Part Ordering Using Weight Measurement AKA Force Feedback
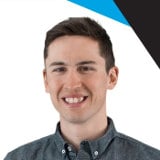
Posted on Jun 25, 2015 in Robot Grippers
4 min read time
In the last couple of years, robots have been given a lot more senses than they used to have. Beginning with vision using cameras and various vision systems, they are able to monitor their surroundings. Now with devices such as force torque sensors, robots are able to feel what they are handling. Here is a demonstration of what robots can detect when they grasp something.
The Demo
As you can see in the video below the demonstration is using the weight of the hockey puck for the ordering system. The robot is grasping the part one after the other by touching the top of the piles and determining the height of the puck tower. Afterward, the robot calculates a height offset, opens the Gripper and then goes and grabs the puck. Once it is in the Gripper, the weight is then determined using force feedback and the robot can then decide where to place the puck.
The first step of the application uses force feedback when the Gripper is touching the puck (seek mode). Once it detects a force (the puck) the robot registers the position of the tool and can then determine the height to go down to for grasping. Once the puck is grabbed, the weight (force) of the puck is acting in the opposite direction from the first operation. A threshold will have been set to make the decision in the program. The robot then figures out the difference between the blue (4 oz) and the orange (10 oz) puck. Once the pucks are correctly identified, the robot places the puck in the corresponding pile. The program continues until the Gripper hits another puck (seek mode) or the empty table. The robot is pre-programmed with the table height, so that it enters another loop that will reconstruct the puck pile.
The major advantage of using force feedback in this application is to be able to determine the weight of the objects, but more importantly to be able to run the program without any notion of the tower height. So, regardless of whether the pile is 1 or 10 pucks in height, the robot is only looking for the next surface (seek mode) and doesn't have to ''remember'' the last puck height or anything like that.
This demo was shown during ICRA 2015, as well as for the Finals of DARPA Robotics Challenge.
Devices
The Robotiq FT 150 Force Torque Sensor is doing the force sensing job in this demonstration. This devices can be used for many different applications, such as assembly tasks, product testing and hand-guided programming. The device is very sensitive and immune to external electrical interference. For further information on this device, please visit the Robotiq website.
The handling task shown is completed by a Robotiq 3-Finger Adaptive Gripper using custom fingertips. This Gripper is designed to adapt to different geometries. It has been featured in the DARPA Robotics Challenge, as well as other research projects around the world. The custom fingertips in this particular application are designed to grasp round objects such as the pucks. The B and C fingers are equipped with special rotating fingertips, so they can adjust themselves to the diameter of the object.
Last but not least, the robot used in the demo is a Universal Robots, UR5. The robot has been chosen for its easy programming features and especially because of its safety parameters. Since the demo has been shown on a tabletop without any kind of guarding, the safety aspect had to be considered really seriously. Since the robot is force limited in each of its joints, it makes sense to use this kind of collaborative robot for the safety of the people running around it. Notice that since the UR5 is equipped with embedded force torque sensors, these could have been used for detecting the puck height and weight as well, however, then there would have been no need for this demonstration and also the resolution of the sensors is more limited, which means that you cannot get as much precision using the robot arm sensors. Which makes sense since they weren’t design for this, they were basically designed to detect impacts.
Notice that every Robotiq device has an all-inclusive bundle to fit Universal Robots. Basically the mechanical and software interface between the robot arm and the end-of-arm Gripper have been designed to fit with each other as easily and seamlessly as possible. If you want to get the programming path for this application, you can download the different files by clicking on the big colored button below.
Leave a comment