The Biggest Challenge for CNC Machine Tending with a Robot: Solved!
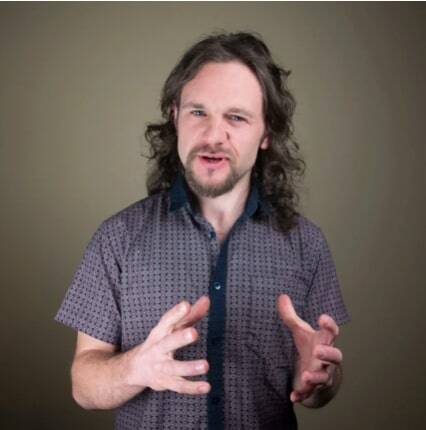
Posted on Sep 06, 2022 in Automation
5 min read time
Every machinist knows that machine tending can be a time-consuming and tedious task. Your CNC machines require almost constant supervision which keeps you from doing more valuable tasks.
A robotic machine tending solution can help to improve the productivity of your CNC machines in an efficient and accurate way. Robots can also improve the safety of your operation, reducing the need for operators to be in close proximity to the machines.
The problem is that integrating a robot for machine tending is traditionally complex. Unless you are an experienced roboticist, some specific integration challenges can hold you back and slow down the deployment process.
We find that one particular challenge slows down machine tending deployments more than everything else. And our team at Robotiq has found an ingenious solution to that challenge.
What is robot CNC machine tending?
Computer numerical control (CNC) machines are used across industries to create everything from engine parts to cellphone cases. In order to operate them, machinists need to feed the machine with new workpieces. This can be a time-consuming and dull process.
Robot machine tending involves using a robotic arm to load and unload material from the CNC machine. It can result in a significant increase in productivity, as you don't need to return to the machine after every work cycle. Instead, you can queue up a whole batch of workpieces and the robot will process them all with no human intervention.
As robotic technology has become easier to use over the last decade, machine tending has become one of the top tasks for collaborative robots.
The biggest challenge for robot machine tending
Even though machine tending is a popular robot application, it can also be quite complex to deploy.
One of the biggest challenges is communication.
There are many different CNC machine types and manufacturers. Each model has a different method of communication. Traditionally, your robot controller needed use these communication protocols to interface with the machine.
For example, a common communication protocol used with CNC machines is RS-232. Other protocols include Ethernet, USB, and even wireless.
The difficultly comes when you need to program your robot to interface with the machine. You needed to "get your hands dirty" and set up the communication protocol in your robot controller. You had to find out how your specific CNC machine used that communication protocol and adjust your programming accordingly.
This is not a very complex task if you are experienced in programming. But it can be restrictive if you are not a programmer.
An ingenious solution to the communication challenge
At Robotiq, we always try to make robot deployment as easy as possible for our users.
When we developed our Machine Tending Solution we knew that communication protocols were going to be the most challenging part of the process.
How could we develop a solution that worked with almost every CNC machine?
A solution that didn't rely on the user knowing how to program communication protocols?
One that people could use out-of-the-box without extra help?
Our team came up with an ingenious solution to the problem…
They removed the need for a communication protocol completely.
How?
The Robotiq Machine Tending Solution interfaces with your CNC machine in exactly the same way that your human operators do.
Here's how:
-
To start and stop the machine, the system uses an actuator to press the "Start" button on the machine's control panel.
-
To detect when the CNC machine has finished a cycle, the system uses light sensors to detect the machine's status lights.
-
To open and close the door to the machine, the system uses an actuator to press the operator's foot pedal.
These simple but powerful solutions allow you to add the Machine Tending Solution to almost any CNC machine without complex programming.
3 other challenges when tending a CNC machine
Communication is not the only potential challenge that can affect your robot machine tending. Other challenges can affect your deployment, depending on the specific requirements of your application.
Here are 3 more common challenges and how you can overcome them:
1. Travel time between the table and machine
Every second that your CNC machine is not running is lost productivity. This means that you are losing productivity when your robot moves to pick up the next workpiece.
A brilliant solution to this is to use a dual gripper. This allows the robot to pick up the finished workpiece and place the next one in the machine with one movement of the robotic arm.
2. Robot programming
Modern collaborative robots are easier to program than any industrial robot in the past. However, the requirement for programming can be difficult for machinists who often don't have any experience with robots.
Robot application kits are a good way to overcome this challenge. They include everything you need to program the robot using simple configuration wizards.
3. Difficult grasp points
Some workpieces are difficult to pick up with a robot as there are no obvious grasp points for the gripper. This can make it hard for the robot to keep a hold on a part and move it into the CNC machine.
Vacuum grippers solve this problem. They can pick parts up from all directions and are easy to integrate into the robot.
How you can benefit from this solution
With robotic machine tending, you can help to reduce the tedious nature of CNC machining, helping you to achieve more productivity with your machining operations.
If you are looking for a machine tending solution that works with almost any CNC machine, without requiring complex communication programming, the Robotiq Machine Tending Solution is probably the simplest, most accessible solution on the market.
What challenges have held you back so far from trying robot machine tending? Tell us in the comments below or join the discussion on LinkedIn, Twitter, Facebook, or the DoF professional robotics community.
Leave a comment