How to Integrate the Adaptive Gripper on a Robot
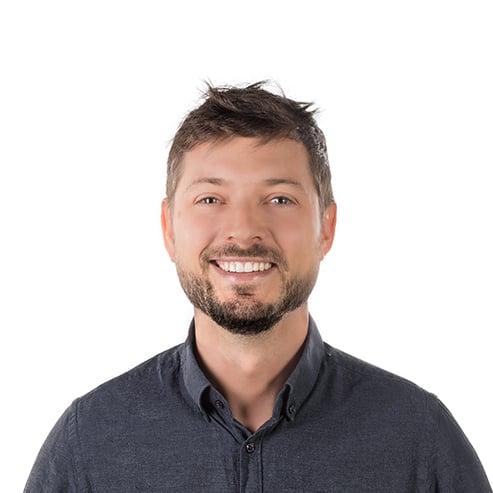
Posted on Aug 25, 2011 in Robot Grippers
2 min read time
The Robotiq Adaptive Gripper has more fingers and axis than conventional grippers. Still, we've worked to make it as simple as possible to integrate it with the different robots. Using a combination of mechanical intelligence, embedded electronics and software, the gripper offers great flexibility and is simple to integrate. Here's how it works and a few example videos.
Example 1: Gripper on Motoman Dual-Arm doing Kitting
If you cannot see the video please click here
Example 2: Gripper on ABB robot showing tactile teach pendant programming
Example 3: Gripper on Fanuc for Machine Tending
If you cannot see the video please click here.
Mechanical Interface
The gripper comes with a faceplate to match your robot's bolt pattern.
Electrical Connections
There are two connectors on the side of the gripper, one for 24 V 2 Amps DC power supply and one for the chosen communication protocol (Ethernet/IP, EtherCAT, Device Net, Modbus TCP or Modbus RTU).
Control
Even though there are 4 electric motors in the Adaptive Gripper, you don't need to control all axis independently. You can send high-level commands such as open, close (full or partial stroke with desired speed and force) or change operation mode. The gripper sends back information on the grip status. The programming of the gripper is done in the robot program. As you can see in an example below, it can be done from a teach pendant.
Leave a comment