How to Determine the Processes that Need Automation?
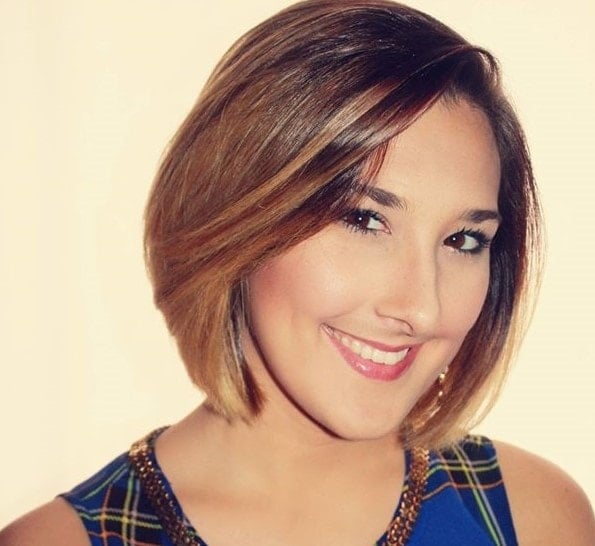
Posted on Sep 24, 2019 in Automation
5 min read time
Humans and machines are already working side by side to build and maintain a more efficient manufacturing infrastructure. But the full potential of automated processes is yet to be leveraged by plants all over the globe - according to a McKinsey study, as much as 64% of working hours that are being spent on manufacturing-related activities are automatable with currently available technology.
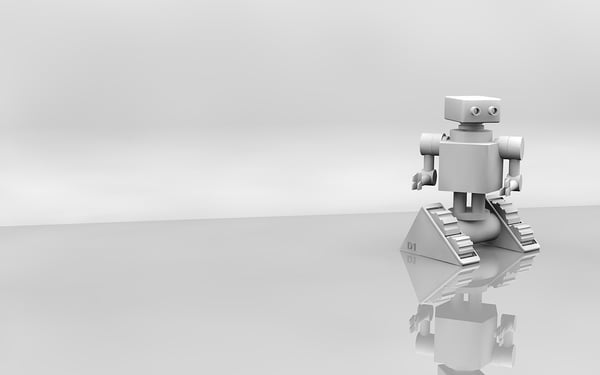
This opens at least two important questions for you:
- Can modern-day manufacturers still succeed without automation?
- If not, then how and where do they start automating processes?
Stay with us as we explore the potential for automation across the industry, examine the fate of manual-only processes in manufacturing, and establish a framework for determining the processes that are no longer financially viable without some help from collaborative robots, AI, and machine learning.
To Automate or Not to Automate, the Question Is Now
Work process automation is a global trend, but is it really so revolutionary that everyone should jump aboard with no questions asked? Is automation in 2019 truly about efficiency and effectiveness or is it only a zeitgeist that will eventually pass? Does automation make you better or only competitive?
But instead of asking why automate? let’s ask why not?
The fact that manufacturing leaders are already fully automated threatens to disrupt the industry. The number of robots deployed worldwide is getting north of predicted 2.6 million units, with China being the automation trendsetter. The future of robotics is now and there’s no running away from it.
According to the cited McKinsey study, $5.1 trillion paid to workers can be saved by automation; industry leaders will not stay deaf to this stat. As a result, the need for experts comfortable with automation will grow, overturning the skeptics. Technology will transform the industry as we know it.
You can be a part of the change or you can get run over by it. One thing is for certain - at this point, widespread automation is inevitable.
If You Can’t Beat Them, Join Them (and Reap the Benefits)
In the US, more than 98% of manufacturers qualify as SMBs, which puts what we’re talking about in perspective. With global competition embracing automation as we speak, small manufacturers have no other choice but to leverage every potential for growth. Automation is an enormous part of that.
These are the four key benefits of robotics and automation in manufacturing:
- Automation equals higher productivity. It doubles or even triples production.
- Automation equals lower costs. It uses sustainable tech and boosts efficiency.
- Automation equals high-level focus. It repurposes workers for creative tasks.
- Automation equals workplace safety. Risky processes are delegated to robots.
Automating manufacturing processes is about branding as well, especially in terms of awareness, competitiveness, relevance, and integrity. A more productive plant boasts not only better production but also happier employees. In that context, the benefit number three on our list is very interesting.
In case you’re worried about losing your job, it answers another important question.
Although advanced robots can perform cognitive tasks as well, their main field of expertise is manual work. In manufacturing, this allows the ability to focus on strategic, high-level tasks that rely on creative thinking. Machines will not replace humans; they will only make their jobs more meaningful.
How to Determine Process Automation Value and Focus
Manufacturing automation boasts incredible benefits, there’s no doubt about it. But in order to reap these benefits, “automation options must be considered and evaluated using a clear strategy focused on reducing the total cost of operations”. You must determine the processes that need automation.
In other words, if it ain’t broke, don’t fix it.
So before you jump aboard this trend, ask yourself the following questions:
- What are your trying to fix?
- Where is your plant at risk?
- Where can you improve efficiency?
If you decide to automate, pinpoint the root problems first.
According to the industry experts interviewed by Automation World, you first need to “target the dysfunctional systems that are hard to work with, most often responsible for unplanned shutdowns, adding to production costs, or barriers to achieving potential new business opportunities”.
Then, you should turn to processes that could be more reliable and productive.
This is the second phase - optimization. It’s where you reevaluate your current performance in the context of industry demand and in comparison to leading competitors. You need to determine what are the greatest risks to achieving your production goals and staying relevant in a volatile landscape.
The mistake manufacturers frequently make is automating without monitoring, documenting, and analyzing current processes first. Techniques such as the use of process flow diagrams and cycle time analysis, in addition to continual data review, are crucial for identifying problems and potential risks.
Factors to Consider Before You Start Using Automation
Using insight from their 2017 research, automation experts from McKinsey have recommended five important factors manufacturers need to consider when making decisions going forward. The idea, of course, is to unlock technology’s immense potential and generate long-term value from automation:
- Technical feasibility
- The cost of developing and deploying hardware and software
- The cost of labor and related supply-and-demand dynamics
- Higher levels of output, better quality, and fewer errors
- Regulatory and social-acceptance issues
Consider this the third step. Together with system monitoring and thorough analysis of current processes, it will help you determine what needs to be automated, to what extent, and at which cost. Even when automation makes business sense, adoption can take time. Don’t forget to count that in.
The key takeaways for you employ in your everyday processes are:
- The manufacturing industry is becoming increasingly automated.
- If you continue to do things manually, you won’t be able to keep up the pace.
- Collaborative robots won’t steal your job; they will only improve it.
- The only way to determine where to start is to look at your current performance.
- Weigh out the benefits against the costs of process automation.
Have you already started experimenting with automated manufacturing processes? Whether you have an experience you want to share or a question you need to ask, let us know in the comments!
Leave a comment