How to Improve Object Pick-up With Sensors
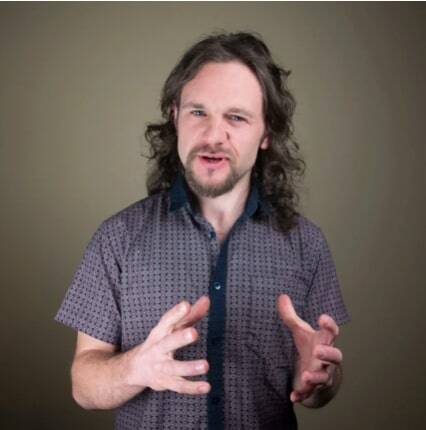
Posted on Aug 02, 2016 in Robot Sensors
5 min read time
What's the best way to detect if an object is ready to be picked up? There are various sensing technologies you could use. In this article, we look at four different options for object pick-up and find out how to choose the best sensing option for you.
In robotics, there are often multiple ways to solve the same problem. This is especially true when we're talking about adding extra sensors to a collaborative robot. There are many different sensing technologies and it's a challenge to know which one is right for your application. That's why we've released a new eBook "Adding Extra Sensors: How to Do Even More With Collaborative Robots." It guides you through the process of assessing your application for extra sensors and selecting the best sensor for your business.
One task which benefits from additional sensors is object pick-up. Sensors allow your robot to accurately pick-up objects by detecting the object position and even orientation. However, there are are several ways you could achieve this, with varying levels of complexity and cost. In this post, we're going to look at four of the ways you can improve part pick-up, both with sensors and without. We only give a brief introduction here, but you can find more detailed information in the eBook.
Fixturing - The Sensorless Option
Fixturing is a well established method of aligning objects in industrial automation. It involves using purely mechanical or electromechanical fixtures to clamp, support or otherwise locate objects in the workplace. Depending on your application, this can range from very simple (e.g. a funnel to orient the objects) to quite complex (e.g. electromechanical clamps which automatically close around the objects).
The advantage of using fixturing to orient objects is that it is relatively low-tech and so requires little training. However, fixtures can be costly and they are usually not flexible to changes in the process.
In-Built Part Detection - The First Option
As we discuss in the eBook, it is important to consider the in-built sensors available on your collaborative robot before looking to purchase an additional sensor. There may be ways of improving your process simply by better utilizing the technology you already have. One example is if your robot gripper has in-built part detection sensing. The Robotiq Grippers, for example, have an object detection feature which allows them to detect if the Gripper has grasped something. This may be sufficient for your application if you only need a sensor to detect if an object is present or not. However, if you need to detect the object's position you may need a more advanced sensor.
Part Detection Sensors - The Low-Tech Option
These are some of the simplest sensors available for industrial robots and are used extensively in automated factories. As the name suggests, they detect whether or not a part has arrived at a particular location. Some of them also allow basic part identification, e.g. by color or reading labels. Thanks to their simplicity and relatively low cost (though this varies widely), part detection sensors can be a good choice as a first sensor to add to your collaborative robot. However, their simplicity also means that they are not as flexible as other sensors, particularly vision which shares some technological similarities with part detection.
There are several types of part detection sensor, which can each detect different properties, including presence, distance, shape, color and orientation. They also use a variety of technologies, including photoelectrics, ultrasound, laser, capacitance and inductance. Find out more about them in the eBook.
Robot Vision - The High-Tech Option
Properly implemented, robotic vision offers high flexibility gains for a collaborative robot. It has several benefits over the solutions described above, such as allowing a robot to manipulate different parts without reprogramming in between, picking up objects of unknown position and orientation and correcting for inaccuracies in the placement of the robot itself.
There are a few different options for robotic vision systems but one way to categorize them is to split it into two separate types: 2D Vision and 3D Vision. Fixed 2D Vision is very common in manufacturing industries. It usually involves a simple, fixed digital camera which is aligned so that objects pass through its field of vision. A more flexible option is to attach the 2D camera to the robot's wrist. This is the approach used in the Robotiq Wrist Camera. The more advanced 3D Vision, on the other hand, often involves a combination of lasers and 2D cameras.
What's the Difference Between Each Option?
As you can see, there are quite a few sensing options, even for the simple task of object pick-up. Different sensors will offer different advantages to your unique pick-up needs. The main advantage of adding any additional sensor is increased flexibility. However, as with any new technology, this flexibility comes with a cost, both in terms of budget and time. The more sensors you add, the more complex your system becomes. The more complex the system, the more work is required to integrate the sensor into the system and maintain it later.
It is not necessarily the case that adding the most advanced sensor is better for your application, as advanced sensors introduce more complexity. For example, 3D Vision systems have the potential to allow very flexible location of objects, but they can introduce more restrictions than 2D Vision setups due to their complex technology.
How to Pick the Right Sensing Technology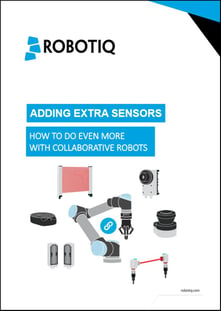
There's no "one size fits all" when it comes to robotic sensing. Therefore, it's important that you carefully consider the options and assess your task before choosing to invest in an extra sensor for your collaborative robot.
Our eBook "Adding Extra Sensors: How to Do Even More With Collaborative Robots" takes you right through this process. It gives examples of how the different sensing technologies can be applied to particular applications and goes in-depth about four of the top sensing technologies for collaborative robots.
How do you currently ensure objects are in the right position for pick-up? Could sensors improve your process? What extra information would you like to see in the eBook? Tell us in the comments below or join the discussion on LinkedIn, Twitter or Facebook.
Leave a comment