Robot vs Cobot: Which is Best for Your Palletizing?
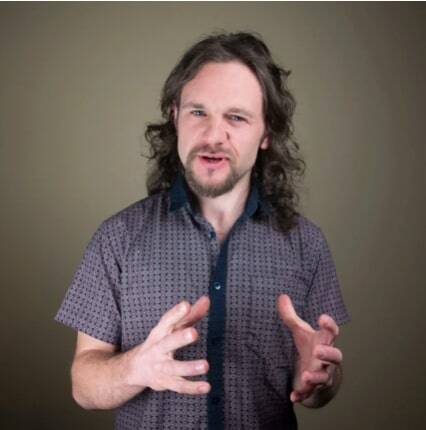
Posted on Mar 08, 2022 in Palletizing
5 min read time
Which is best… an industrial robot palletizer? Or a collaborative robot palletizer?
You might be unsure which of these two robotic solutions will be right for you. They share many similar properties. At first glance, you might even think that they are the same.
Conventional industrial robots have been used for palletizing for decades. They have a long track record and are used extensively in many industries. Should you go with this more "established" approach to robotic palletizing?
Photo credit: Mech-Mind Robotics
Collaborative robots, on the other hand, are a more recent solution. Although cobots have been around for well over a decade, cobot palletizing is still relatively new. Cobots are very accessible to new users. Should you go with a cobot palletizer instead?
There are several factors to take into account when you're looking for a robotic palletizing solution.
When you understand the differences, you can make the right choice for your business.
What you need to know about palletizing with a robot arm
Industrial palletizing robots. Collaborative palletizing robots. Are the two really that different?
It can be helpful to remember the fundamental similarity of these two solutions. Both are an alternative to the conventional approaches to palletizing:
- Manual palletizing — Here a human operator carries out the palletizing task. It is usually an inefficient approach and has many disadvantages. Any type of automation can be better than manual palletizing.
- Conventional palletizing automation — Here an entirely automated, customized palletizing machine is installed on your work floor. Conventional machines can handle very high volumes, take up a lot of space, and tend to be inflexible to changes.
Compared to both of these, any robot palletizing solution can be a huge advantage for your business.
Both types of robots are more flexible than conventional palletizing automation. It's much easier to reprogram a robot to handle changing product lines. Robots also support putting more varied shapes and sizes of products onto the same pallet.
Robot vs cobot: A comparison for palletizing
How do industrial and cobot palletizing solutions differ? Some key differences will affect your choice of robot.
There is a reason that industrial robot palletizers tend to be used by only the largest manufacturers — they require a significant investment of time, budget, and floorspace. While they are more flexible than conventional palletizing machines, most industrial robotic systems are best suited to higher volumes.
One of the reasons that collaborative robot palletizing is so popular right now is that is accessible to many more companies. The systems tend to be smaller and are much easier to deploy than industrial robots.
Here is a comparison table of the main relevant factors for palletizing robots:
Industrial Robot | Collaborative Robot | |
---|---|---|
Speed | Very fast. 10-40 bags per minute or more with layer palletizing. | Faster than you might think. Up to 13 cycles per minute. |
Payload | High for many systems but varies 5-800 kg | 16 kg |
Programming | Hard. Requires extensive specialist knowledge. | Easy. Anyone can do it with minimal training |
Size | Huge. Requires a lot of floorspace. | Small. Just larger than 2 pallets. |
Fully loaded cost* | $$$$ | $$ |
Max pallet height | 1-3 m | 1.5-2.75 m |
Safety requirements | Requires a fence and often extra sensing. | Can require some sensing and fencing. |
Ease of redeployment | Hard. Requires a lot of work to switch to another task. | Can use the robot for other tasks if necessary |
Deployment time | Several months. | A couple of weeks. |
* What is a fully loaded cost? In case you're not familiar with this term, fully loaded costs include both the direct cost of the robot and the indirect costs associated with the deployment. These indirect costs add a lot to the cost of an industrial robot system.
What you can learn from this table
Both industrial robots and collaborative robots have unique strengths.
The fully loaded cost is a clear differentiator. But both robotic systems can have a good return on investment so this is less important than some of the other differences.
Three important factors for many users are deployment time, ease of redeployment, and ease of programming. These are what make collaborative robot systems so much more flexible than industrial robots. They are easy to program, deploy, and redeploy.
People often think that the maximum height of the robots will be very different. Industrial robots are a lot bigger. However, cobot products like The Palletizing Solution can reach up to 2.75 m, which is not much different from an industrial robot. The real difference is in the payload — industrial robots can lift much more weight.
Speed is also a difference that people often assume will vary more than it does. However, collaborative robots can have a similar cycle time to industrial robots. The reason that industrial robots can handle much higher volumes is, again, their higher payload capacity. A large industrial robot can lift a whole layer of boxes or bags in one cycle. A collaborative robot can only lift one box or bag at a time.
How to choose a palletizing robot
Which is the best palletizing solution for you? An industrial robot or a collaborative robot?
The answer will depend on your palletizing needs, your available resources, and your experience with robotics.
If you need to process a high volume of products or you are palletizing very heavy objects, an industrial robot may be the best solution. If you want a highly flexible system that is easy to use and quick to deploy, a collaborative robot is probably the best bet.
It's often helpful to start by defining the performance requirements of your system.
You can ask yourself questions like:
- What throughput will we require?
- How many different product lines do we need to palletize simultaneously?
- What are the size and shape of the objects that we will be palletizing?
- Do we have automation experts on our team who can carry out the deployment?
It's also advisable to see your robotic solution in action before you buy it. You can see videos of our cobot palletizing solution on our applications page along with our interactive online configurator.
Which type of robot looks most suitable for your palletizing needs? Tell us in the comments below or join the discussion on LinkedIn, Twitter, Facebook, or the DoF professional robotics community.
Leave a comment