A Beginners Guide to the Exoskeleton Industry
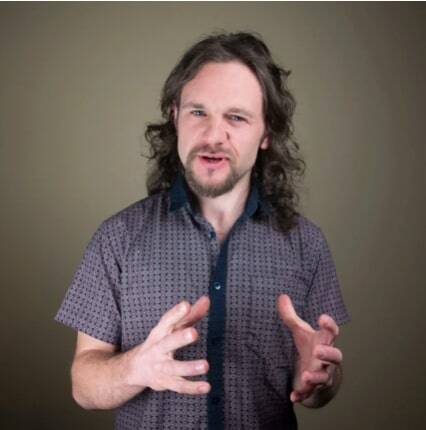
The exoskeleton industry is predicted to be the "next big thing." But, why are we not seeing them in businesses? Here's the lowdown on this industry of the future.
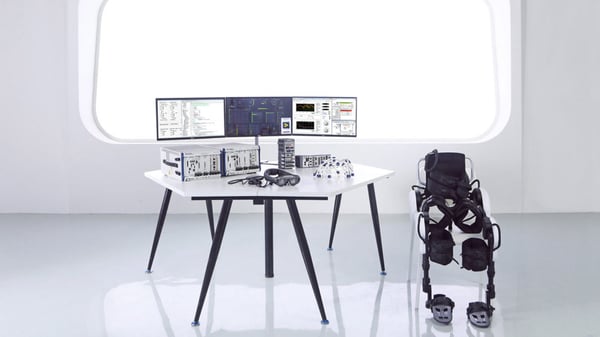
If you read robotics news as often as we do here at Robotiq, you might have noticed that there are a lot of stories about exoskeletons at the moment. We hear about new exoskeletons and fundings of exoskeleton startups quite often.
The exoskeleton industry has been tipped as "soon to be huge" for some years now, but it's never really taken off as explosively as people had predicted. However, it has still been growing and looks set to continue (much like the cobot industry, as we heard in our last RUC conference).
Despite its slow growth, it is an industry that we should all keep an eye on. It seems almost certain that exoskeletons will be part of our future. Here's the lowdown on the industry and how it's relevant to us.
What is an Exoskeleton?
The word exoskeleton comes from name of the rigid, external skin of invertebrate animals (bugs, spiders, crabs, etc) which allows their body to keep its form without an internal skeleton.
In robotics, exoskeletons are essentially wearable robots. They attach to the outside of your body like a skin and provide extra power to the normal movement of your muscles. They range from suits which simply support to your muscles a little (e.g. for rehabilitation) all the way up to suits which allow you lift heavy weights with very little effort.
Types of Exoskeleton
There are a huge number of different exoskeletons, too many to list here. Here are the common ways that exoskeletons are categorized in the industry.
By body part
- Upper extremity exoskeletons — These provide support to the upper body, including the arms, shoulders, and torso. A recent example is the Ottobock Paexo, announced in September 2018.
- Lower extremity exoskeletons — These provide support to the legs, hips, and lower torso. A good example is the rehabilitation system from ReWalk which announced its new clinical trials in July 2018.
- Full body exoskeletons — These provide support to the whole body and are thus the most powerful exoskeletons. A recent example is the Guardian XO from Sarcos Robotics which received $30 million in funding in September 2018.
By form
- Hard/classic exoskeletons — These use rigid structures and actuators. They are tough and can provide a lot of power.
- Soft exoskeletons — These are made of fabrics and other soft materials. Power is applied to the body via compliant actuators, such as air muscles or cables. They are more comfortable than classic exoskeletons but don't provide as much power.
By actuation technology
(including the rough percentage of each actuation type for the exoskeletons on the market in 2016)
- Electric (55%) — These use electric servos or other electric actuators to provide support and extra power to the wearer's muscles. They usually use batteries, so can be very portable.
- Hydraulic (20%) — These use hydraulic actuators which are more powerful than electric ones. However, they require larger and more complex power sources, such as internal combustion engines or hydrogen fuel cells.
- Fully mechanical (13%) — Also known as passive exoskeletons, these include no active actuators. Instead, they support the wearer using mechanical linkages. According to research, some can reduce muscle activity by 35% during assembly work, allowing workers to work for 3 times longer.
- Electric (55%) — These use electric servos or other electric actuators to provide support and extra power to the wearer's muscles. They usually use batteries, so can be very portable.
- Hydraulic (20%) — These use hydraulic actuators which are more powerful than electric ones. However, they require larger and more complex power sources, such as internal combustion engines or hydrogen fuel cells.
- Others (13%) — Less common are exoskeletons with fuel cell actuators, shape memory alloys, and pneumatics.
There are also a range of different application areas, each of which has different requirements for what it would need from an exoskeleton. For example, rehabilitation applications are more suited to soft, low-power devices which support and develop the natural muscle use of the wearer. On the other hand, military and construction applications would want high-powered exoskeletons to augment the strength of the wearer.
As seen in What's New In Robotics? 21.12.2018 / German Bionic
The state of the exoskeleton industry
There have been a stream of industry reports about exoskeleton markets recently. The global market is expected to reach $8.3 billion by 2025, or only $2.5 billion by 2025 depending on which prediction you believe. Also, the military exoskeleton industry anticipates growth thanks to increased interest by China and India.
Despite these lofty predictions, the exoskeleton industry has so far failed to take hold, as a recent article in Singularity Hub explained. Small successes in rehabilitation exoskeletons have not yet led to wider adoption of the technologies in industry. However, two developments this year suggest that exoskeletons could be about to make a significant entrance into the automotive industry.
In August 2018, Ford announced that it is rolling out 75 EksoVests (a passive upper-extremity exoskeleton) to 75 of its automotive plants worldwide. This is the largest adoption of exoskeletons by a company yet.
At the same time, German artificial limb manufacturer Ottobock announced in September 2018 that is was in talks with Volkswagen about rolling out its Paexo (another passive upper-extremity exoskeleton) in their manufacturing plants, following successful tests with 30 of their workers in Bratislava.
Both of these developments address the same problem in the workplace. Workers have to reach above their heads thousands of times a day when working on the underside of cars. The passive exoskeletons take some of the weight from their shoulder, allowing them to work without risking upper body injuries.
The exoskeleton industry needs more of these keystone applications for it to succeed. Just as cobots really took off when they found their keystone applications (machine tending, pick and place, etc) exoskeletons will grow when they become indispensable for some tasks.
- Read also: What Are the Best Collaborative Robots?
How exoskeletons could help your business
The main benefit of exoskeletons is one which is also a benefit of collaborative robots. They reduce ergonomics issues, which are a major cause of musculoskeletal injuries in the workplace. This type of injury is very common and can be both devastating to the worker and to the company.
The best way that you can start thinking about these ergonomics issues is to do an ergonomics review. We introduced how to do this in the article "Robots Can Help Reduce 35% of Work Days Lost to Injury."
Exoskeletons may be the solution to your ergonomics issues. However, collaborative robots could also be a solution.
One thing seems certain: we'll be seeing many more exoskeletons in the coming years!
Where could exoskeletons be applied in your business? Tell us in the comments below or join the discussion on LinkedIn, Twitter, Facebook or the DoF professional robotics community.
Leave a comment