German Space Agency, DLR, Using 3-Finger Adaptive Gripper
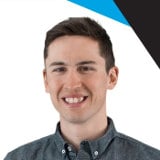
Posted on Jun 15, 2015 in Robot Grippers
3 min read time
Robotiq Grippers in space? Not quite yet. However, some of our international sales reps have spent time at the German Space Agency (DLR: Deutsches Zentrum für Luft und Raumfahrt) and have had the chance to observe simulations using the 3-Finger Adaptive Gripper. The concept and technology is quite impressive and the potential is even more incredible. Here's what one of our representatives had the chance to see at DLR.
To give you some context, the robotic cell is supposed to simulate a reloading operation between two satellites. So in order to simulate this situation you have got to first recreate the environment in which the satellites are acting. You then have to simulate the reloading process using a robotic arm and in this case the 3-Finger Adaptive Gripper. To have a better idea, take a look at the video below.
The Cell
To recreate the satellite context of weightlessness, the DLR team is using two KUKA KR1000 TITANs to lift the satellites (Scale 1:3). The robots used are mounted with force torque sensors to recognize any force applied on the satellite itself. Since the satellite will be in a free-floating (no gravity/ no air friction zone), if you ''push'' the satellite, it will move consequently. So by using force torque sensors, the robot software can interpret the force applied on the satellite. Doing so, the force applied from one satellite to another increases the complexity of the handling task since applying (even a small) force will cause a reaction with the other satellite.
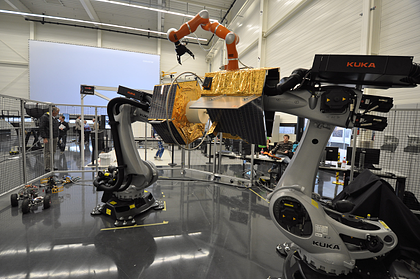
This being said, the manipulation process is done with a KUKA LBR iiwa and a Robotiq 3-Finger Adaptive Gripper. The robot arm is also equipped with a vision system to give instant feedback on the grasping status of the Gripper. All these devices work together to handle the second satellite for the reloading process. They have chosen the 3-Finger Gripper due to its wide stroke. With the fingers wide open, this leaves more place for the satellite's handle and thus more opportunity to make contact. And the fact that the Gripper can grasp using an encompassing method insures that the satellite handle remains in the clasp of the fingers of the Gripper.
Finally another cool aspect about this cell is that it can be operated by telepresence. This means that another KUKA robot is connected in parallel and moved by a human that has access to the vision feedback and can control the Gripper using his/her fingers. So basically, the Gripper is imitating the motions of the human hand in real time! This is VR (virtual reality) in reverse, since instead of using motions or sensors on a glove to imitate a motion in a simulation, they are going one step further and using VR to move in a simulation which then actually moves in reality! You can observe how DLR is doing this in the video above.
The Application
As you probably noticed, the main goal of this simulation is not to launch the satellite straight into orbit. Since it is a scaled down version of the potential platform, it is simply to develop the knowledge and troubleshoot any potential issues with this application. To have further information on what the real life project looks like, you can take a look at the video below or follow this link.
Well, we are really pleased that DLR has determined that our product meets their unique and stringent qualifications and are looking forward to continuing our partnership. Hopefully, you have enjoyed this application as much as we have, it is not every day that you get to see the end result of product you have worked on being used in such a fascinating and awe inspiring project. We are thankful to DLR for having chosen our product. To get more information on other inspiring projects using our 3-Finger Adaptive Gripper, you might as well drag your cursor to the big colored button at the bottom of this blog post.
Related Articles:
Grasp Planning Control with the 3-Finger Robot Gripper
A Robot Services Defective Satellites to Prevent Space Debris
Leave a comment