How to do Product Testing using a Robotiq Gripper
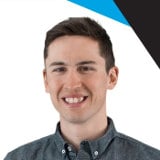
Posted on Oct 07, 2015 in Robot Grippers
4 min read time
When you are manufacturing a product, you have two main concerns; deliver a quality product and have the lowest production cost possible (to make a bigger margin). If we set aside the profit margin reasons, to deliver a product with a superior quality you have to make sure that the specifications for the product are respected and that the product is capable of doing what it was designed to. Bottom line, you need to test your product. As most automated product testing cells are really rigid, this doesn't allow you much leverage if your product changes or if you want to test another product with the same equipment. This is why a lot of companies are switching to robotic product testing.
Since large companies produce product with a relatively long lifetime and with a huge production rate, a flexible robotic product testing cell can be unnecessary for them. But smaller businesses (SME's), who are facing high-mix/low-volume production rates, need flexibility in their production and in the way they test product. As you don't want to get into complex rigid modules you can start with a flexible solution like a collaborative robot paired with an Adaptive Gripper. This will allow you to have a testing cell that can perform a lot of different applications without any complicated safety devices. This is space saving too and it does not require advanced programming skills, while the testing module/machine requires little to no modification.
Here's a great example of electronic product testing. The cell is using the same test module that was used initially. Very few modifications were made to the workstation and the robot was installed in a few minutes. Notice how the Gripper can adapt itself to different kinds of grips without any modifications.
What's required?
Well in this situation, the cell is composed of:
- Universal Robots (UR5): Programmable by hand guiding, 5 kg payload, does not require fencing, can work alongside humans, can be relocated to another task in a few minutes.
- 2-Finger 85 Adaptive Gripper: Highly adaptable to different situations, 5 kg payload, parallel and encompassing grips. Also available with a 140 mm stroke for larger objects.
- Pedestal: Custom robot support to free space on the table and allow the smallest footprint on the work floor, can make the robot mobile for repositioning to other stations (we didn't in this application).
- Test Module: The test module that was previously used by human workers was left as-is for the robot application. The fact that the Gripper can adapt to the handle and to the part at the same time made the redesign of the module unnecessary.
COST
- Universal Robots (UR5): Roughly $35,000 USD depending on a couple of factors ;-)
- 2-Finger 85 Adaptive Gripper: Roughly $5,000 USD
- Pedestal: We used material we already had in stock, but approximately $200 USD. A table would have been good too ($0) or a mobile platform (>$).
- Test Module: As I said the test module was used as-is so $0.
So let's say under $50,000 USD for the whole solution including transportation, installation time and other external factors. If you are interested in calculating costs or ROI, please consult our ROI calculator.
Advantages
- Consistency: You can test your product the exact same way with a highly repeatable robot. There is no human error/factor in the testing (pass or fail). Your products are then consistent.
- Free workers: The worker that used to place the part in the test module all day long is now liberated to do more value added work.
- Fast payback: Because of the relatively low cost and the fact that employees are liberated to do more value added stuff or can simply be available to work on another part of the production, the robot pays for itself in a few months. The average payback is about 6 months with Universal Robots.
- Easy to reposition: The robot can be reprogrammed for another product batch, but it can also be moved to another application, such as packaging or machine tending.
If you are interested in robotic product testing there are many ways to do it. We have only shown one of the ways. Other sensors can be added to make the cell more precise or more repeatable. Vision or force sensors are the usual external devices that are used in these applications. You may also want to get further information on how to integrate a robot into a workshop, to do so take a look at the link below to download more information on this topic.
Leave a comment