Where Are We Standing With Robot Vacuum Cup Grippers?
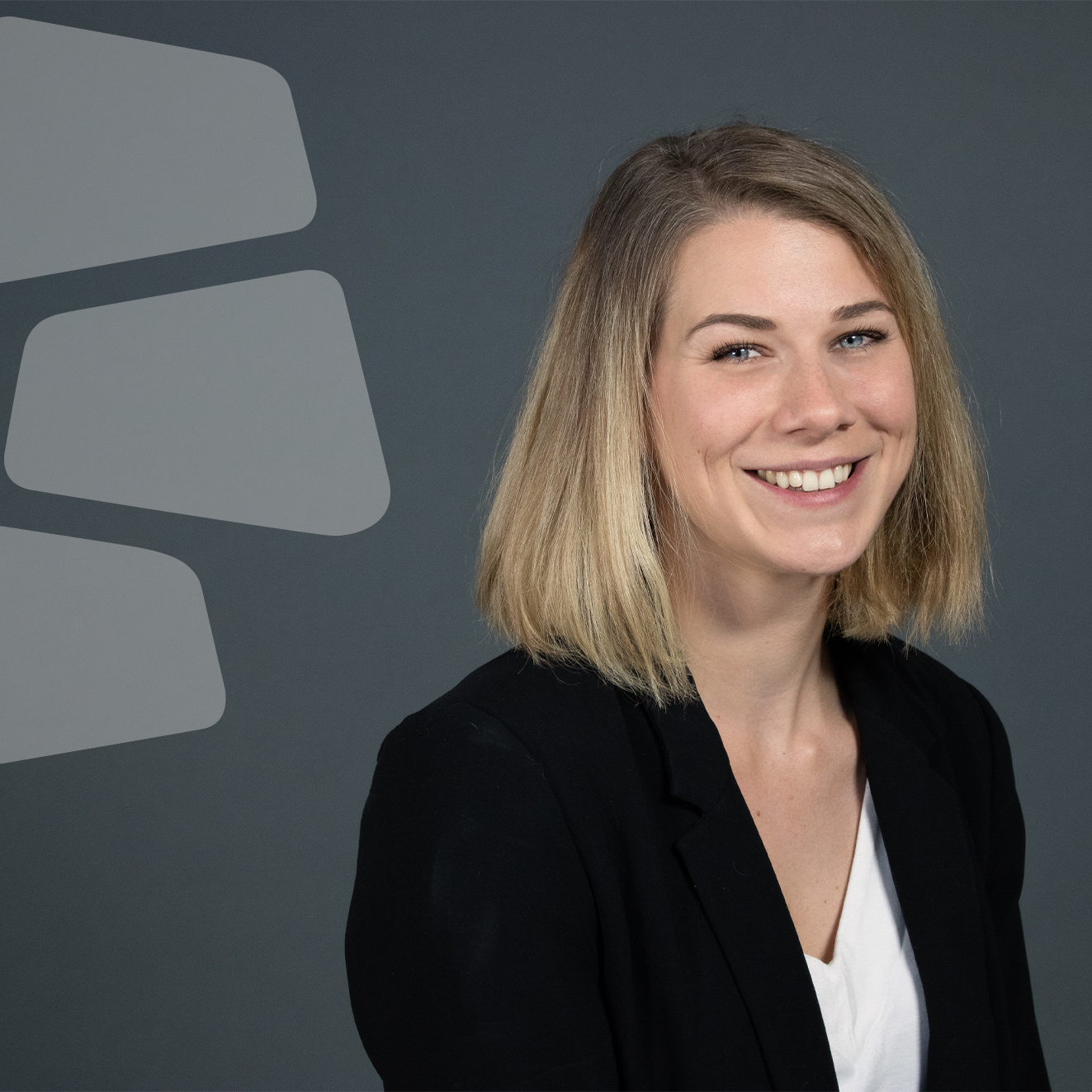
Posted on Jul 11, 2019 in Robot Grippers
5 min read time
Back in 2014, Robotiq CEO Samuel Bouchard wrote “Robot Vacuum Cup Grippers: Top 5 Problems,” introducing the main challenges the industry was facing with vacuum grippers. Now that the industry of collaborative robots has greatly evolved, the vacuum gripping technology has a lot more to offer and is more accessible than ever before.
Since at Robotiq our mission is to free human hands from tedious tasks, we aim to always improve our tools and know-how in order to simplify collaborative robot applications so that factories can start production faster.
As we keep making progress in regards to vacuum grippers and suction cups, we could not miss the opportunity to have a second look at what the problems were back then, and see where we are standing now.
Say bonjour to AirPick and EPick the newest products from the creators of the world's best-selling grippers!
Problem #1 - “Issues with varied surface types.”
Statement: Irregular shapes, uneven and dirty surfaces can prevent efficient gripping.
Two major improvements come into play regarding this matter: the variety of suction cups, bellows, and vacuum blocks, and the vacuum flow rate.
