The New ISO/TS 15066 is Now Out, What’s Next?
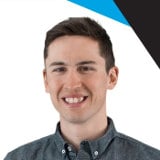
Posted on Feb 05, 2016 in News
4 min read time
Yes, it is finally here, ISO/TS 15066. We have been waiting for this standard for a long time. I am sure everyone involved from near to far in the collaborative robot design world has been waiting for it. In fact, this will guide collaborative robot design and the environment around cobots to ensure that human and robots can work in perfect cohabitation without undue risk of harm. Here's what’s in ISO/TS 15066.
What the hell is ISO/TS 15066 anyway?
To make a long story short, the new technical specification is a complementary document to support the previous ISO 10218 (Safety Requirements for Industrial Robots) which was really focused on industrial robots and barely on the (relatively new) collaborative robots. This standard will then give more explanation on specific human-robot collaboration and the different requirements necessary to make sure your robotic cell or your robot, if you are a robot manufacturer, is as safe as possible.
- ISO/TS 15066:2016 is a good first step toward ensuring the safety of human workers in a collaborative robotic system and will be a solid foundation for future work in this area.
- TS 15066 is a Technical Specification (TS), a document that provides supplemental and supporting information to the industrial robot safety standard ISO 10218-1 and ISO 10218-2, published in 2011.
- ISO/TS 15066 provides safety requirements for collaborative industrial robot systems.
- Effective use of TS 15066 assumes that the system under consideration is in compliance with ISO 10218:2011.
What does this new TS add to ISO 10218
The biggest addition to ISO 10218 is the 'injury level' data (calculated for the maximum robot speed for specific body parts), a deeper explanation of the different collaboration modes and what to put in your collaborative robot risk assessment.
Injury Level
According to the Technical Specifications, the ISO committee is using a grid representing the different 'pain' levels for each body parts developed by the University of Mainz, Germany. This means that for each body part exposed to a robot, you now have an exhaustive list of force and pressure levels that will guide either your robot design or integration. In fact, since this data is expressed in force and pressure, there are different ways to analyze it to prevent overshooting this threshold in the case of impact.
One of the ways to reduce impact is by designing robots and robot tools that are compliant and or soft; and which will reduce the force of the impact by their greater contact surface or by slowing deceleration during an impact.
Another way to avoid reaching high body part pain levels is to adjust the robot speed (this can be adjusted during the programming process). In fact, by reducing robot speeds, you then get a smaller inertia, which means a smaller amount of force in the case of an impact. Which brings us to the next part of the tech spec: Allowable speed.
Robot Maximum Allowable Power/Speed
The ISO/TS regulation details all the necessary calculations you will need to determine the maximum allowable speed to set your robot at to avoid reaching human pain levels that are deemed too high. The interesting part of these calculations is that they can be very specific to each situation and they can also be specific to a given part of the human body. Without going into too much detail on the calculations, the energy transferred to the body by the robot must consider the specific body part as each body part has an effective spring effect. The calculations involve a whole lot of different variables, but you should know that without all the body part information, it was kind of hard to estimate the energy level (or maximum speed) to set a robot at so that it does not harm humans. By having all this different data, we are able to start our analysis of potential injury with a proposed formula. It should be noted that even the committee studying this states that no doubt the data being presented in this tech spec is likely to change as more information becomes available, this being the first set of regulations along these lines.
Robotic Collaboration Mode
When looking at ISO 10218, you can read about what are the different collaboration modes, however, besides describing it, there are no details on the different requirements necessary to achieve these collaborative modes. Considering the fact that a collaboration mode can be achieved using non-force-limited robots (industrial robot) it is really important to have information on how to do it properly and to make sure it is safe for human.
How to Fulfill your Risk Assessment
Once again in addition to ISO 10218, the ISO/TS 15066 is more specific on risk assessment fulfillment. In fact, when considering that collaborative robots are a different kind of robot, you need to know what has to be put in your risk assessment and this tech spec gives you more information along these lines.
Design Criteria
A small but oh so important part of the standard speak directly to robot and robot tool manufacturers on the different design criteria that should be introduced into their design. This will give clear guidelines to manufacturers that were expanding exponentially, but that couldn't draw a line between what was and what wasn't collaborative.
Who should use this TS? Robot suppliers and integrators.
Robot suppliers and integrators. The new Technical Specification on Collaborative Robots (ISO/TS 15066) will provide guidance primarily to suppliers and integrators for the safe design and operation of collaborative robot systems.
Those wishing to purchase this Technical Specification will be able to do so by visiting the ISO Store website. Actually it is available in PDF form now and as of the February 15th will be available in paper form. A short time after ISO/TS 15066 appears on the ISO Store website, it should also appear on the ANSI Webstore as well, where the purchase can be completed in U.S. dollars, and ANSI members can use their member discount.
With this recent release we are expecting a wave of new design and new concepts from different robot companies. We will keep you posted on what's new and what robot manufacturers are doing to try to respect the different requirements of this technical specification. In the meantime, you may want to take a look at our risk assessment eBook to increase your familiarity with safety requirements and how to complete this process.
Leave a comment