What are the Important Robot Force Torque Sensor Specifications?
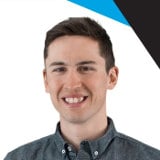
Posted on Nov 09, 2014 in Robot Sensors
4 min read time
I remember buying my first computer, there was a lot of technical data to compare, so I ended up asking the salesperson 'What was the best for me?'. However, at the moment you cannot go to the closest robot store and ask for the best force torque sensor. The following article explains the basics on FT sensor specifications. So you can determine what is the best for you.
Signal Specifications
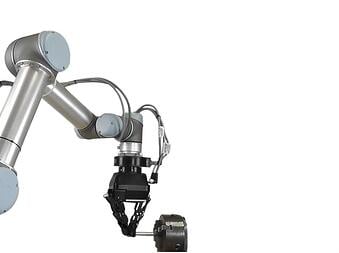
There are basically 2 different types of specifications that you need to understand. First the signal specifications which refer to the electronic side of things. There is also the mechanical specifications which refers to the physical dimensions of the sensor.
Force and torque measuring range
The range of force and torque that the sensor can measure. Most sensor manufacturers will rate their measuring range with a +/- sign. This means, for a +/-150 Newton sensor, it can measure 150 N in each direction. For example, the sensor can measure the lift (pull) of a part, including the part's weight, up to 150 N and it can also measure the applied force (push) up to 150 N in any direction as well. However, this is the measuring range, meaning that you can measure 150 N in every direction. Most of the time sensors can be overloaded. If for example you are using a +/-150 N sensor and the application requires or applies more than 150 N. Take note that if an application needs a given force (ex: 100 N) you should use a sensor that can sense more than the required force (ex: 150 N).
Precision; Resolution
The minimum change in force that the sensor can measure. It is not necessary to have a resolution with five digits of precision, in fact the resolution needs to be graded sufficiently to distinguish between events that are pertinent to the robot application. A sensor will need a higher resolution if the applications need more precision or if the parts are really light and thus require a higher calibration to distinguish. For rough applications and heavy parts, the resolution can be coarser.
Precision; Accuracy
Does the sensor measure precisely the applied force and torque? If the force is 50 N, does it really measure 50 N? It is really important to have good accuracy in the use of a force torque sensor, because some robot control software use dynamic models in which the actual force value is important.
Repeatability
If you apply exactly the same force twice, will you obtain the same value each time? Depending on the application, you may want to have good repeatability, instead of good accuracy, to have a process that is the same again and again. For example, if you are doing deburring, even if you don't apply the exact same amount or force on a part, if all the parts end up the same... your process is still good right?
Drift
The signal is drifting when the sensor is reading a changing force even if no real force is being applied to the sensor. Force measurements are often used in a control loop. A drift in the measurements here will generate false values that will cause unwanted behavior. For example, a sensor drift in hand-guiding will cause the robot to move even if nobody is touching it. So, you want to have the lowest drift possible. And drift can be affected by different environmental aspects like temperature and humidity. By calibrating and recalibrating the sensor often, you reduce your risk of drift.
Noise level
How much noise is generated by the sensor. If the sensor signal is analog, then this noise is added to the force signal. A high level of noise will require signal filtering, reducing the effective bandwidth of the sensor and adding delay to the reaction time of the robot.
Some sensors particularly sensors with a digital signal are immune to external electrical noise. This means that the signal is not effected by external noise and that the signal is clearer so there is no need to apply a filter on the signal. Also it will mean that the sensor is exchanging more accurate information with the robot reducing delays.
Output rate
This is the number of force readings per second that the robot can read from the sensor. Most sensor manufacturers will express this specification in Hertz (Hz). For example 100 Hz, means 100 reading per second or a reading every 0.01 seconds. The output rate needs to be sufficient to feed the control loop in the robot program, so that it remains stable.
Mechanical Specifications
Dimensions
Basically all the external dimensions are important to determine if the sensor will fit your robot. Thickness can also be an interesting specification to consider since it will influence the distance between the robot wrist and the robot tool.
Robot Fit
Sensors are often designed in order to fit well on specific robots. Although you can fit most sensors on different kinds of robots. Manufacturers provide adapter plates that can be attached between the robot wrist and the sensor. Not all manufacturers provide adapter plates for all types of robots. Your vendor or application engineer should be able to determine what is the best fit for your robot, sensor and tool.
Weight
In the end it often comes down to weight. The robot you are using has a certain payload and if you add a sensor, a gripper and some adapter plates, each addition is reducing the functional payload of the robot. Make sure to sum all the components that will be attached onto your robot wrist to make sure it can still perform the application you have in mind. The benefits of adding a sensor might depend on how much latitude you have in your robot payload. But your application might also really benefit from the accuracy, and ease of use functionality gained from a FT Sensor. Ultimately this is for you to decide or if you need help you can do what I did with my first computer, ask someone... like a knowledgeable robot integrator.
Leave a comment