Why Are Collaborative Robots So Cheap?
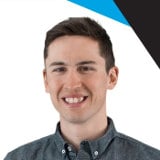
Posted on May 06, 2015 in Collaborative Robots
3 min read time
You may wonder why there is such a strong difference between the collaborative and industrial robot price. Well there are few differences that can reduce a production price and allow robot manufacturers to offer their robots at a lower price point. Here are the main reasons why collaborative robots are cheaper.
So let’s take the example of a UR10 from Universal Robots and an M-10A from Fanuc. The UR10 being the collaborative robot and the Fanuc being the industrial robot. Look at the following comparative chart to see the specification differences.
Hardware
First of all, collaborative robots, for the most part, are designed to have smaller payloads, slower speeds and lower accelerations. This means that the different structural components and motors can be smaller than a standard industrial robot. By having a frame that is lighter, you can put in smaller electrical motors that are cheaper than heavy duty industrial strength robot motors.
Since a large part of the collaborative robot has to be easily movable by hand, they have to be made out of light weight materials. This is a big difference from industrial robots with the same payload. In fact, for the same payload, a collaborative robot will always be lighter than an industrial robot. This means that less material is used to manufacture the robot… which is one reason that results in a cheaper robot.
In this particular example, the Fanuc robot weight is 130 kg and the UR10 weight is 28.9 kg which means the UR is 4.5 times lighter than the Fanuc. This means the UR is a lot easier to move. So smaller actuators and a lower price. For the end users it also means a lower power consumption.
Accuracy
When looking at the different robot specifications, you may have notice that the collaborative robot has a lower accuracy and repeatability than the industrial robot. This result is related to the fact that collaborative applications often don’t need to be as accurate as industrial ones. So collaborative robots manufacturers don’t push their technology to be super accurate.
As you can see in the example the accuracy on the industrial robot is twice that of the cobot. This means that there is a lot of precision added to the components of the industrial robot. Which should theoretically reduce the production time, while increasing the quality of the parts produced, but which unfortunately also results in a more expensive robot. If you use your robot to do precision applications with a fast cycle time, you may want to the industrial robot. However, for most applications that involve human cooperation +/- 0.1 mm accuracy is plenty accurate, there is really no need to be more precise than this.
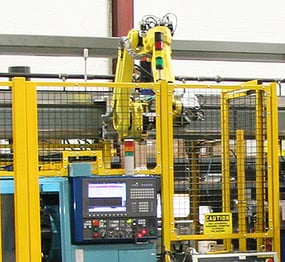
Safety Guarding
This is more an end user savings. In fact, since you don’t have to buy guarding for the collaborative robot on your work floor, you save on the price of guarding and on the space in your shop. Both cost a lot of money. This should be considered in your choice of robotic cell.
In the example, using an industrial robot with a 1,098 mm reach, according to the applied norms, the robot should be able to move freely around this work area without hitting the protective guarding. This means that the area should be greater than 1.2 m2 and this is space that you don’t have for another machine or for easy access by your employees.
Sensors
Depending on your application you may want to have vision sensors or force torque sensors. Most collaborative robot have force torque sensors incorporated into them that are designed to limit the force due to impacts. However, those sensors can also be used for basic force limited applications such as screwing or product testing. This means that you don’t have to buy an extra force torque senor for this application. That being said, we highly recommend using external force torque sensors to have a more accurate reading and data that is easier to treat and understand.
The same principle applies to vision sensors like those on Sawyer. The vision system can monitor the robot’s surroundings, as well as monitor the part in the gripper. So, for an end user choosing a collaborative robot that has embedded sensors can save both time and money.
So, these are basically the reasons why a collaborative robot is cheaper than an industrial one. With lower priced hardware and embedded sensors, no guarding and smaller parts, it is only logical to have a lower price point. If you want to learn more about collaborative robots, you could take a look at our latest version of our eBook on collaborative robots.
Leave a comment