The Easiest Way to Automate the Dullest Jobs
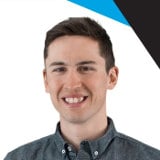
Posted on May 01, 2015 in Automation
4 min read time
Working in an environment involving robots gives me a different perspective on the manufacturing process. When I go to visit customers I always ask myself: ''How can this process be enhanced?'' Not only by using a robotic arm, but how can the process be enhanced to fit the workers needs or make the cycle time faster. There are various things that can be done and almost every working station can be enhanced in someway. So when I see a plant using humans to perform the dullest, most repetitive, dangerous tasks I am always amazed and want to get the worker out of there and give him a post that is more challenging and that requires more intelligence and dexterity. Here are a couple of tips to automate the dullest jobs in your plants.
First of all, you need to know that using a robot is not necessarily a faster option than using a human. It only removes the human from difficult tasks and transfers the work load onto the robot. Especially with the introduction of collaborative robots like Baxter, it is not a question of speed anymore, but more a question of having a more efficient production with happier workers.
Large Parts to Handle?
In the following video, the Baxter robot is grabbing 4 packages at a time and transferring them to a conveyor. First thing to notice is that grabbing 4 package at a time for a human worker can be more complex than for a robot. In fact, the robot is using a special tool to grab the packages and transfer them. The other thing to notice is that carrying 4 packages from one spot and transferring them to a conveyor that is half a meter away, non-stop, during an 8 hours shift... that can be quite exhausting and boring. What I propose is that instead of that, take this employee and give him another task that involves more skills.
When talking about large parts you can also think about large cardboard box sizes that might have to be handle in a packaging application. These objects are relatively light (so they respect the robot payload) but since they are large they are tougher to handle for a human worker. If the application requires several large parts, the robot can handle them one at a time instead of asking the worker to pick them up one by one.
Does the Job Require Personal Protection Devices?
Applications that involve high temperatures, sharp blades, high impact potential or high noise levels are all jobs that are perfect for robots. Since workers have to wear or use personal protection devices, it means that the application is probably high risk and that a robot can be a good way to remove any kind of potential danger. Watch the following video and notice the different applications done by Baxter that are potentially dangerous for a human worker.
Can the Job be Done With Your Eyes Closed?
You can detect a job that can be automated by asking yourself, can I do this job with my eyes closed? or can this job be adapted to do it blind? With physical guides, and poka-yoke devices a job can easily be automated. The following video shows a very simple packaging task that can be done with your eyes closed. The parts are being fed by a conveyor and always come to the exact same place, the robot only has to put them in the cardboard box and you are all set. No need to require judgment or dexterity... this is the perfect job for a collaborative robot.
Low Precision Required
Using a collaborative robot such as Baxter means that your process doesn’t require a particular precision. You only want the job to be done correctly. For example transferring a package on a conveyor doesn’t need any kind of precision, the package has to be on the conveyor and that’s it. So even if the precision is rough, the application can still be done. Keep in mind that humans don't have any kind of precision either.
Don't Think That a Robot is Dedicated to a Given Task!
Back in the day, a robot was dedicated to a given task. With all the guarding, fixations, and external devices used in the robotic cell, it was a complex process to move the robot to another station. Now that collaborative robots can be programmed by hand-guiding and have mobile platforms, it is easier to move them from one station to another. In a few minutes you can reprogram them and you are good to go.
New Version of Baxter: Sawyer
Rethink Robotics has come out with a new version of Baxter, called Sawyer. It is basically the same platform, but with a single arm and with enhanced features. Sawyer has a bigger payload, higher repeatability and higher stability. It can perform applications that require greater accuracy than Baxter provides. If you want to learn more about this robot, follow this link.
If you have a production process that meets any of the criteria above you should consider looking into whether a collaborative robot might be just the thing to improve your production process at the same time alleviating potential human injury and making your factory jobs more attractive for your employees. To review the specs for collaborative robots on the market today check out the link below.
Leave a comment