Getting Started with Collaborative Robots: Machine Tending
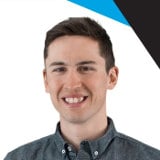
Posted on Mar 09, 2016 in Automation
6 min read time
You are looking at your first robot integration, you have heard about collaborative robots, but you don't know where to start? You’ve come to the right place. We have put together this blog post series to help you figure out which robot will match your specific application. For our first blog post, we'll start with machine tending applications.
Machine tending constitutes the largest use of collaborative robots in the market. Before going too deep into details, let's start with simple definitions.
Machine tending application using Universal Robots UR5 and Robotiq 2-Finger Gripper
What is machine tending?
If you are an up to date machine shop, you probably use CNC machines (lathe, milling, etc.). These machines need to be tended by workers to introduce raw parts and remove them once the program is done. With the global issue of a qualified workforce becoming harder to find, a robot can be used to execute these repetitive tasks and let the worker do added value tasks instead.
What about machine tending wit/h a collaborative robot?
A collaborative robot or cobot for short is a general term used to describe power and force limited robots, robots that can be used without safety guarding or that has incorporated other safety features. This means it can be put beside a machine or a person and set to perform a certain task without needing to be fenced off from the surrounding environment.
That being said, to introduce a cobot around a CNC machine and program it to load and unload parts is not as simple as it sounds. You will need to choose a robot that can accomplish the job and that can reach a level of performance comparable to a human worker. To help you choose the right robot for your machine tending automation, we have listed the different things you need to consider.
Robot Specs
- Payload: The payload is the total weight the robot can carry. You need to weigh your tool and the heaviest raw part you want to carry. This will determine your robot payload.
Tip 1: Calculate your part weight by multiplying the volume (W x L x H) by its density (g/mm^3).
Tip 2: Give yourself an extra 20% payload weight to be able to reach maximum accelerations and make sure not to create an error while running the program. - Repeatability: Your machines are super repeatable and you want your part to be precise, however, you do not need to have a robot that is as precise as your machine. In fact, in most cases, robots will be used to do first setups where the part is usually larger than the finished part, which will allow a small variations in positioning.
Tip 1: The robot should be able to repeat within 0.1 mm. To ensure repeatability you can use mechanical stoppers or go all out and use a force torque sensor.
Tip 2: Make sure to leave at least one axis 'free' when inserting a part in a vice or lathe, this will prevent wear on the robot actuators. - Reach: The robot will need to take a part from somewhere and place it in the machine. Measure the distance between these 2 points and divide it by 2. This will give you the minimum reach that the robot must have.
Tip 1: If you need a large reach, your robot's payload will automatically increase; a larger robot is a stronger robot.
Tip 2: The reach also includes the number of axes or degrees of freedom, to learn more about this subject, check out this article.
Gripper Specs
- Stroke: Your gripper is the 'hand' of the robot. But, the gripper is not as versatile as your hand. Grippers work best when parts have at least 2 parallel surfaces. The stroke of the gripper will limit the range of part you can handle. Make sure to measure your largest part and buy a gripper that suits this part.
Tip 1: Try to go with an Adaptive Gripper that can handle different shapes and more importantly different sizes of parts without modifying fingers or the robot program.
Tip 2: When analyzing the parts you're manufacturing, make sure the gripper can handle 85-95% of the parts... the rest can be loaded manually. - Payload: Like the robot payload, the gripper payload is the amount of weight the gripper can handle. Make sure to respect this payload to ensure gripper longevity.
Tip 1: Even if your part respects this payload, make sure the allowable 'torque' of the gripper isn't maxed. If the bulk of the object's weight is always grasped by the gripper fingertips, the gripper will wear prematurely.
Required Workspace
- Machine interface: In machine tending, the interface between the robot and the CNC machine is an important part of the integration. This is not always a given for different machines produced by different manufacturers. In order to optimize your cycle time, you should make sure the 2 machines can talk with each other so they know each other’s status. A bunch of different states should be communicated. e.g. CNC program done, door can be opened, vice is closed, robot running, part in place, etc ...
Tip 1: Make sure your robot and CNC or other machine can share the same interface. Some robot models may not speak the same language as your machine and vice versa.
Tip 2: Do not try to program the robot with a timer, it will not work, trust me. - Ordering devices: To either pick the raw part or place the finished part, you need to do it in a structured way. We usually recommend starting small by adding a very simple device that will position the part at the same spot each and every time. This is easier to program and highly repeatable.
Tip 1: Matrices and stacks are the most commonly used methods for machine tending pick and place applications.
Tip 2: Most cobots have built-in wizards to ease the programming of these paths. - Vice: An automatic vice is pretty much essential if you are going to automate your application. What is the point of automating your pick and place, if you still have to manually secure the vice? Ask your vice/tool provider if they sell automated vices that will fit your machine.
- Door: Cobots can open and close doors. To reduce your cycle time you can introduce small air cylinders managed by the robot or CNC machine’s I/Os.
There are always further details to automating a machine tending application, but this is a good starting point. If you need more information on how to shop for a collaborative robot or what their key features might be, we have put together a complete eBook on this subject.
Leave a comment