Choosing the Right Gripper for Your Robot
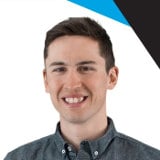
Posted on Nov 07, 2014 in Robot Grippers
4 min read time
Most of the time our blog posts are about functionalities or how a specific kind of gripper works. Although, we have never talked about which gripper can fit on a given robot. In fact, this could be a real puzzle for the end user. What do you need to look at and what are the main tips for choosing the right gripper for your robot.
Energy Source
There are four groups of grippers overall; electric, pneumatic, magnetic, and hydraulic. Depending of your application(s) you have to figure out which gripper will meet your application requirements the best.
Most grippers in the electric gripper category can fit on most robots. In fact, most industrial robots are fed by electricity, so there is usually no additional problem in feeding an electrical gripper. With some electric grippers, self-blocking systems are embedded into the gripper which allows it to maintain the object in place without using extra energy during the clamping motion. In case of a power shut down, the object can stay grasped by the gripper.
Magnetic grippers are also electrically fed, but because of the physics of the way they work, they don't have the auto-blocking principle, which means they have to be constantly fed energy throughout the entire operation every time they move an object, and in the case of a shut down, the part will fall.
Pneumatic and hydraulic grippers though, this is another thing. For both technologies you need to have external sources (i.e. a compressor) that build pressure for the air or fluid in the hydraulic/pneumatic lines. These lines means that the robot must be tethered by being nearby this source (ideally) and finally these lines somehow have to be fitted onto the robot. This requires supplemental material. Finally, this type of equipment is not ''leakage proof'' which means problems can and do occur. This will likely result in a reduction of the pressure in the lines and a corresponding reduction of pressure at the gripper level. If the system is shut down, air or fluid pressure can be cut and the gripper can open or the suction provided will stop; releasing what ever was being held.
Payload and Gripper Weight
Payload can often be mixed up with the weight of the gripper (understand the difference by reading this article). In actuality both specifications need to be studied. In fact, once you have chosen your robot, it has a given payload which is allowed for it. And you have to consider that the weight of the gripper has to be included in this payload. You also have to make sure that you are using a gripper that can grasp a sufficient payload for your application. For example, if you are using a gripper with a 2kg payload and a robot with a 10kg payload, you are still limited by the gripper. Your gripper and part may come in under the necessary weight for the robot, but your gripper still can't handle more than 2kg.
For example, our 2-Finger 85 Gripper weighs about 900g (without accessories) and can manipulate a part weighing up to 4kg. A Universal Robot (UR5) has a 5kg payload. If you fit a 2-Finger 85 on a UR5, you have to consider the maximum payload of the robot (5kg) and the weight of the gripper (900g=0.9kg). So basically, you can pick up an object weighing up to (5kg-0.9kg= 4.1kg). So the 2-Finger 85 has a payload of 4kg. And when used with this robot, you are then maximizing the full power of the Gripper.
On the other hand, our 2-Finger 200 Adaptive Gripper weigh 8.9kg which means it should not even be fitted on the UR5.
Note that this calculation is based on estimates, a real payload calculus should be done once your equipment is selected with the real parts you will be manipulating.
Mechanical Fit
The mechanical fit can be a really restricting aspect of the fit between a robot and a gripper. The mechanical fit means that the gripper is compatible with the physical attributes of the robot wrist. Most of the time an adapter plate can be fitted between the gripper and the robot. Although, some gripper companies don't provide every adapter plate for every given robot model. Make sure to ask your vendor or application engineer to know if the gripper will mechanically fit on your robot.
Communication Protocol
This compatibility also applies to the programming side of things. In fact, to make the gripper respond to its commands, the communication protocol between the robot, the gripper and the controller must be compatible. Make sure to ask your vendor about all the different communication protocols out there and which ones should be used with your robot arm and gripper.
That's pretty much it. You should also consider other aspects in your robot/gripper fit. Things such as your process, your environment and many more factors can make the difference between a good match for your application and a lot of trial and error. Make sure to follow the link below to check out more information on which gripper can fit your applications.
Leave a comment