How to Handle Fragile Parts with Robotiq Grippers
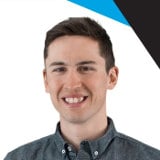
Posted on May 13, 2014 in Robot Grippers
3 min read time
As you may be aware, robots are well known for their high gripping force and power. But as robotic applications are expanding, not every application needs to have a strong grasping force. In fact, fragile parts need to be handled gently by the robot gripper. Many robotic grippers out there only have 2 positions (either full on or full off), however our flexible end effectors can handle a lot of different shapes and at different forces. This being said, by using our flexible industrial Robot Grippers, you can handle fragile objects without breaking them. Here are 3 aspects that need to be considered when looking into handling fragile parts with our Grippers.
Grip force control
The gripping force parameter can be set at different levels. For the 2-Finger Gripper-85, the lowest force is 30 N and in the case of the 2-Finger Gripper-200, the lowest force is 150 N. Concerning the 3-Finger Gripper, the lowest force is 15 N. The Robot Gripper will always try to reach the preassigned closing position. However, if the fingertips hit an object before its prescribed position, the force will ramped up to reach the preassigned level. As this level is reached, the Gripper will stop in a self-locking position. There is a certain delay before the Gripper ''understands'' that it is holding an object, so the slower the closing speed, the less force you will apply before stopping.
Force distribution
You may already know that if the same force is applied on a larger surface, the pressure will be reduced. By using this principle, we have found a way to increase the contact surface when grasping an object. By using the encompassing mode, it is possible to use many contact points. The difference between handling an object by using 2 fingers and handling it with your whole hand is that the second option will be easier and softer, because it involves many contact points and force which is spead out over the object. The same thing holds true for our Gripper. Using the encompassing mode, you want to position the object between the fingers and the palm. Another advantage of using the encompassing mode is that you are able to reduce the force needed to handle the object since it is surrounded by the fingers. A simple way to distribute the force evenly on a given object is to adjust the fingertip design. By using different materials or sizes, you can create a supplementary surface and reduce the pressure on the object.
Gripper fingertip compliance and position control
For some applications, the minimal gripping force will still be too high. To counteract this situation, you can make adjustments by using the fingertip pad compliance (for rubber fingertip equipped Grippers only), combined with the positioning of the Gripper. Ideally, you want to send a close command to the Gripper at a position slightly smaller than the object. Because this position is so close to the part size, the Gripper will not ramp the force up to the preassigned level. Rather, it will stop at the final prescribed position. The force will then be exerted on the compliant pads, causing them to deform slightly. Again, different pads with different stiffnesses can be used.
The 3 topics discussed in this article describe how to handle fragile objects with the built-in features of the Grippers. Another way to grab fragile parts would be to use different tactile sensors. These sensors need to be adapted to the robot gripper. However, companies such as SynTouch have integrate their sensors directly into our Gripper. You might want to take a look at the different sensors out there and see if they can be fitted onto your robotic gripper and used for your applications.
By using these simple ideas, it will now be possible to handle different kinds of objects; for example, small fragile objects such as eggs, fruit or laboratory test-tubes. There are a lot of possibilities regarding how to handle sensitive objects. In fact, different gripping positions can be used for the same applications. Contact us to get specific info relative to your material handling issues and we will do our best to help you find a solution for your problem.
Leave a comment