When worker safety drives innovation: How one ice cream cone manufacturer is taking care of its people
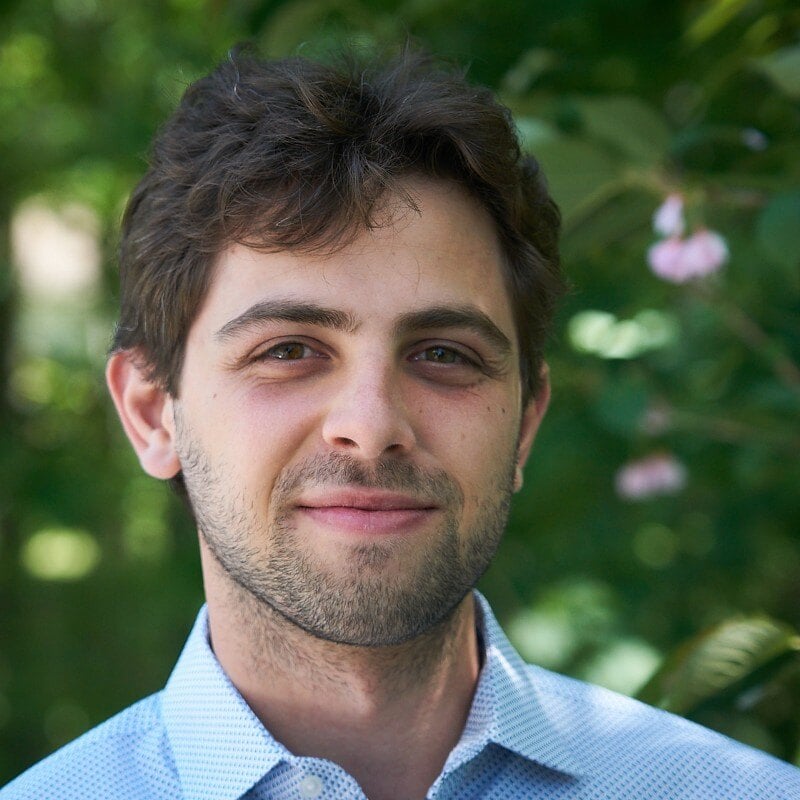
Posted on Apr 03, 2025 in Palletizing
3 min read time
At first glance, palletizing ice cream cone boxes doesn’t sound like a high-risk job. But when those boxes weigh 35 to 40 pounds and need to be stacked shoulder-high, shift after shift, five days a week—you start to understand the strain it puts on people.
That’s exactly what one major U.S. food manufacturer realized. They produce a wide range of cones—waffles, sugar, and cake. Despite their scale and reach, what really stood out to us was something else: their culture.
This company operates as an ESOP—an Employee Stock Ownership Plan—which means every person on the floor has real skin in the game. From the front office to the production line, they all own a piece of the business. And when that’s the case, safety becomes more than a policy. It becomes personal.
Why automate?
It wasn’t a labor shortage that drove their decision to automate palletizing. It wasn’t even about efficiency in the traditional sense. The spark came from a very human place: too many shoulder injuries. Lifting heavy boxes over and over, especially to the top of a pallet, was causing problems. The kind that takes people out of work and puts long-term strain on the team. They didn’t want to wait for the next injury. They wanted to prevent it.
So, they made a move. They chose to bring in a robotic palletizing system—not to replace someone, but to remove the risk from a task that just didn’t make sense for people to be doing anymore.
What made this a good fit?
The technical side was straightforward. The boxes are hefty, they’re well within the payload range of a cobot palletizer. The company already had Universal Robots on-site, so integrating another one with our PE20 was familiar territory.
But the real fit wasn’t about speed or specs. It was about care. They weren’t trying to eliminate a job. The palletizing task was just one of many handled by their team. What they wanted was to eliminate the injury risk. Plain and simple. Plus, the ease of use of the programming interface allowed to upskill some operators who can now use the robot.
A takeaway for food manufacturers
Automation typically gets evaluated through the lens of labor savings. But this story is a reminder: ergonomics matter. Worker safety isn’t a soft metric—it’s a powerful reason to rethink manual tasks. Heavy lifting, repetitive motions, and awkward positions take a toll. And even if you’ve got capable people on your team, that doesn’t mean they should be doing those jobs.
This isn’t about chasing buzzwords like “lights-out manufacturing.” It’s about solving real problems in real plants, with practical tools that work.
And if you’re running a facility where your team is your greatest asset—like this one—you might find that the business case for automation is stronger than you think. For in-depth insights on the toll manual palletizing can take on a company and how automation can alleviate those strains, download our Manual Palletizing Ergonomic Risks ebook by industry expert, Carla Silver.
Leave a comment