Interview with Matthew Borzage of SynTouch on Robotic Tactile Sensors
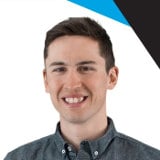
Posted on Jul 08, 2014 in Robot Sensors
7 min read time
One of the big problems common among robot grippers is that usually they cannot feel what they are handling. It can cause problems when grasping fragile parts or when your application needs to apply a minimal pressure on an object. Some companies have come out with ideas that give a sense of touch to the robotic gripper. Companies such as SynTouch have developed some very accurate devices to sense objects. So we asked Matthew Borzage, co-founder of Syntouch, to tell us more about their product.
Robotiq: Can you describe the technology used in the design of your tactile sensors?
Matthew Borzage: The BioTac® is the only sensor technology that endows robots with the ability to replicate the human sense of touch. The technology inside the tactile sensors themselves isn't exotic: they contain flexible circuit boards, pressure sensors, electrodes, thermistors, and injection molded parts. However, the way we've brought these elements together to mimic both the physical properties and sensory capabilities of the human fingertip make the BioTac unique. The BioTac has the ability to detect forces, vibrations, and thermal flux from a sensor that has anatomical features and mechanical properties that are similar to a human fingertip.
When pressed against an object, the BioTac detects forces as deformations of its skin, just like humans. To do this it has a conductive fluid layer between a silicone elastomeric skin and a rigid bone. Pressing on the skin deforms the skin and fluid layers and causes changes to the shape of the conductive fluid layer. These changes in the conductive fluid layer are detected by an array of sensing electrodes on the surface of the core. This information can be used to extract normal force, shear forces, and identify the points of contact.
When slid over an object, the BioTac detects vibrations. To do this it has a pressure sensor inside the rigid bone. Sliding past an object creates vibrations that are transmitted via the incompressible fluid to a pressure sensor. The pressure sensor acts as a hydrophone sensing these vibrations. This information can be used to extract information about object textures and slip conditions.
Finally, when pressed against an object, the BioTac detects thermal flux. To do this it is heated to about body temperature via the electronics within it. Pressing it against an object at a different temperature creates a thermal gradient. Typically objects are at room temperature, which is cooler than the BioTac, so heat is drawn out of the BioTac. The slope of the signal from the thermistor represents this thermal flux.
Robotiq: If we compare your tactile sensors with what Takktile or other equivalent companies have done, what differences are there? What are the advantages of your tactile approach?
MB: The goal of tactile sensing is to endow robotic hands with the ability to perform human-like capabilities such as identification and manipulation of objects to perform useful tasks. The existence proof that such dexterity is possible is the human hand. We practice biomimetic design and have learned from the human hand what tactile information is useful.
If dexterous hands needed high-resolution taxel arrays to be useful, humans wouldn't be tool users because the human hand doesn’t have high-resolution taxel arrays. Instead, deformations, vibrations, and thermal gradients are sensed by the human hand. These senses have made human hands incredibly useful and are now available to roboticists via our BioTac. Other sensors such as Takktile, Tekscan, Pressure Profile Systems, etc. provide high resolution taxel arrays. These are incrementally improved versions of the same types of sensors that have been used for decades and have not previously endowed robots with human-like capabilities.
Our biomimetic design goes beyond mimicking the sensory capabilities of fingers. It requires an understanding of the key mechanical features of a human fingertip: the shape of the bone, compliance of the skin, presence of fingerprints, and other seemingly unimportant features of a human fingertip that are all critical for the identification and manipulation of objects. In contrast Takktile, Tekscan, and Pressure Profile Systems sensors are deployed as a broad, flat, and relatively rigid surfaces compared to a soft, curved human fingertip.
It is not a coincidence that features similar to human fingertips appear in both non-human primates and non-primates like raccoons that are known for dexterity. With the BioTac these features now appear in robots.
If robotic and prosthetic hands are going to be used in the same environments for similar tasks as human hands, then they must address ALL pertinent requirements. Useful tactile sensors for such robots combine the right mechanical properties with the right sensing modalities in a package that is robust and field serviceable.
That is the BioTac.
Robotiq: Why are the motions of our fingers and our sense of touch so closely integrated?
MB: David Katz described this phenomenon when he said "The tactual properties of our surroundings do not chatter at us like their colors; they remain mute until we make them speak" and went on to say "eye movements do not create color the way finger movements create touch".
