Robotiq Adaptive Robot Gripper - New and Enhanced Features
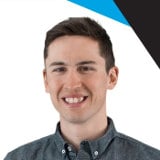
Posted on Aug 19, 2015 in Robot Grippers
4 min read time
At Robotiq we are always seeking integrated solutions for our end users. As our Grippers can adapt to different geometries, we thought it was time for them to adapt not only to the geometry of the part but also to its composition. In fact, a soft or fragile part should not be treated the same way as a hard part, this is why we have added a Low Force Mode setting in our programming. We have also been concerned about object detection when an object comes in contact with the fingers of the Gripper. Ultimately we wanted to secure the grip on the object whatever the situation was, so we developed a Secure Grip Mode. And finally to make programming even easier for end users, we have improved the object detection algorithms in our Gripper.
To have a better comprehension of the new capabilities of our Gripper take a look at the following video.
Object Detection
We have been using object detection for a couple of years now, but these new adjustments have enhanced its capability. In fact, object detection is simply a reading of the position of the Gripper. As the Gripper stops against an object, a certain (fixed) position is reached and read, since this position is constant for a certain amount of time and the requested position is not actually reached, you can assume that an object has been grasped. In other word, if you request the Gripper to close completely (position 230), and it stops at position (145 like in the video) depending on the object size and composition, then you can tell if the part has been grasped or not. In the opposite case, if the Gripper closes completely at 230 (fingers completely closed against each other) there is no way you can send an object detection query to the robot program.
So, this feature basically allows you to detect if a part has been dropped. As a given position is reached (say 145) with the object in between the fingers, if the object is then 'lost' or slips out of the finger’s grip, the Gripper will continue to close and will reach its requested position (say 175) where it stops and sends an object lost signal to the robot program. This way the Gripper can react in order to either regrip another part or simply stop.
Secure Grip Mode
This new feature of the 2-Finger 85 Gripper has been designed to secure uneven objects or objects that tend to slip. In fact, as shown in the video, there are 2 main scenarios that require the use of the Secure Grip Mode. The first one would be the scenario where a soft object such as a cable has to be gripped. Since it is not 'hard' the cable tends to change positions and places itself in ways that are hard for the Gripper to grasp correctly. Using the standard programming method, the Gripper would feel a forced feedback resistance and stop when this is detected. However, in Secure Grip Mode, the Gripper will continue to close its fingers against the object if it doesn't feel a particular requested force threshold. In other words, without this mode, the fingers stop once they detected resistance, but using the Secure Grip Mode, the Gripper will constantly read the force and will adapt its grasp according to the object.
In the case of the cable, you can observe in the video that once the cable starts to slip, the finger position changes to secure the object in place.
In the other case presented in the video, you can observe an object encountering another object in its path. With the Secure Grip Mode the Gripper is making sure that the object stays in between its fingers. In fact, the Gripper is closing its finger a little bit more than its initial grasp to make sure the object is not going to drop. This allows you to achieve your task every time even if the robot hits something. In applications where the environment is unstable or there are a lot of variables, you can be sure that your task will be completed.
Low Force Mode
Imagine that you need to handle a tissue box or eggs. You need to grip the object strongly enough to be able to move it with your Gripper, but you don't want to destroy the whole thing. The problem that most grippers on the market today have is that they will either close to their requested position which sometime leads to not grasping a part or they will close until they reach a given force. With fragile objects the line between reaching the exact force and exploding an egg into messy pieces is really thin. This is why the Low Force Mode has been developed. It is made for soft or fragile objects that need to be kept in their original shape, but still allow them to be handled with a robot Gripper. So basically the Gripper is acting like a human would, if you see a fragile or soft object you do not try to crush it, you simply take it with care and carry it where it has to go.
The goal of all these new features is simply to be able to achieve your task each and every time you are requesting it. Whether you are doing machine tending, bin picking or warehouse automation, you can grasp different types of objects, make sure they are in the Gripper and that they will remain in it whatever else is happening. So whatever your application is, take a look at these new features to see if they can improve your applications.
Leave a comment