Challenges of Dexterous End Effectors
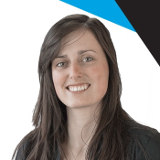
Posted on Jul 25, 2013 in Robot Grippers
4 min read time
During the Automate 2013 show, a workshop was held by the National Institute of Standard and Technology (NIST) and Robotiq was represented by Jean-Philippe Jobin, one of its co-founders. A lot of interesting subjects were discussed about dexterous manipulation. In our previous article on this workshop, we talked about the Dexterous Manipulation Needs within the Industry. Along these same lines, is the idea that the main component that can give dexterity to a robot is the end effector. There exists a lot of different grippers on the market, but what really are the challenges for the dexterous end effector?
Material handling
First, material handling can be a very complex task and is one of the main challenges for industry. Clay Flannigan from Southwest Research Institute (SwRI) explained how we can class difficulties in material handling. He gave four examples: structured, semi-structured, bin picking and unstructured material handling.
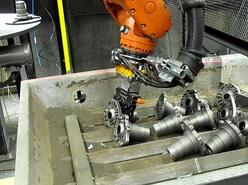
Structured Material Handling
In this type of manipulation, the rigid part that needs to be gripped has a predetermined location and orientation easily reachable by a robot and its end effector.
Semi-structured Material Handling
Here the part is constrained on a planar surface with no assigned location or orientation. It is defined as a 2 degrees-of-freedom (DOF) pose. There is no overlapping of parts. This kind of handling is easily done with the help of a vision system under controlled lighting.
Bin picking
Bin picking consists of a single type of object randomly piled in a box. The system needs to resolve the pose of each object with 6 DOF. A lot of overlapping parts may be encountered. Here again, actual vision technologies have proven that they can solve this kind of puzzle, but controlled lightning is still needed.
Unstructured Material Handling
The last example is the more complicated. Different types of objects are overlapping and are randomly oriented. The parts may or may not be rigid and the system needs to resolve a 6 DOF pose of overlapping parts. Since lighting might not be controlled, vision systems are very hard to implement. This kind of material handling can not be automated with all the present technologies. Humans are still the right solution for this type of handling.
Describing these different difficulties in material handling shows the great challenges that have to be overcome. Many of these applications have been improved by the use of vision. However, these technologies are still in development and are expensive. In order to facilitate any kind of material handling, Jean-Philippe Jobin, explained that the right gripping device could simplify the vision requirements and tooling costs.
The Right End Effector
Small manufacturers production is often characterized by a low volume and a high mix of parts. Also, they usually don’t have a lot of capital for tooling and they have high labor costs since humans are their solution for complex material handling. These are the reason why manufacturers need dexterity to lower the tooling and labor costs and reduce cycle time that are characterized by a lot of changeovers. This dexterity is often given by the right end effector.
The selection of the gripping device is often done at the end of a system design. Instead, it should be considered at the beginning of the project, since tooling such as vision systems may not be required when considering the gripper first. In order to select the right end effector, different aspects should be considered such as:
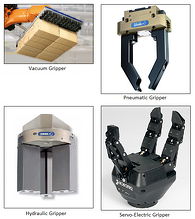
-
Stroke
-
Grip force
-
Speed
-
Form factor
-
Weight
-
Material
-
Repeatability
-
Sensing
According to Robotiq, the right end effector for dexterous manipulation is in the ‘sweet spot’ in terms of performance, flexibility and cost. Robotiq Adaptive Gripper are designed to provide the best gripping solution for your applications.
The Robotiq fingers can adapt to any form of object without sensing or vision devices. This adaptability comes from their mechanical design. In this way, robot grippers from Robotiq provide high flexibility and a great ROI.
Leave a comment