How to Include a Force Sensing in a Robot Cell Design
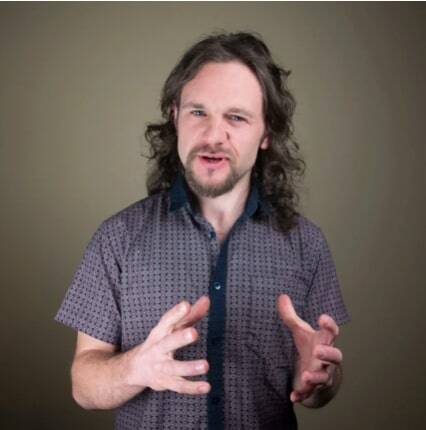
Posted on May 17, 2021 in Robot Sensors
5 min read time
You have decided to include force sensing in your robot application. Perhaps your task requires tactile feedback, flexibility, or you need the robot to apply a constant force on the workpiece.
How should you include force sensing in your cell design?
There are many options for force sensing on the market. Some of them are well suited to robotic applications while others are less suitable.
There are different sensors from different suppliers, each of which has varying advertised features. It's hard to tell how each force sensing option will affect the design phase of your robot deployment.
Force sensing is traditionally considered to be quite complex in robotics.
What features should you prioritize so your design phase is as easy as it can be?
How can you ensure that you don't make your job unnecessarily difficult?
The days of complex force sensing design are gone
Not long ago, the main option for adding force sensing to a robot was to choose a 6-axis force sensor using strain-gauge technology. These used to be complex to integrate, requiring in-depth knowledge of force control techniques and advanced programming skills.
Many people still assume that this is the case. They think that they will have to integrate the force sensor into the robot design themselves. They need force sensing for a particular task and they assume they will need to get down to some serious robot programming.
But, those days are gone.
There are now plenty of options for force sensing that don't require you to get your hands dirty with complex programming and algorithms. With some force sensing options, adding the sense of touch requires almost no effort on your part.
What do you need from robot force sensing?
The first thing to get clear on is exactly what capabilities you require from your chosen force sensing option.
Look at your robot application and identify which aspects of the task will benefit from the addition of force sensing.
You can ask yourself questions like:
- What task am I performing?
- Which specific steps in the task will need force sensing?
- What type of force sensing will each step need? — e.g. force feedback for detailed insertion, weight measurement, the application of a consistent force along a path.
- How precise will the force sensing need to be to achieve this?
- What other aspects of the task could benefit from force sensing but don't necessarily require it?
You don't need to be completely clear on every aspect of the task yet. However, it helps to get a reasonably complete picture of how force sensing will affect your chosen task.
The 3 basic force sensing needs
Whatever your specific needs, they can usually be grouped into 3 basic categories when it comes to finding the best solution for you.
The 3 basic force sensing needs are:
Ease of use: Integrated force sensor
If you want to reduce the integration time and effort as much as possible, the best option is likely to be a collaborative robot with an integrated force-torque sensor. These weren't available a few years ago but now they are both available and reliable.
The best example of this is probably the Universal Robots e-Series, which includes force-torque sensing in the robot itself. The supplied software can handle most situations you're likely to encounter without requiring complex programming.
Flexibility: 6-axis force-torque sensor
Of course, many robots are not available with an integrated force sensor. In this case, the best and most common option is to use an external force-torque sensor.
This is also the most flexible solution as you can mount the sensor in the most useful position for your specific task. In some cases, it will make more sense to mount the sensor externally rather than on the end of the robot itself.
Adding a force-torque sensor doesn't need to be complex. Certain sensors are very easy to use for a range of robot applications.
Specific needs: Another technology
In some situations, 6-axis force-torque sensing might not be appropriate or necessary for your specific needs.
For example, perhaps you only need to detect collision events when the robot presses a button. In this case, it might make sense to use a simple force sensitive resistor attached to the button if you don't need more complete force sensing elsewhere.
How to incorporate force sensing into your design
Once you've decided on the type of sensor that you need, your design steps will become clearer.
For integrated force sensors or external sensors with easy integration options, there is very little you need to add into your robot cell design. There are a few programming options that you should include when you get to the integration, but all the hard work that is traditionally associated with force sensing is now handled for you by the robot's software.
For less intuitive force-torque sensors and other sensing technologies, your design work will vary. You will need to plan the cabling and connections going to the force sensor. You will probably have to design the interfaces in programming to make the sensor operate as you intend it to.
If you have any specific questions about how to incorporate force sensing into your unique design, please let us know in the comments or post a question on the DoF forum.
Where to find the right sensor
Which force sensing option is going to be the best for your unique situation?
The answer depends on your application. However, it makes sense to look for the most intuitive force sensor available for the needs that you have identified.
If your robot doesn't have an integrated force sensor, you could take a look at the Robotiq FT 300-S. It is a fully-fledged 6-axis force-torque sensor that is designed for easy integration.
Which aspects of robot cell design are you currently struggling with? Tell us in the comments below or join the discussion on LinkedIn, Twitter, Facebook, or the DoF professional robotics community.
Leave a comment