What Risks Do Production Managers Face When Implementing Robotic Solutions?
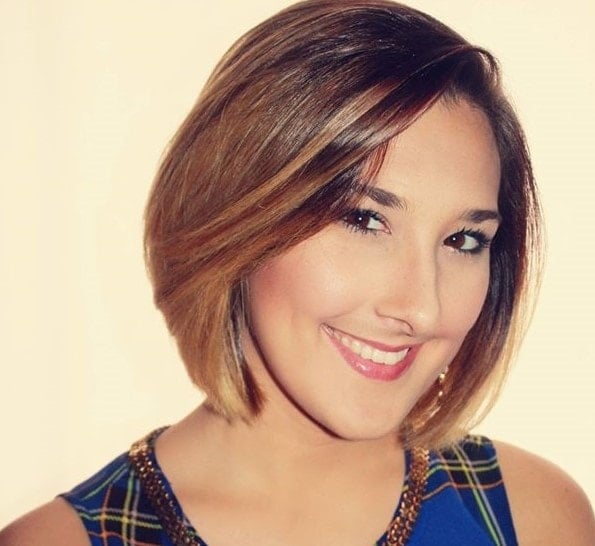
Robotic solutions solve a wide variety of problems for manufacturers. They increase efficiency while never getting tired or slowing down the way a person would. They also work independently once they’ve been programmed and provide a consistent level of quality in everything they do.
In essence, they are the perfect solution for production managers, but there are some caveats. Certain risks are involved when implementing robotic solutions, but with the right approach to education and training, they can be avoided. Let’s explore some examples of these risks, and what you can do as a production manager to avoid them.
3 Potential Risks When Implementing Robotic Solutions (And How to Avoid Them)
Industrial robots have become a huge boon for the manufacturing industry in recent years. As the technology grows, so too does the safety standards attached to them. There are international safety standards, known as the ISO 10218 that help employers understand and mitigate the risks of working around fenced industrial robots.
At the same time, new technology is on the rise that provides additional safety for workers who are within proximity of these technological marvels. Here are 3 risks associated with robotic solutions, and how you can prevent them.
1. Human Error
As with anything, the possibility of human error is still a risk when implementing robotics into the workplace. The solution here is to perform a risk assessment. To prevent impact with robots, it's important to understand the potential risks of having them on the factory floor.
If a robot isn't collaborative, there's no reason for human to enter its workspace unless they are an operator and the robot is shut down. In the case of collaborative robots, it's important for the production manager to familiarize themselves with the ISO standards so they can understand the safety measures and guidelines in place.
2. Cybersecurity
Henrik Christensen, executive director of the institute for robotics and intelligent machines at the Georgia Institute of Technology, brings up a valid concern about the vulnerability of connected devices. “The biggest risk is cybersecurity; making sure that all these new systems are safe and that people cannot hack into them.”
This ties into an initiative being handled by Cisco Systems and Rockwell Automation, who are partnering with Fanuc to build a network platform that would connect robots in factories together. They can learn from each other’s errors, collect data, and even apply machine learning algorithms to self-learn.
The robotic industry is always focused on safety, but as robots enter into the Internet of Things, it’s important for plan managers to ensure that no stone is left unturned when it comes to security. While one may not think about cybersecurity, it is indeed a valid concern.
3. Safety of Humans in the Robot’s Proximity
Our final risk is one that production managers may feel is an issue with collaborative cobots, which would work in proximity to human counterparts. This is a risk that has been mitigated through technological advancements in the field of robotics.
For example, current technology allows robots to slow down or stop when people are nearby. The force that a robot applies is measured by current in the robot's joints. This force-limiting is always in place with collaborative robotics and does not require an external sensor.
Finally, cobots tend to be lightweight and slow so they don’t cause any risk to their human counterparts. This risk is something that can be alleviated with proper education and understanding of today’s safety standards.
Final Thoughts
There are risks involved with anything that’s automated in manufacturing, but robotics only pose risks if you’re not properly educated on how they function and what safety features they include. Performing the proper risk assessments with this information will ensure that all necessary steps are being taken.
Knowing this, you can rest assured that your transition to robotics will be a smooth one. How do you mitigate risks with robotics in manufacturing? Let us know in the comments!
Leave a comment