What Are the Challenges for Robotic Force Control
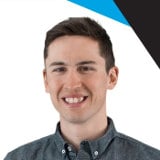
Posted on Dec 04, 2014 in Robot Sensors
5 min read time
With the introduction of a force torque sensor to our product line-up a whole new aspect of robotics has been explored. Monitoring the force and torque applied on the robot tool is useful data for different applications. However, it is not always perfect, there are still some challenges when introducing a FT sensor into your robotic cell. This article is about key points you'll need to look at when shopping for an FT sensor.

External Noise Interference
This type of problem is more about the environment where the sensor is working than the sensor itself. In fact, if the sensor is in an environment where there is a lot of external noise interference, such as welding power sources, high voltage CNC machine, etc. the readings can be just plain weird. To eliminate this type of error different types of sensors are available. Depending on the technology used in the sensor, it is possible to be immune to this external noise. Most of the FT sensors out there use strain gauges to measure force, some other use other technologies that are not effected by external noise. Our FT 150 sensor is using digital technology which is not effected by external noise. Although, there is still a risk of interference if the external sound is causes really strong vibrations.
Robustness
Robustness is separate into 2 aspects. First of all, the maximum force that the FT sensor can handle. So for example, if the sensor can take only 1.5 times its maximum force, you will probably reach this level and destroy the sensor. If your sensor can take 4-5 times its maximum force, this gives you a chance to recover from questionable maneuvers (which of course nobody is doing on purpose, but which does happen...). Also if something goes wrong with the robot and the tool hits something accidentally, you can still save the sensor since it can take a lot of force.
The second aspect is a consequence of the first. If the sensor senses an abnormal effort and permanent deformations occur, some sensors will keep this permanent deformation and will no longer be able to read the right force. However using other reading systems (than force gauges) allows the sensor to be re-calibrated periodically or after an impact and in the case of permanent deformation still be capable of reading the right force. We have been testing this technology and even when applying an outrageous amount of force on the sensor, which caused permanent deformation in the sensor, only a small offset was notice. We re-calibrated or ''zeroed'' the sensor and the offset was gone. Our sensor was still able to precisely read the force applied to it.
Difficult to Integrate Sensor
Software-wise, most of the sensors out there have complex software. Not only are they difficult to understand, they are also difficult to establish accurate readings with. Sometimes, you are obligated to interpret analogical signals and transform them into force and torque data by passing through a conversion matrix that is unique to the sensor or the configuration. This can be relatively complicated. We thought it was easier for end users to have access directly to the data from the sensor. So we have developed built-in algorithms that treat the data and give you what you need - Force and Torque data.
Electrical and connection aspects of a force torque sensor can also be complicated. Often sensors needs external controllers and most of the time, communication converters to be able to communicate properly with the robot feedback loop. Our FT sensor kit for Universal Robots eliminates these steps with fast and easy integration. In fact, with no external controller required, the sensor data is fed directly to the feedback loop without any converter or external controller. This allows you to switch the sensor over from one robot to another, recalibrate and your ready to go, everything is fine. There are no fancy connections or other complicated calibration procedures to perform. It is all built-in.
Resolution
Resolution is the fineness of detail that can be distinguished by the sensor. This means the smallest increment that the sensor is capable of recognizing. If the resolution is small, then the amount of force that can be detect is small and the sensor can more easily detect smaller variations than with a sensor with a larger resolution. This variation equates to the smallest force that can be detected by the sensor and is the value of the resolution. There can be a problem with sensors with large or coarse resolutions that try to read small force amounts. Most sensor manufacturers monitor this specification carefully.
Noise
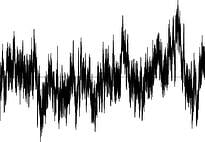
This is pretty much the same as with the resolution, if the force is lower than the force applied to the tool, there is not going to be a way to interpret it. In fact, the signal noise has a certain amplitude and even if a force is capable of being read, the signal of this force has to be higher than the amplitude of the noise signal in order to be interpreted by the algorithm. If not, the sensor will return a null reading. To eliminate this, you should use a sensor which recognizes smaller movements to be able to analyse correctly the forces applied on the tool.
Drift
As with a lot of digital tools, a specific measurement can drift in time. In other words if a given force is exerted on a force torque sensor, the reading can be exact for when the force is applied, although if the same force is applied over a long period of time (several hours for example) the reading might drift in time (most of the time the drift recorded by the force reading will be small).
Bandwidth
The bandwidth is the range of reading frequencies that are considered reliable for a given system. For force torque sensors or general robot applications a low frequency will not be representative of the system and can result in inaccurate readings. In other words, the system will move faster than the reading shown for the sensor and this will slow down the feedback for the sensor with regards to the system. Basically the program will be reading data that is already ancient history and this will screw up the accuracy of the sensor. We consider that a bandwidth of around 100 Hz is considered a good frequency for applications such as hand-guiding, assembly, grinding, etc. However, applications that requires fine precision such as medical surgeries or Haptic applications probably require a higher bandwidth (about 1000 Hz). Our FT 150 sensor works at a bandwidth of 100 Hz for standard applications.
Since FT sensors are relatively new to the market, it can be confusing to shop for this kind of sensor. Hopefully this article has given you a heads-up on what to look for in your next FT sensor. To learn more about Robotiq's very own force torque sensor, follow the link below.
Leave a comment