How To Choose The Right Robotic Gripper For Your Application
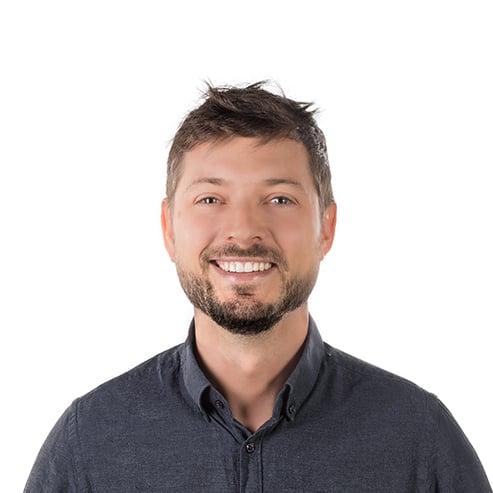
Posted on May 25, 2014 in Robot Grippers
3 min read time
Grippers consisting of vacuum cups, pliers, or finger assembly are some of the most common EOATs (End Of Arm Tooling) to be used on industrial robots. To ensure economical and practical success in automation projects, choosing the right gripper is essential. After all, this is where the rubber hits the road. This article focuses on technical factors, from a process and part perspective, that must be taken into account when choosing the right gripper for your application.
What will be done with your robot? Automation projects vary greatly from one to another.
- The task itself : The tasks to be done by a robot often determine the type of gripper that should be used. A very fast loading/unloading requirement will favor vacuum cups but a slower process will favor pliers or fingers for accuracy.
- Cycle time: The speed needed for clamping and/or opening or closing the gripper will determine cycle time. The cycle time will also determine acceleration and resulting G force from the gripper, a heavier gripper will put more G stress on the robot and cause wear on its parts. You must remember that robot specifications for maximum acceleration are calculated by the sum of the gripper weight and the part, so more gripper weight means less weight from the part you handle. In addition to this specification, reach and EOAT weight will determine the resulting torque at the robot base; again we will seek to minimize the gripper weight. This is why many modern grippers favor the use of hollowed aluminum parts.
- Precision need: Some assembly work will require great precision, a mechanical gripper, actived by servo-electrical motors, would be ideal. Part sorting processes will require gripper adaptability to ensure parts can be sorted, especially those ranging in size or that are positioned differently from each other.
- Environmental need: Not all gripper types can be used in every process. In the food and pharmaceutical industries for example, hydraulic actived grippers are forbidden since there is a risk of oil spilling and contamination. In many clean room industries vacuum and pneumatic grippers are also not recommended since they can create flow of particles in the air. Grippers used in less clean environments like foundries, machining and welding are exposed to dirt and particles so they must be protected. Corrosive or toxic environments in nuclear or chemical industries also create special considerations for protecting the gripper to ensure its stability and safety of use. In most applications the gripper must be failsafe. Dropping a banana on the floor has no serious effect but spilling chemicals or radioactive materials can be catastrophic and/or toxic in some cases.
The parts:
Knowledge of the part to be manipulated is crucial in determining which gripper should be used. The main factors are:
- Size: Except for vacuum grippers, all other grippers need to grip parts with a parallel or angular closing. This means the bigger the part, the more reach gripper fingers will require. In all cases, the gripper must have enough reach to handle parts but not in excess since longer fingers create more torque on the tool and the robot.
- Shape: The shape of an object will determine which kind of grasp can be done. Flat surfaces can be handled by vacuum or magnet types of grippers while other shapes will be handled by jaw, claws or multiple fingers. When using encompassing or fingertip grasps, calculating finger reach must be taken into account.
- Weight: To ensure grasping holds, a gripper must have enough force to meet the weight of the part and time the acceleration it can withstand during the process. A designer cannot simply use maximum clamping force since damage to the part or the gripper may occur.
- Surface type: The type of surface upon which a grasp will occur will also be an important factor when estimating friction.
Calculation of the clamping force must account for a part's weight, maximum acceleration during the process, surface friction and maximum stress the part and gripper can withstand.
Economic factors:
In an upcoming piece, I will expose some of the economic arguments for automation projects in various industries.
Conclusion:
This article summarizes that the more adaptability and flexibility provided by a gripper, the better. Adjustment of the clamping position, angle, rotation possibilities and grasping methods will protect your investment from future retooling costs.
Leave a comment