7 Types of Industrial Robot Sensors
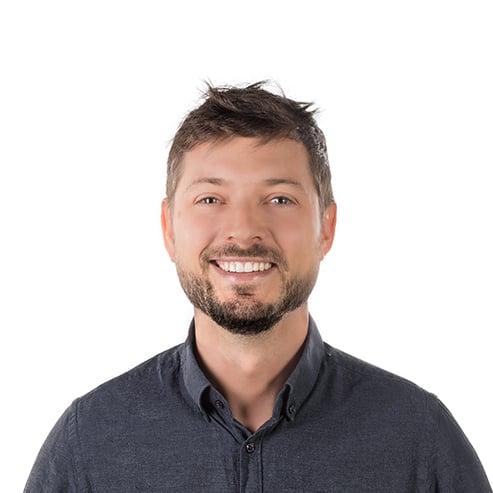
Posted on Oct 01, 2014 in Robot Sensors
4 min read time
In the industrial and automation world, machines need sensors to provide them with the required information to execute a proper operation. A lot of sensors can be added to different robots to increase their adaptability. We see a lot of collaborative robots having integrated force torque sensors and cameras in order to have a better perspective on their operations and also to provide the safest workspace. This made us think it would be a good thing to enumerate the different sensors that can be integrated into a robotic cell.
2D Vision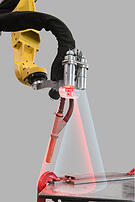
2D is vision is basically a video camera that can perform a lot of different things. From detecting movement to localization of a part on a conveyor. 2D vision has been on the market for a long time and is here to stay. Many smart cameras out there can detect parts and coordinate the part position for the robot so that it can then adapt its actions to the information it receives.
3D Vision
3D vision is much more recent phenomenon as compared to 2D vision. A tri-dimensional vision system has to have 2 cameras at different angles or use laser scanners. This way, the third dimension of the object can be detected. Once again many applications use 3D vision. Bin picking, for example, can use 3D vision to detect objects in a bin and recreate the part in 3D, analyze it and pick it the best way possible.
Force Torque Sensor
While vision gives eyes to the robot, force torque sensors give touch to the robot wrist. Here the robot uses a force torque sensor (FT sensor) to know the force that the robot is applying with its end of arm tooling. Most of the time, the FT sensor is located between the robot and the tool. This way, all the forces that are applied on the tool are monitored.
Applications such as assembly, hand-guiding, teaching and force limitation can be done with this device. We have developed a technology called Kinetiq Teaching that allows industrial welding robots to be taught via hand-guiding. All of this using a force torque sensor to monitor the motions of the ''teacher''. We also have a FT Sensor that is sold separately to accomplish any number of applications that might require force sensing.
What if you want to detect the force applied on the robot arm? For example, you want to know if the robot is in collision with something or someone? Well, the next type of sensor answers all these questions.
Collision Detection Sensor
This kind of sensor can have different forms. As the main applications of these sensors is to provide a safe working environment for human workers, the collaborative robots are most likely to use them. Some sensors can be some kind of tactile recognition systems, where if a pressure is sensed on a soft surface, a signal will be sent to the robot to limit or stop its motions.
You can also see this kind of sensor directly built into the robot. Some companies use accelerometers, some use current feedback. In either case, when an abnormal force is sensed by the robot the emergency stop is released. This provides a safer environment. Although, before the robot stops you will still be kicked by it, right? The safest environment is an environment with no risk of collision. This is what the next sensor is all about.
Safety Sensors
With the introduction of industrial robots in collaborative mode, industry has to react with a way to protect its workers. These sensors can really appear in a lot of different shapes. From cameras to lasers, a safety sensor is designed to tell the robot that there is a presence around it. Some safety systems are configured to slow down the robot once the worker is in a certain area/space and to stop it once the worker is too close.
A simple example of safety sensors would be the laser on your garage door. If the laser detects an obstacle, the door immediately stops and goes backwards to avoid a collision. This can be a good comparision to what safety sensors are like in the robotic industry.
Part Detection Sensors
For applications that require you to pick parts, you probably have no clue if the part is in the gripper or if you just missed it (assuming you don't have a vision system yet!). Well, a part detection application gives you feedback on your gripper position. For example, if a gripper misses a part in its grasping operation, the system will detect an error and will repeat the operation again to make sure the part is well grasped.
Our Adaptive Grippers have part detection systems that don't need any sensors. In fact, our Grippers are designed to grasp parts with a given force. So the Gripper doesn't need to know that the part is there or not, it will only apply enough force to get the best grip on the object. Once the required force is reached, you know that the object is in the Gripper and that it is ready for the next step in the operation.
Others
Of course there are a lot of other sensors that can be fitted to your robotic cell that are very specific to your application. Sensors that are capable to do seam tracking in welding operations are a good example where a specific sensor is necessary.
Tactile sensors are also becoming more popular these days. This kind of sensor is, most of the time, fitted on a gripper to detect and feel what is in it. Sensors are usually able to detect forces and draw an array of vectors with the force distribution. This shows the exact position of an object and allows you to control the position and the grasping force of the end effector. Some tactile sensors can also detect heat variation.
Finally, sensors are key components to leveraging software intelligence. Without such sensors, advanced operations wouldn't be possible. They bring a lot of complexity to the operation, but they also insure good control during the process.
Leave a comment