More Than Just a Parallel Gripper: How Does It Work?
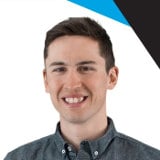
Posted on Oct 23, 2014 in Robot Grippers
4 min read time
We have been providing different types of Adaptive Grippers for industrial and research applications since 2008. However, what does Adaptive really mean? And what is the difference between our Grippers and other regular parallel grippers. This blog post will give you the main points of what is so unique about our Adaptive Grippers.
Self-Adaptive Mechanism
Our Grippers have a patented mechanism that makes them really unique. In fact, by being underactuated (less actuators than joints), the finger mechanism can adapt itself to just about any shape. Each finger is independent. This means that if a shape is tapered for example, each finger can close to the exact diameter of the section. This is basically the reason for the ''Adaptive'' nomenclature.
Also, even if each finger is independent from every other finger and can adapt to the shape in front of it, you should also notice that each phalanx is also independent. This means a single finger can grab an object, make contact with the object or perform a certain operation. A good example would be the 3-Finger Adaptive Gripper that is used on some of the DARPA Challenge robots. One of the stages of the competition requires the robot to grab a drill and to execute maneuvers with it. If you have ever taken a drill in your hand, you probably notice that it is full of uneven shapes and the trigger is not at the same height as the handle or other parts. So being able to manipulate this type of uneven and oddly shaped object is not easy and an important feature of the self-adaptive mechanism of the Gripper.
Encompassing Grip
Adaptive Grippers, as I said, are able to adapt to a very different kinds of objects. When the object is small, the Gripper can literally encompass it and lock its fingers around it. This means that the Gripper is no longer counting on its fingertips to retain the object, but more on its entire mechanism. Imagine grabbing a water bottle using your fingertips or by encompassing your fingers around it... I'm sure you can imagine which way is more secure? Well, this is why our robot hands have these specifications. By increasing the grasping surface and number of contact points, the weight of the object is then spread around all the phalanxes and this provides a more solid grip. A Gripper can secure an object with its system of self-locking mechanisms and even grab heavier objects without the risk of dropping them. For example the 3-Finger Adaptive Gripper is usually able to grasp objects up to 5.5lbs or 2.5kg with its fingertips and can grasp up to 22lbs or 10kg in the encompassing mode.
Pinch/Parallel Grip
However, even if the encompassing grip mode is more secure to use, some applications need to use the parallel grasping mode. This mode is basically like most of the grippers out there, it can grasp and lock its finger on the object by keeping its fingertips parallel one to each other. All though with the Adaptive Gripper the force applied on the object can be set directly in the robot/gripper program. This means that some fragile parts can be grasped and there is no risk of damaging or destroying them because the fingers can control the amount of force applied.
Internal, External, Combined
The beauty about Adaptive Grippers is the fact that there is no need to adapt the gripper to the applications. In fact, as most of the grippers out there need to have custom fingers created for each object they grasp. The Adaptive Grippers can generally use the same fingertips for any grasping position. All the Grippers can perform internal, external and combined grasping manipulations. An external grip would take hold of a box by its outside surfaces or geometries. The internal grip is usually used when a cylinder is grasped by its internal surface or diameter. A combined grip would be a combination of internal and external contact.
For example, a C-Channel rail might not be able to be grasped by its internal geometries, because this would be unstable and it might be too large to use the external grip. This is where the combined grasp is practical. In fact, the Adaptive Gripper can pick up even a thin wall surface and carry the C-Channel without any problem. Thanks to its slim fingers, it can go into a wide range of places and geometries.
So this is basically why our Adaptive Grippers are so unique. A one of a kind principle, flexibility, that allow the user to accomplish a lot of different applications with the same Gripper. To read more about our Grippers, follow the link below.
Leave a comment