How we Tested the Robotiq Adaptive Gripper
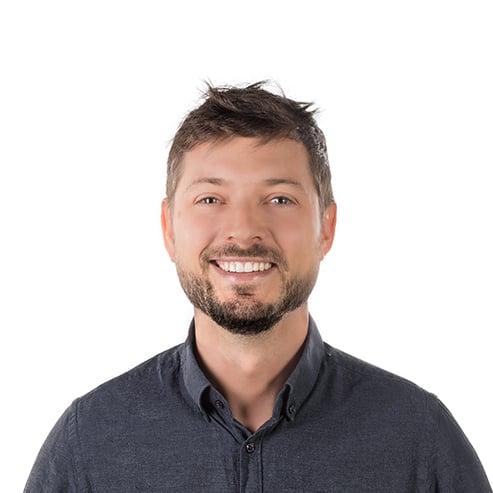
Posted on Apr 28, 2011 in Robot Grippers
2 min read time
You might look at the Adaptive Gripper and say, "Nice! But is it rugged enough for what we do here?" Robotiq has put great effort to ensure that when we pack a gripper in a box and ship it to a customer, it does the intended job precisely and consistently. Enclosed in the gripper casing are electronics components and motors of the highest quality. The gripper is additionally built on a mature finger design based on more than 10 years of R&D for nuclear and space applications. Even so, before the product was launched, we completed extensive testing of the gripper and its components. Below is an overview on how we've tested for production-ready Grippers.
Gripper Cycle Testing
Four Grippers were tested in this case. The video above shows the test bench utilized for the Adaptive Gripper. It consists of four stations. In each station, one gripper is subject to a specific loading condition. The four different Gripper grasping modes are tested. Each unit did a total of 100,000 cycles, 1/4 of the cycles being on the four different stations. Two of the grippers were holding 100% payload specs. The two others were holding 50% of payload specs. No preventive maintenance was done, or required, during the testing period. Result: not a single flaw and no performance degradation. One of the four units is still running, without charge, until it reaches a milllion cycles.(*2011-10-19: The gripper has now reached 3.6M cycles and is still going on.) This test bench is used for quality assurance to test grippers before they are shipped to customers.
Gripper Environmental Testing
We requested the expertise and equipement of INO for the Gripper environmental tests and did them according to the Department of Defense Test Method Standard for Environmental Engineering Considerations and Laboratory Tests (MIL-STD-810G standard 501.5 and 502.5). We conducted both Storage/Transit Environmental Tests and Operating Environmental Tests.
Results were:
- Min. storage/transit temperature: -30°C
- Max. Storage/transit temperature: 63°C
- Min. operating temperature: -10°C
- Max. operating temperature: 50°C
Gripper Destructive Testing
The two images above show the gripper in a welding environment. These tests confirmed that the electronics and communication could withstand welding requirements. It also demonstrated which mechanical aspects need to be protected for using the gripper in welding applications. Stay tuned for the solution that we are preparing.
We've also tested the load that fingers could bear individually. As shown in the above picture, we loaded a finger with increasing weight in the three main directions. In all directions, the individual finger could withstand a hanging weight of 85 pounds or more before breaking.
Are you ready to put the gripper to the test for your application?
Leave a comment