Our CEO, Dr. Gerald Loeb has expanded on this, saying "Unlike other sensing modalities, tactile sensing is predicated on the occurrence of a specific event - the collision between the object to be sensed and the sensors themselves. The sensors can be designed to be sensitive to various mechanical and/or thermal aspects of the collision, but what they sense is necessarily determined by the mechanical dynamics of this interaction."
As previously described, tactile sensing in human hands is the combination of mechanical features and sensory capabilities, which are mimicked in our BioTac sensor. To create useful data with these tactile sensors requires that the human or robotic fingertips are used to explore objects with strategies gained by spending a lifetime colliding hands with objects to create useful percepts. Our complete understanding of the fingertip's mechanical features and sensory capabilities, and the exploration strategies of hands that generate useful percepts have enabled a new field that we call Machine Touch®.
Robotiq: What kind of robotic applications would be interesting to develop with a 3-Finger Adaptive Robot Gripper and your tactile sensor?
MB: There are two main classes of robotic technology and tactile sensing that have great promise for both: autonomous robots and telerobots. In both cases, the robots need to handle mechanically complicated, unpredictable and fragile parts, a fact that makes these seemingly disparate types of robots have very similar needs.
In humans tactile feedback includes hidden but essential reflexes by which the overseeing brain delegates the moment-to-moment control of muscles. These reflexes are critical because waiting for the brain to process the sensory data would create control loops that are too slow. SynTouch has implemented a local reflex for prosthetic hands (a form of telerobot) that has proven to be very useful. In autonomous robots a computer would be the overseer, selecting and modulating these reflexes to accomplish manipulation objectives just like the human brain controls the spinal cord. In telerobotics a human operator would be the overseer who would benefit from being able to set up rapid and automatic reflexes, just as they normally use their own hands.
The more obvious use of tactile sensing is the conscious perception of an object and mapping its similarity to other previously perceived objects. SynTouch has implemented exploratory movements that have allowed autonomous robots to discriminate and identify objects based on their haptic properties. In telerobotics human operators would benefit from similar information. In this case, a tactile display is needed. Microphones and speakers, video cameras and monitors, and now tactile sensors and tactile displays are pairs of recording and display devices that allow operators of telerobots to experience the world remotely. Designing tactile displays requires an understanding of human tactile sensing, the information provided by our BioTac, and the ability to bring these together into a device that will withstand the rigors of daily use.
We are currently developing tactile reflexes, our capability to perform autonomous object identification, and telerobotic tactile display technologies at SynTouch.
Robotiq: What are the next steps in the development of this sensor?
MB: The BioTac is essentially in a final form that mimics the glabrous (hairless) skin of the fingertips. However we have had a number of requests to make sensors suitable for different areas of robots: i.e. their limbs and bodies.
We're developing the NumaTac®, which is a simplified version of the BioTac. It's an air-filled sensor that has the same mission as hairy skin on a human body: it lets us bash into the world around us without hurting it (or ourselves!) too much. The compliant skin dissipates much of the energy of the impact, and the sensory capability allows our reflexes to kick in and stop the motion. This will allow otherwise brittle robots to cause less damage to themselves, and also allows currently clumsy robots to cause less damage to the world around them
Robotiq: What are the other projects or companies you are working with and what is the success of the integration?
MB: SynTouch is the most widely integrated tactile sensor: beyond our integration with Robotiq we have developed interface kits for robotic hand manufacturers like: Shadow Robot Company, Kinova, Schunk, Simlab, Barrett Technology, and for full mobile robot manufacturers like: Willow Garage and Rainbow Robot, who make the PR2 and HUBO robots, and for prosthetic hand companies like, Motion Control and OttoBock.
We're also working with a number of cosmetic, personal care, personal electronics, and general consumer goods companies. These companies aren’t interested in robotic applications; instead they have been using our sensors as a way to gather useful information about how their products feel to customers. These companies have recognized that the BioTac lets them determine how their products feel when touched by human fingers, which is an important part of the consumer perception of their product.
The applications have enormous breadth, but in a short summary they're being used to do everything you expect your own fingers to do: they enable dexterity, prevent damage, provide awareness, protect humans, and improve product quality.
Leave a comment