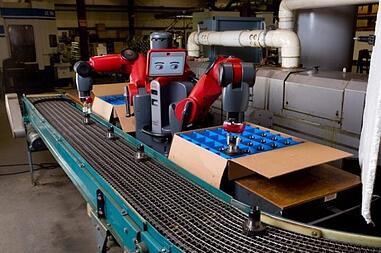
Marketed as being safe, these robots are definitely designed to be more responsive than their industrial mates. In fact, their geometry is rounder, they don’t have any kind of pinch point and most of the time they have internalized their motors and wires, etc. to make them more compact. Thus the term lightweight robot is sometimes applied to them. Some robots even have an external 'skin' that allows them to feel their environment but also gives an extra cushion in case of impact.
Finally economically a force limited robot is interesting because of its easy programming and integration. When you think about it, no need for fencing or other safety devices, the programming time is reduced because of hand guiding and finally you don't need to change your production line since it is made to work alongside humans. With an investment of around $50,000 you can have a complete robot cell and repay it in 6 months.
Force Limited Robots Models
- Universal Robots UR3, UR5, UR10
- Rethink Robotics Baxter, Sawyer
- KUKA LBR iiwa
- ABB Yumi
- F&P Robotics
- Fanuc CR-35iA
To conclude, it all comes down to the fact that there is a misunderstanding in the lexicon. Now that you know what you are talking about, you can go back to your good old habit of calling force limited robots; collaborative robots. Even we use it this way in our blog posts. But don't call industrial robots collaborative even though they can do collaborative applications. If you need more information on force limited robots, follow the link below to find our comparison sheet.
Leave a comment