Dexterous Manipulation Needs within Industry
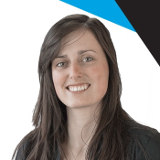
Posted on Jul 16, 2013 in Manufacturing
4 min read time
This past January, Robotiq was at the Automate 2013 show. We were featured in our partner's booth and we also took part in a workshop on Dexterous Manipulation for Manufacturing Applications. CTO, Jean-Philippe Jobin, one of the co-founders of Robotiq, was there to discuss the challenges of dexterous hands in the industry. The main goal of the workshop was to define the application of dexterous robot technologies in order to meet industry requirements. The National Institute of Standard Technology (NIST) just recently released their final report on this workshop. A lot of issues were discussed and a lot of interesting information was shared during this event. We would like to share this information with you through a series of interesting articles. Here, we start with the needs for dexterous manipulation within industry.
Challenges
Manufacturers are facing new challenges when their production involves high-mix, low-volume parts. When it comes to automation, this new type of production needs fast changeover and reprogramming in order to stay efficient. The panel agreed that the next automation challenge is to satisfy this kind of production. This is where the need for dexterous manipulators are greatest. Dexterous manipulation is defined as “an area of robotics in which multiple manipulators, or fingers, cooperate to grasp and manipulate objects”.
From the manufacturers perspective, the main challenge is to be able to grasp as many objects as possible of different sizes and shapes, adeptly and decisively. These systems need to have a certain sense of touch in order to reproduce human dexterity and be able to grasp any object in a “blind to shape” way. Some panelist think that, one day, reactive grasping will allow 'blind grasping' of an object without the use of vision.
There are two ways to give dexterity to a system; either through the end effector or through the robot itself. Some companies, such as KUKA, have already developed a dexterous robot arm with sensors in every joint. This solution might be more expensive, but it still enables the feasibility of dexterous manipulation.
Industry Needs
Procter & Gamble
At the workshop, the first to speak was Mark Lewandowski from P&G. This company is a great example of high mix production with over 2,000 different products. As an example of the need for dexterous manipulation, he talked about their production line for bottles, where they need to be placed on a conveyor belt. The various shapes and sizes of these bottles makes automation using today's technologies infeasible. P&G are looking for flexible automation in order to reproduce human capabilities. Grasping has to be adjusted by force and sensing feedback to avoid crushing the bottles. Moreover, the grasp has to be firm enough to avoid slippage during high speed movements. Mr. Lewandowski stated that the robotic end effector has to be 99% reliable, so it is not the weakest link in the production chain. He also mentioned that the cost of universal gripping devices is easily justified by their flexibility and reliability, compared to the high cost of custom end effectors, which are designed for individual parts.
Boeing
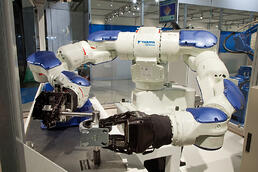
A Boeing representative was also part of the panel discussion. He was there to explain the assembly and automation processes in his industry. Craig Battles exposed the assembly challenges facing aerospace by showing examples of complex parts used in this industry. Boeing's biggest issues for robotic dexterity in manufacturing and automation are: safety, quality control, cost reduction and throughput. Each assembly tasks has different quality control and cost challenges and each one includes a fastening, a loading/unloading and a sealing step.
Human safety is a big consideration, because there are a lot of risks involved in repetitive tasks requiring tools, along with the hazards of an automated environment. Some tasks are even performed in tight spaces where a human can barely fit. Thus, small collaborative robots might be a great solution for those kinds of tasks, especially since they can reduce safety hazards. But this brings another challenge, since those assembly robots would need to move around the large shop floor.
At the scale of aircraft manufacturing, a “dexterous hand” would be more like a series of coordinated manufacturing robots each acting as a finger.
Conclusion
In conclusion, the need for dexterous manipulation is definitely present within industry. Some examples were presented by different companies. As the technology is evolving, manufacturing processes become more and more erratic. This workshop was, thus, very useful, because it was meant to find a way to bring new technologies to the manufacturing floor. This is also Robotiq's main goal with its adaptive end effector solutions.
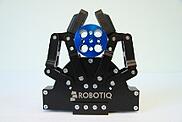
Leave a comment