Robotiq Releases a Protective Cover
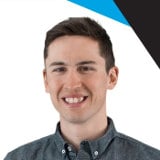
Posted on Feb 18, 2016 in Robot Grippers
3 min read time
Safety has always been and will always be a true value in our company. For the last couple of years we have been working with collaborative robots and a lot of our products have been used in collaborative applications (aka alongside humans). We have been working on making our products as simple to use as possible, but always with an attention to safety. Along these lines, we have designed a protective cover to eliminate any type of pinching that might be possible from the joints of the 2-Finger 85 Adaptive Gripper. Here's why we did this.
Working alongside humans
Since the start of collaborative robots a lot of attention has been put on the safety of workers. In the beginning by removing the preconceived idea of fencing around robots, some people were apprehensive about using these robots. As time went by a lot of customers where then happy to remove the fencing, this saved space and made their employees work in collaboration with a robots instead of separate from them. However, the safety concerns will always remain. How do you make a work cell as safe as possible by reducing or eliminating all potential dangers? Collaborative robots have been designed to be force and power limited, have pliant shapes and/or work with limited speeds. All of this is designed to eliminate injuries (crushing, stabbing, potentially fatal) that an impact with a fast, sharp, feeling-less robot might entail.
One step closer
That is exactly where we have drawn the line. In fact, we know that safety is a big concern for all companies, even for some of our most satisfied customers. So we decided to make available for our 2-Finger 85 Gripper, a cover that would bring it one step closer to 'collaborative' status. By adding a protective cover over the finger linkages, this allows the pinch points to be blocked, so that all potential body parts (mostly fingers here, but really why would you stick your finger in there) cannot possibly be crushed in this part of the Gripper. This cover also eliminates exposure to the edges on the finger linkages.
Notice that the Gripper keeps all its initial functionalities, by adding this protective cover, you do not reduce the flexibility or strength of the fingers.
What about grasping forces
There is still no ISO standard or regulation that talks specifically about 'collaborative end effectors or tools', but as we went through the new ISO/TS 15066 which talks about robots and robotic devices (which is pretty broad); we noticed that the maximum allowable force for human hands and fingers is 135 N. As our 2-Finger Grippers are rated to reach a maximum of 220 N +/-10%, obviously, at max, we are over the 135 N limit. There will always be a juggling act to be done to have the right amount of pressure needed to manipulate your product establishing a firm enough grip to hold it and not too much force to crush it as with fragile or brittle pieces. Notice that you can adjust the force of the Gripper at every step of the programming. In fact with 256 possible gradations you can adjust your force very precisely and make sure that the 135 N threshold is not surpassed.
In my own opinion this isn't bulletproof, because someone can always mess with the settings, but we have a very accurate and repeatable product that can remain on the same force value over a long period of time. In other word, if you set your force setting today, it will last for the whole Gripper lifecycle.
I want one for my Gripper
So if you are looking for extra assurance, we are currently selling this protective cover. Notice that the cover will only fit on version three, V3, of the Gripper (the one with the round base/wrist, not the rectangular one). If you would like to ask for a quote, here's the email of our application engineer (nicolas.hardy@robotiq.com), who will be able to help you in choosing the right Gripper and how to make it safe for your application. Of course, you can always check out our 3-Finger Gripper, whose force settings are lower than the 2-F model, but then you have to determine if it will work as well for your application.
Once you have analyzed the robot and its tool, you still need to make sure your application is safe to work alongside humans. If your robot and gripper is fully collaborative and you are manipulating knives... well… you've might have missed something. To learn more about this part of the risk assessment, we have created a document that will help you realize your first risk assessment using a collaborative robot.
Leave a comment