Case Study: Whippany Actuation Systems
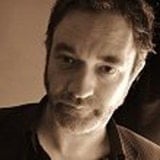
When Whippany Actuation Systems experienced increased demand for specialized parts, they needed to increase productivity. Quickly. The company – a manufacturer of rotary and linear electrochemical actuation systems for the aerospace and defense industries– and its 170 employees faced some important choices: buy a new CNC machine, outsource the work, or introduce automation. Read more to learn what they chose to do.
“We were faced with an overloaded condition at certain work centers,” explains Phil DeMauro, manager of manufacturing engineering at Whippany. “One option would be to outsource some of those products to subcontract manufacturing rather than doing it where we would rather do it, which is in-house.”
With CNC machines costing sever thousands of dollars, Phil DeMauro and Russel Harter, manufacturing engineers at Whippany, took a trip in March 2015 to the Automate trade show in Chicago to explore the automation possibilities. That's when they first encountered Universal Robots.
Eye-catching automation
“We saw a host of manufacturers and Universal Robots caught our eye as an effective solution that could be implemented very easily and programmed very easily. A collaborative system that doesn't require a lot of the traditional guarding or safety fences that other robots require," says DeMauro.
So, DeMauro and Harter, engineers with more than 40 years of combined experience at Whippany, contacted Eric Cortese, a sales engineer and robotics product specialist at Axis Industrial Automation, N.J., the local area distributor for Universal Robots and Robotiq to find out more.
Few Whippany employees understand the tasks that needed to be automated better than Patrick Cain, gear machinist at Whippany. His job is to take blanks that come from other machines and convert them into gears using a CNC machine. He might also need to deburr them or use another machine to do the other side of the gears.
Step-by-step
Whippany needed a robot that was capable of sliding open the door of their CNC machine, reaching in, taking a part out, relocating it safely, picking up another part, putting it in the machine, sliding the door closed, and instructing the CNC machine to begin its work.
If everything went to plan, Whippany hoped to increase production capacity by having the robot work unattended overnight – and all without the major capital expense of a new CNC machine. Perhaps most importantly, Cain and other employees would be freed up to spend time on other, less tedious tasks that added value to the product, like inspection and deburring.
So, after a series of meetings with robot distributor, Eric Cortese, during which potential challenges were analyzed and the potential cost-effectiveness and capabilities of the collaborative robot system became clear; Whippany made their decision; to purchase a Universal Robots integrated with a Robotiq 2-Finger 85 Gripper.
Customized, integrated solution
Initially Whippany wanted to integrate a customized gripper with the Universal Robots, so that it could handle parts of different sizes. Also the robot and Gripper needed to able to communicate with the company's CNC machine. Instead they chose the Robotiq 2-Finger 85 Gripper because they didn’t need to customize the Gripper, they only needed to customize the fingertips.
Choosing an Adaptive Robotiq Gripper for these tasks was a natural choice, says DeMauro. “The Robotiq Gripper is a fully-developed application. Having something like this readily available, off-the-shelf, that can be mounted to a robot and you can easily adapt with custom gripper plates [fingertips] makes it a much quicker implementation.”
Integrating a Robotiq Gripper with a Universal Robots is pretty easy, you can see how it’s done in this video. The Gripper itself is “very, very easy to use”, says gear machinist Cain. “I thought it would be more complicated than it is.” To enable the robot to handle different parts, Cain swaps out customized fingertips, a simple process that takes just a few minutes. “It's a very short procedure,” he says. “Two screws on each finger. Pop them in and out. I don't have to modify the UI programming at all.”
The ability to move the robot from one cell to another quickly and easily was also “a huge consideration”, says DeMauro. “We just pop a couple of locating pins in the floor and get up and running.”
The integration of the robot to the CNC was “straightforward”, says Axis' Cortese. “We had an outside integrator come in and help us to wire the discrete I/O to the controller of the gear-shaper and the Universal Robots. Once we had everything plugged in, we were able to label all the I/O points and map everything out.”
The system's control program allows users to monitor specific I/Os tied to events happening on the machine from doors opening and closing to the unit being loaded. When everything is first turned on, the operator can see an I/O tree lighting up. This indicates that the robot, CNC machine, and Gripper are all communicating with each other.
Benefits
Since then, Whippany's goal of increased production capacity has been achieved, says DeMauro, who expects to achieve ROI on the robot in a little under one year. Collaborative robotics has not just made Whippany more competitive, the company is now considering the possibility of in-sourcing more work because of its enhanced production capacity.
“Overall it helps the business, from a cost standpoint, from a productivity standpoint, and from a capacity standpoint,” explains DeMauro, who expects to see improved company margins as a result.
For gear machinist Cain, automation frees him up to do more interesting work. “The robot helps me out by taking over the tedious stuff, so I can go ahead and do setups. I can also deburr and get the other machine running. It frees up a lot of my time.”
Future plans
Whippany now plans to introduce more collaborative robot systems into their machine shop. “We've already targeted two other cells that we're going to implement robotics in. It's going to give us the ability to aid capacity with a workforce that is tasked with more value-added activities,” says DeMauro.
Increased production capacity, improved employee experience, better margins, increased throughput, an expected less than 12 month ROI --it's amazing what a highly mobile, cost effective, easily installed, robot and Gripper team can achieve.
Leave a comment