Which is Better: a New Machine or a Dual Gripper?
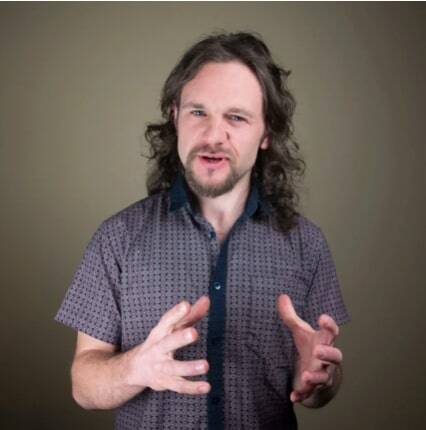
Posted on Mar 21, 2018 in Robot Grippers
18 min read time
When you're attempting to resolve a bottleneck issue, you might be wondering whether it's better to invest in a parallel machine or a dual gripper. Here's how to find out easily!
What's the best way to overcome a bottleneck in your manufacturing cell? Should you buy a whole new CNC machine? Or should you attach a dual gripper to your collaborative robot?
Bottlenecks can severely reduce the productivity of your process. Sometimes they're resolved by basic process optimization, but other times you may have to invest in a new technology.
This article will show you how to calculate the potential benefits of adding a parallel machine to one step in your process. Then, you'll learn how to compare it with the potential benefits of a dual gripper, so you can decide which option is best for you.
Continental Automotive Spain uses the Robotiq 2-Finger Adaptive Robot Dual Gripper for quality testing.
Is your machining cell causing a bottleneck?
The easiest way to identify the source of a bottleneck is to look at where products are starting to stack up.
Do you find lots of Work in Progress (WIP) piling up at your machining cell? Is the cell part of your Critical Path? If so, the cell could be causing a bottleneck in your process.
Using a collaborative robot for machine tending is a great way to reduce bottlenecks in a manufacturing cell. If you haven't started automating your machine tending yet, make sure to check out our Machine Tending Playbook.
However, if your manufacturing cell is still causing a bottleneck – even with a machine tending cobot – there are three great ways to give it a performance boost.
How to boost a cell's performance with parallel machines, dual grippers, or both
According to researchers at universities in Texas and New York, there are three main ways to improve the productivity of a robot-tended machining cell: parallel machines, dual grippers, or both. Let's have a look at the three options.
The parallel machines solution
If one CNC machine in your cell is operating at full capacity, you may be able to resolve the bottleneck with a parallel machine. This means adding a whole new CNC machine to perform the same task as the overloaded CNC machine (see diagram below).
There are many potential advantages to adding a parallel machine:
- It means that multiple value-added tasks can take place at the same time.
- It's simple and quick to implement – just install one extra machine with the same program.
- It doesn't require any new knowledge from the team.
But there are also some potential disadvantages:
- It's costly — an extra CNC machine is a big investment.
- It may not solve the bottleneck — the machine's load and unload times could still restrict the flow of parts.
- It takes up a lot of floor space.
The dual gripper solution
If your cell is being held up because it of how long it takes the machine tending robot to load and unload the CNC machines, a dual gripper could be an option. Check out the diagram below for an idea of how that would work. (We also recommend reading our previous article for an introduction to dual grippers.)
The potential advantages of using a dual gripper are that:
- It's inexpensive to implement, requiring only a connector plate and an extra gripper.
- It's flexible regarding future changes in the cell, since robots are easily reprogrammed.
- It takes up no extra floor space.
The potential disadvantages of using a dual gripper are that:
- It may not resolve the bottleneck if loading and unloading time is not the root cause.
- It may require somewhat complex programming, depending on the complexity of the operation sequence.
- It does not increase the number of concurrent value-added tasks.
The combined solution
The final option is to use both a dual gripper and parallel machine. This combines all the advantages and disadvantages of the previous two options.
I'm not going to cover the calculations for this setup in this article, because my purpose here is to help you compare the first two options. But as you can imagine, the combination is usually better than either option individually. If you are interested in doing the calculations for this option, you'll find the equations in Section 6.3 of the original research paper.
