How to Reorganize Your Shop for a Collaborative Robot (Part 1)
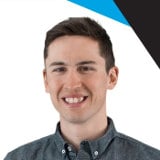
Posted on Apr 02, 2015 in Collaborative Robots
9 min read time
So you are thinking about introducing a robot into your manufacturing process. You have to decide which robot to use, the different tools you'll need and all the necessary accessories, but have you thought about how you are going to set up your robot on your work floor? I am not talking about where to position your robot, I mean what you need to do to run your robot smoothly and make life easy for your employees. Take a look at this short list to review a couple of tips on what to know when integrating a collaborative robot in a machine tending application.
All collaborative robots are able to execute machine tending applications, however, I have learned over time that it is not just about putting a robot in front of the machine that assures you are ready to go (well you can do that too!). In fact, you need to think a little bit further and figure out different ways to insure a stable process. Since there are several models of collaborative robots, I will not go into depth on the details regarding what to do with your robot. You should consider the following points more a heads up about what would be good to look at. Make sure to follow the links in the text that will take you to videos and blog articles for the applications discussed.
Robot Fixture
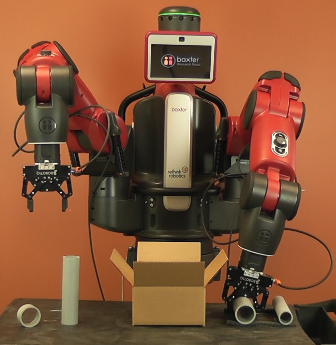
As you may have guessed from the picture above, there are a wide choice of collaborative robots available and even more numerous ways to attach them. Some are mounted on wheels and some have to be fixed on a table or stand. The baseline is: For precision your robot has to be fixed at the exact same spot each and every time it runs. It is one thing to lock the wheels on the floor, but it is another thing to position the robot at the right position and with the right orientation.
In other words you need to find a way to screw, pin, or lock your robot onto a constant reference point on your work floor. Try to use mechanical devices to make sure your position is always the same. For example, if you use a Baxter, it can roll in all directions, make sure to have 3 or 4 anchors in the ground to fix it securely. This way you will be sure that the robot will run the same program the same way it did the last time. Then you will spend less time in reprogramming your robot.
Imagine a situation where you tend your machine with your robot for a certain amount of time, move the robot around to other applications and then bring it back a couple of days later. You will have to guess the previous position for the robot, try the program, figure out if the program is off and reprogram a couple of points to make the program work again. Instead of that you could just have fixed the robot to anchors and run it full throttle.
If you think that your robot will stay in one place over the long term, don't forget that you will still have to do maintenance on the machine. At some point, you will probably have to move your robot, so making your set up sectional also allows for easier upgrades when you want to improve your system in the future.
Part Input
Once again the baseline is positioning. You want to know where the parts are to grab them, quite intuitive, however to implement this is another thing. There are many different ways to locate a part.
- Array: Most machine tending applications are done with simple array allocations. This is the easiest and simplest way to organize parts. And most robots have pre-programmed routines that can execute this kind of motion. Arrays can be integrated into platters that can be switched or used directly on a table. If you use platters make sure to produce double batches so the platters can be filled by the operator (or another robot), while the robot is feeding the machine.
-
Single Allocation: Inclined plane or industrial shakers can be use to bring the parts to the exact same position for every grasp. This means that the robot doesn't have to know where to pick up the part or even what the part orientation is, it just grabs at the exact same place each and every time. This is a simple technique, but unfortunately won't apply to all parts.
-
Drawers: This is an awesome way to bring your part to the robot, also it is space efficient since it doesn't take a lot of square footage. The parts are ''piled'' in several drawers. The robot can open the different drawers and grab the part or the drawers can be automatic. In some cases, drawers are arrays of parts positioned one above the other.
-
Vision: Is mostly used in moving processes such as conveyors. The vision system can be paired with encoders on the conveyor and ''remember'' the position of the part while it still moving in the direction of the robot. Vision systems can also be used when parts are randomly positioned. The camera can locate the part and ask the robot to change its approach depending on the part orientation. Vision systems are generally more complex and costly systems to implement, but in some cases this is the best option.
- Force Sensing: A good mix of arrays and vision. In fact some robots can be fitted with Force Torque Sensors that give the sense of touch to the robot. This means that on a given path the robot can identify where the parts are. So, most of the time you can place your parts in an array and ''ask'' the robot to go through the array to sense and locate the part. This approach is similar to a vision system since it also allows the robot to locate the part, but it may be cheaper to buy an FT sensor than a whole vision system.
For a piece of general advice, you should start with workers bringing parts to the robot. You should also start with a simple ordering system and then you can get more complex later on. Buying a collaborative robot can be a big step in the organization of a business, make sure to start nice and easy. You can get the more complicated stuff afterward.
Part Output
You have to think about the simplest way to get the parts out of the system. Is there going to be a secondary operation on the part? Is the part going straight to the customer? How is the part going to be packaged. This will all have an impact on how you will dispose of the parts after they have been processed. A simple box or crate can be sufficient, however another array could keep track of the parts and help the quality assurance department if they need to find the root problem in a production error.
This was just an introductory article concerning what you should look at when installing a collaborative robot on a work floor. Let me know if you have other concerns about integrating robots into your business. This will help direct me with my next article on this subject or leave a comment and don't forget to follow Robotiq's blog.
Future articles: I/O between robot and CNC machine, machine repositioning and more.
Leave a comment