The number of manufacturers and product lines has significantly increased in the last five years (think of Piab’s Value Line® in 2015, Schmalz’s VCBL-GL vacuum block in 2016, FIPA’s Variopack® in 2018) and their take on the problem is to broaden the range of objects that can be held using vacuum grippers.
While advanced filters and filter materials allow working with dirty surfaces, choosing the right bellow structure for suction cups can help a great deal in terms of gripping irregular shapes.
In regards to vacuum flow rate, the various ways of adjusting it now pave the way for gripping heavy, fragile, porous and uneven workpieces. Does the repeatability and accuracy issues remain? Yes and no. Even though finger grippers get the job done, additional components such as a vision system and/or force torque sensor work up to precision for cobots (collaborative robots) equipped with vacuum grippers.
Problem #2 - “Vacuum robot grippers can leave marks on some surfaces.”
Statement: Removing marks can require additional resources, therefore consuming time and money.
In the same vein, the latest technological advancements in vacuum end-effector materials allow users and integrators alike to make the most out of suction systems.
Vacuum area gripping systems can be quite large, but they deliver when comes the time to reduce contact with the workpiece as much as possible. For instance, Schmalz’s FXP area gripping system can be equipped with a protective cover made of foam and mesh that also acts as a particle filter. Plus, changeups are made easy. Angled applications are somewhat of a problem given the size of the end effector and the lack of shear force performance found in vacuum cups.
Oppositely, vacuum cups made of mark-free materials also made their way on the market. Thermoplastic polyurethane (TPU), nitrile-PVC (NPV) and nitrile rubber (NBR) are some examples of suction cup materials that reduce marking.
But then again, it works better when the lifting force is parallel with the object being gripped.
On a different note, with a better control over the vacuum flow, operators can prevent the suction effect which often times lead to surface marking. Limiting the maximum vacuum distribution level right from the user interface solves many problems, and regulating the inlet air pressure of pneumatic tools help in reducing the lifting force.
Robotiq Vacuum Grippers can handle a wide range of applications and are ideal for picking up uneven and even workpieces.
Problem #3 - “Vacuum robot grippers are compliant.”
Statement: Too much compliance can position gripped workpieces at undesired angles and reduce repeatability in picking and placing.
Too much compliance is like no compliance.
Traditionally, pneumatic vacuum grippers allowed for a quick grasp of workpieces in industrial applications that required little or no precision. They were chosen because of their versatility and ease of use. There was less programming to do, they were cheaper than robotic grippers and highly customizable. Their compliance prevented them from being used in areas where repeatability was a top priority.
But the early days of vacuum grippers are long gone. What has changed since then? Using vacuum grippers opens up a vast field of automation projects in collaborative robotics. Not only can vacuum grippers hold complex, burdensome or flat objects, but they also can be positioned accurately—in industries such as electronics, automotive, precision assembly, and much more. Obviously, the main advantage lies with the integration of vision and force sensing systems on cobots—which is also possible with industrial robots, albeit more complex.
Problem #4 - “Vacuum robot grippers need custom end-of-arm tooling to support them.”
Statement: The design of custom end-effectors can be tedious and costly.
Piab’s application configurator, Robotiq’s brackets, and the various patented air nodes are only the tip of the iceberg: everything is about customization. Reusing equipment in multiple applications is key. Chasing fitting suppliers should now be a thing of the past.
While changing a suction cup is a lesser task, mounting different holders depending on the application can be quite a burden.
Flexible holder systems, decentralized vacuum generators, manifolds on racks, universal valve terminals… You name it! With smaller vacuum generators and adaptable holding components, there is no limit to what the cobot can perform. Sawing aluminum extrusions should not be a part of the integration process. Take the time to think the task over and explore what is out there. Then equip your robotic cell with useful, versatile components.
Problem #5 - “The usual problems with compressed air.”
Statement: Compressed air is not energy efficient and can introduce dirt.
The main breakthrough here is the democratization of electrical vacuum grippers. Vacuum generators without the need for compressed air supply are a cleaner solution, of course, but also boasts some other features. Among others, they can be used for performing stationary handling tasks, and installed on mobile robot cells.
On the other hand, since we cannot simply rule out the compressed air vacuum solutions, the latest programming modes and methodologies allow for less air leakage, which means less waste. Robotiq’s Smart mode used with their line of Vacuum Grippers is just an example. Claiming an automatic timeout delay, the Smart mode prevents energy waste and at the same time puts forward a safety feature.
Simple use of Regulator and Filter can solve most problems of dirt in the air. Part of the usual FRL where the lubricant is avoided, it is a standard piece of equipment between air source and the actual equipment. Advanced air equipment as screw compressor improved compressed air production reducing the cost of the use of air.
In a nutshell, thanks to the latest materials and shapes, precise vacuum flow and full customization of end effectors, the steady progress in recent years led to the entry of vacuum grippers in particularly niched industrial areas, and to their grand foray in the cobot industry.
Leave a comment