How to calculate potential improvement with a parallel machine
Using the equations proposed by these researchers, you can calculate the performance improvement caused by introducing a parallel machine at the machining stage that has the longest processing time.
First, you'll need to figure out the following values:
- Nm – Number of machines.
- Tl – Time to load or unload one machine. This includes dropping off the previous part at the output buffer, picking a new part from the input buffer, and loading this part into a machine.
- Tm – Travel time between two different machines.
- Tp – Processing time (use the longest one out of all the machines).
Then, you're ready to calculate the following two values. The first quantifies the effect of the processing time on the overall cycle time, and the second quantifies the effect of the robot's travel time:
Finally, to calculate the overall "cycle time per unit" for a robot with a single gripper and a parallel machine, simply take the maximum of these two values:
Example calculations
Let's take an example cell. The cell starts with two CNC machines, each performing a different machining step. We'll calculate the effect of adding a parallel machine to one of these steps. The values we'll use are:
- Number of machines (Nm) – 2
- Time to load/unload a machine (Tl) – 10 seconds
- Travel time between machines (Tm) – 5 seconds
- Longest processing time (Tp) – 75 seconds
These will give us the following values for the cycle time per unit:
Because Tparallel 2 is the bigger value, we can tell that the robot's travel time has a greater effect on the overall cycle time than the CNC machine processing time does.
However, as we'll soon see, this doesn't necessarily mean that a dual gripper is better than a parallel machine for this setup.
We can take the same equation that we used in the previous post to calculate the improvement of a parallel machine:
This gives us a value of:
Some examples based on two, three, and four machines
Here are some examples of the improvements brought about by a parallel machine on several different setups, using two, three, or four CNC machines. These are the same setups that I used for my calculations in the previous post about dual grippers, so you can compare all calculations directly. All times are in seconds.
Setup |
Nm |
Tl |
Tm |
Tp |
Tt single |
Tparallel1 |
Tparallel2 |
Tt parallel |
% improvement |
A |
2 |
30 |
15 |
60 |
270 |
112.5 |
270 |
270 |
0.00% |
B |
2 |
10 |
5 |
75 |
130 |
65 |
90 |
90 |
30.77% |
C |
3 |
70 |
5 |
200 |
600 |
165 |
600 |
600 |
0.00% |
D |
3 |
30 |
5 |
180 |
315 |
105 |
280 |
280 |
11.11% |
E |
4 |
60 |
7 |
324 |
670 |
146.25 |
670 |
670 |
0.00% |
F |
4 |
90 |
9 |
900 |
1287 |
321.75 |
990 |
990 |
23.08% |
How to calculate potential improvement with a dual gripper
The calculations for the dual gripper setup are explained in the previous article: How to Calculate the Productivity Boost for a Dual Gripper. Please check out the article to learn how to calculate the potential benefits of using a dual gripper.
Is a dual gripper better than a parallel machine?
The big question is: which option better for you? As is often the case, the answer is not straightforward.
When we the results we obtained here with those of the dual gripper (from the previous article), we get the following improvements to the overall "cycle time per unit" (all times are in seconds):
Setup |
Nm |
Tt single |
Tt dual |
Tt parallel |
% improvement with dual gripper |
% improvement with parallel machine |
A |
2 |
270 |
244 |
270 |
9.63% |
0.00% |
B |
2 |
130 |
96.5 |
90 |
25.77% |
30.77% |
C |
3 |
600 |
591 |
600 |
1.50% |
0.00% |
D |
3 |
315 |
241.4 |
280 |
23.37% |
11.11% |
E |
4 |
670 |
647.6 |
670 |
3.34% |
0.00% |
F |
4 |
1287 |
1081.5 |
990 |
15.97% |
23.08% |
As you can see, no single option is best in all cases. Some setups are better suited to a parallel machine and others to a dual gripper. That's why it's important to run these calculations before you invest in either a parallel machine or a dual gripper, to ensure the solution is sufficient for your productivity needs.
Wondering how you could use a parallel machine or dual gripper in your setup? Got questions about machine tending? Want to share the improvements you calculated for your cell? Tell us in the comments below or join the discussion on LinkedIn, Twitter, Facebook or the DoF professional robotics community.
Leave a comment