Top 7 Robotic Applications in Food Packaging
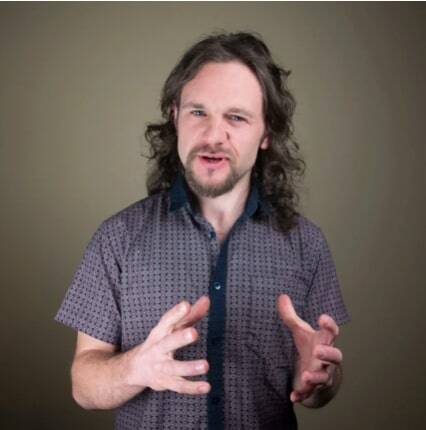
Cakes, creams, lettuce and milk. Robots can package them all! Here are seven great robotic food packaging applications.
Packaging is one of the more established robotic applications in the food industry. The uniform nature of products at the packing stage makes it simpler to automate than tasks earlier in the food supply chain. Tasks in agriculture and food manufacture are harder to automate with robots, but producers are starting to introduce them.
In the previous article, we showed how robotics is transforming the entire food production industry. Here we introduce the top seven food packaging applications, covering all three stages of the process: primary packaging, secondary packaging and tertiary packaging.
1. Pick and Place of Randomly Oriented Foods
Processed foods are often uniform in size and shape, making them easy to handle with a robotic gripper. However, automated food processing machines often produce products which are randomly oriented and distributed.
Robots are a very popular solution for packaging randomly placed products. With a simple pick and place action, they can simultaneously identify, align and place the product. The non-robotic alternative would be to use fixturing, which is inflexible to changes in products and can take up a lot of space.
This video from ABB shows a delta robot placing randomly oriented sticks of salami into individual packets. The system uses robot vision to detect the orientation of products.
2. Raw Food Packaging
Primary packaging involves taking raw or processed food products and wrapping them. The packages can vary hugely in size and shape, depending on the food. This makes some products difficult to handle with a robot. Processed foods (like cookies) are often easier to grasp due to their uniform size, but raw foods (like broccoli) can present more of a challenge.
This video from FANUC shows robots being used at various stages of the food process, including during primary food processing and quality analysis. The final stage shows individual lettuce heads being placed into clear plastic packaging.
3. Depanning
If you have ever baked cakes at home, you will know that removing cakes from a pan can be a tricky task. Mass produced baked goods are often cooked in large pans. Robots are one way to remove the products for primary packaging.
Robotic depanning usually involves picking up an entire tray of baked goods using a specialized depanning tool. Each baked product is grasped by a vacuum or by small pins.
4. Denesting
Denesting involves removing an empty package from a stack. It often performed in conjunction with robotic depanning — the denesting robot removes a package from the stack and the depanning robot places the baked goods inside it.
This video from Precision Automated Technology shows a depanning and denesting robot working together to package cupcakes into plastic trays. The challenge for this application was to produce a packaging system which could handle different products in the same process without taking up too much of the factory floor. The alternative would have been to use interchangeable conveyors but this would not have been as cost effective.
5. Boxing
Secondary packaging involves taking individually packaged products and grouping them into boxes or cases. The products are already sealed from the environment so this stage does not risk contaminating the food. As a result, these tasks are often simpler to implement robotically.
Collaborative robots can be used in a variety of secondary packaging applications, including handling delicate foods. This case study from Universal Robots shows how Italian egg producer Cascina Italia uses a UR5 robot to arrange filled egg boxes into a larger cardboard box.
Collaborative robots can even handle packages which are challenging to grasp. This video from Orkla shows how a specialized gripper allows the UR10 robot to pick and place flexible bags of vanilla cream into cardboard boxes. The company reports the ROI of the robot was only six months.
6. Palletizing
Tertiary packaging involves taking boxes of product and preparing them for shipping, often by stacking them on pallets. Palletizing is a common robotic application in the food and beverage industry. We previously showed how it can be applied to craft breweries to boost production and reduce the risk of worker injury.
This video shows how Atria Scandinavia have integrated three Universal Robots into their production line. The first robot places lids on plastic tubs (primary packaging), the second robot packages those tubs into a box (secondary packaging) and the third robot palletizes the boxes (tertiary packaging). This is a great example of how a small producer can use robots for every stage in the food packaging process, allowing human workers to carry out the more value-added tasks.
7. Warehousing
We have discussed previously how automated warehousing can give a competitive advantage to food producers. Once products have been packed onto pallets or cages, the task of transporting pallets can be very labor intensive, especially when high numbers of product are being warehoused.
The Arla dairy in the UK produces 1.5 million litres of milk every day. This report shows how they have integrated 90 Autonomously Guided Vehicles (AGVs) into their factory to move packaged bottles of milk, in a similar way that Amazon uses the Kiva warehousing system.
The food industry has embraced robotic packaging for some years now. This is likely to increase in the coming years, especially in the secondary and tertiary packaging stages. Collaborative robots now bring the advantages of autonomous packaging to smaller producers who work at much lower volumes.
What are your favorite applications in robotic food packaging? Tell us in the comments below or join the discussion on LinkedIn, Twitter, Facebook or the DoF professional robotics community.
Leave a comment