Q&As When Developing a Robotic Manipulation Cell (Part 1of 2)
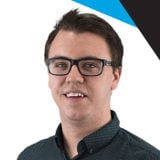
Initial investigatory questions are listed in this article, I recommend you get a piece of paper to help you track your answers along the way. You can then brainstorm potential solutions based on these answers.
For the sake of this article, comments to some questions will be addressing a specific application, i.e. where various parts are picked by the robot arm from a conveyor belt passing in front of it and using a camera for a quality check, then dropping the part inside a box afterwards.
Looking at the parts
The first questions you need to ask yourself are really about the parts themselves. In addition to the following questions, you can consult the following blog article.
1. How many different parts does the robot have to pick?
2. What are the variations across the different parts (size, weight, shape)?
3. What are the maximum and minimum specs for the parts (size and weight)?
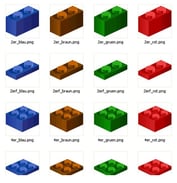
Note: When looking at the variations between different parts, try to see any similarities in shape and size across the components to find the best potential places for grasping. For example, let’s say you want to manipulate the blocks in the picture shown here, you will see that these blocks have different sizes. However, notice that there is always one side of the block which is the same size for all the blocks (length = 2 button head). Therefore, always picking from this side would allow you to use a single-stroke gripper. On the other hand, if no trends can be observed across the different parts, you will have to look for an EOAT (end of arm tool) that is flexible enough to grasp all the parts or in a worst case scenario, many EOATs with tool changers.
4. Are the parts fragile?
Note that if the parts are fragile, you obviously need a tool that won’t damage the part. You can adjust the pressure of a pneumatic gripper to reduce force, but pneumatic grippers are prone to pressure variations from your pneumatic lines. Using an electric gripper provides a more consistent and reliable grasping force control.
5. What material are the parts made of?
This may eliminate some gripper options like suction cups if the material is porous or electromagnets if the material is non-ferrous.
Looking at the company
Some elements regarding the company are also useful to look at before implementing a robotic solution.
1. What is your team’s level of expertise in robotics and automation?
For your project, select components based on your experience and level of expertise in robotics and automation. Lots of time can be spent developing, troubleshooting and improving vision algorithms, robot programs or code for the automation components in your project. If you are comfortable with developing custom code, go ahead, you may be able to save some money. However, be careful because you may end up doing a lot more work than expected in the development phase of your project. On the other hand, if you want to ease integration, select components that are easy to use for your application. In our introductory example, if you are experienced enough, you could use an industrial robot, develop your own vision algorithms for the quality check and develop a specific gripper that could adapt to the various parts to be picked. On the other hand, you could use an easily programmable Universal Robot, a 2D smart camera with built-in vision algorithm libraries and one of Robotiq’s Grippers, say the 2-Finger 85 Adaptive Gripper to grasp the different parts. The Universal Robots bundle/kit for Robotiq Grippers makes integration plug and play with Universal Robots. So your best bet is to try and keep things simple!
2. Does the company have some standards for component selection?
When looking at the project you might notice that some components/features are already present in the shop. Trying to stick to the same brand or the same design standard, will save you time when it comes to troubleshooting, maintenance and repair. You will also reduce your inventory of spare parts. For example, if you need to include a camera in your project, try to stick to the same camera brand running the same software as the others found in your shop. Your technicians will already be familiar with troubleshooting these! However, if those systems are outdated or simply did not work as expected, don’t stick with the same thing just because it is what you have always used. Try to choose components which will be flexible enough to work across the factory floor.
Hopefully the above Q&As have helped you to figure out some details of your application. Some more Q&As regarding the process and your surroundings will come later on in another article.
Related Articles:
Choosing the right gripper for your robot
Choosing the right gripper for your environment
Leave a comment