5 Reasons Why Industrial Robots are Stagnating
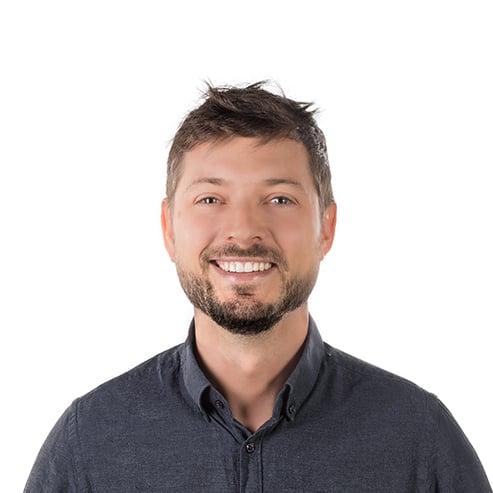
More than 50 years ago, the first robot was introduced in manufacturing, the first man landed on the Moon, the laser was invented and the personal computer would appear 10 years later. Don't you have a feeling some fields have advanced much faster than others? From my point of view, it seems industrial robots have been stagnating for a while. Here's my (humble) opinion on why.
See this technology comparison from 1985 to today, taken from Chris Anderson's talk at the 2011 AWAS Conference.
1. The Reality of Industrial Robotics
I can blame the industrial robotics industry for being conservative and, I have to admit, this game is a tough one. When you are responsible for installing and supporting the equipment upon which the production of entire plants run 24/7, you want to make sure that what you are using is proven and safe. Traditionally, the integrators that work with plants are comfortable with a toolbox, or range, of products. Experienced integrators know too well the pitfalls of trying to shorten steps when they expand the toolbox too quickly. That being said, other industries face higher stakes than industrial robotics while being highly innovative. Medical equipment is one example where it is not about production and money, it is about saving human lives - the innovation and speed in this field is amazing.
2. Lack of Collaboration Means Waste
Industrial robots are sold in a market that is obsessed by reducing waste and being more efficient (ROI is always brought up). It seems controversial then that the lack of collaboration between players in robotics, due to competition or other factors, is creating wasted time and dollars for customers. An important aspect of the robot manufacturer's business model is about locking you into their operating system and controller. Here are examples of facts that create waste:
- Each robot company has its own proprietary programming language.
- Programs can't be ported from one robot company to the next.
- Communication protocols are all over the place (see our article about communication protocols used in robotics).
- Mechanical interfaces are not standardized across the industry.
- Each and every one of them support only a set of peripherals such as vision systems or force sensors.
As a result, most robotic peripheral makers (such as Robotiq) have to support many different protocols and even having to modify the robot controller programs. This requires a lot of developement time that someone ultimately must pay for and which also doesn't add functionnality to the product.
The above is just one example. Imagine a plug and play industrial robotics world a-la-USB. That would be fantastic! It would save money across the value chain, especially for end users. It is true that if robot manufacturers opened their platforms, it might reduce the revenues/robot sold, but this would have a dramatic impact on the overall acceptance of robots, increasing the total number of sales. This would also force manufacturers to compete on features, quality, service and more rather than "well, you already have some of our robots; it would be complicated to used another brand."
3. Recent Years Were Bad, Current Times Are Too Good
Industrial robotics is still highly dependent on the automotive industry, which accounted for 36% of the number of units sold in 2009 according to World Robotics. When your largest customers are closing plants, they certainly are not buying your equipment which is intended to increase production. A lot of employees working in robotics lost their jobs during the turmoil. Now, the automotive sector is rebounding and is playing catch-up with the investments they were supposed to make over the past 2 years. In turn, industrial robot manufacturers are experiencing high growth at the moment. This is happening at a time where staff is still low which means industrial robot manufacturers are quite busy trying to ship the units they've sold. This leaves few available resources to work on new solution development in some cases.
4. Lacking Young Minds
If you attend industrial robotic shows, look at the age of the people working for industrial robot manufacturers. I don't have data on this, but according to the average hair color, I can tell that this industry is aging. Believe me I have huge respect for experience, but youth brings state-of-the-art skills taught at schools, energy, creativity and a risk taking attitude that are an absolute necessity to innovate. As I wrote in a recent article comparing industrial and service robotics, the cool factor is definitely in favor of the latter, that hires the most talented young roboticists and mechatronics graduates. This is one decisive reason why you are seing high innovation nowadays in service robotics. Perhaps more companies will find ways to mix experienced minds with new minds to leverage the best of both talents.
5. End-Users Don't have their Back Against the Wall, Yet...
Aging population is a ground swell that will take a big chunck of the skilled workforce out of the active population in the next 10-15 years. This is a fact that will hit all industrialized countries. See for instance statistics for the USA and Canada. To keep increasing productivity, or even just keep production running, robotics will not be an option; it will be a necessity. Companies are already struggling to find skilled welders and machinists, and it's getting worst every year as baby boomers exit the work force. This will continue to put pressure on robot manufacturers to offer more affordable, flexible and simple platforms.
Exciting times are ahead. This may be a controversial article to some but, the "reasons" are a collection of observations over my recent time in the industry - I welcome your feedback.
Leave a comment