Robotiq Force Torque Sensor Made Especially for Universal Robots
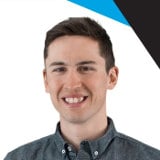
Posted on Feb 09, 2016 in Robot Sensors
3 min read time
As we had a lot of demand for our Force Torque Sensor (FT150) to fit on Universal Robots, we thought it was the time to develop a sensor specifically oriented to the UR design. We wanted to get a perfect mechanical fit, but also to ease integration in terms of connections and software. Learn more about how the FT300 fits the bill.
Smaller Look, Greater Forces?
The most impressive improvement over the last version of the sensor is pretty much its smaller outer casing. The more compact design also has a greater force capability. In fact, the FT300 is now perfectly suited for Universal Robots in terms of dimension, but also it can measure/feel forces and torques normally found in the robot’s environment.
As you can see in the picture above, when fitted with a Robotiq 2-Finger Gripper, it looks almost as if there is no sensor even present. The advantages of this kind of mechanical design are directly related to the safety features of the assembly. In fact, by removing the external connector, reducing the external footprint and matching the sensor shape to the robot wrist shape, this makes the robot more easily used in collaborative applications.
Easy Connection
Most FT sensors on the market today need to be used with an external controller or other analytical devices. The FT300 sensor is made to be integrated as easily as possible. In fact, with a direct connection into the UR controller, a simple cable is all that is required to make the connection between the sensor and the controller; and to give you readable data.
The fact that the data is directly treated inside the sensor and that the wire only transmits communication data (instead of voltage for force gauges) makes the sensor immune to external noise. This particularity was developed for welding applications, but was also included in this latest generation of sensor.
Software Package
Since the Sensor was designed to be matched with a UR, we have also created some routines so that you can simply copy/paste them into your robot program. As you probably know, force sensing is not all that easy to integrate in real life, but with these few programming lines, you can make your life a whole lot easier. See our support section to download what you need to integrate and program your FT Sensor correctly.
Why the FT300?
- Easy to integrate: No machining; no cable or wiring adjustment problems; no looking at robot technical sheets; we have done all the work already to make this sensor as easy as possible to add to your UR robot, why do the job twice, eh?
- Immune to external noise: If you are working around a lot of machines, a lot of electrical noise can be generated, by using this sensor all that external noise won't affect the FT300 sensibility and accuracy.
- Easy to interpret data: The data is treated in the sensor and does not need to be treated a second time, so you don't need further programming or external boxes, it is all inclusive.
- Easily fits with Robotiq’s end effectors: Mechanical coupling, same footprint, devices that can communicate in parallel, I mean it has been designed to be fit together, why not using this to leverage your robotic cell.
At the end of the day when integrating a collaborative robot in your workshop, you want to get back into production as fast as possible and spend the least possible amount of resources to achieve the highest level robotic application. By using easy to install and program devices like Universal Robots with Robotiq products, you are leveraging your integration and making everything a lot easier. You could get the same result from a funky, expensive robot solution... but why would you, when you can do this with a lot less work. It's your call!!
Leave a comment