Keep Your Employees Safe When Using Collaborative Robots
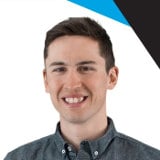
Posted on Jan 20, 2015 in Collaborative Robots
4 min read time
Collaborative Robots will be a big trend in the manufacturing world in 2015. With the introduction of these devices into the workplace there are obvious security concerns. To make sure that the integration of your robotic cell is accomplished in a nice smooth manner, consider the following tips.
The following tips are only a baseline. You can use them as a beginning to your thought process on robot safety. Always keep in mind that the safety of your employees is the most important aspect to consider when introducing a collaborative robot into your workspace.
Risk Assessment
Before employees even enter the robot workspace, a serious complete risk assessment should be done. Any potential hazards should be analyzed and eliminated. The safety risks will depend on each robot or robotic cell. Don't think that if you are using the same robot model for two different operations the same risk assessment can be used. Every applications is unique. You should also consider non-routine operations: programming, maintenance, testing, etc.
Regulation Knowledge
The production director or any manager that will be working with the collaborative cell should know the current rules and regulations surrounding health and safety concerning the robotic cell. Once the manager knows about this, it can be interesting to transfer the information about these rules and regulations to the user of the cell. In fact, by giving more responsibilities and knowledge to the workers this will make them aware of any potential problem points in the cell. Having someone near the workspace that knows the rules can be useful to prevent injuries.
Simulation Software
Once your robotic cell is set, you may want to know how your robot will react to the programming you just did. To do so, you could use simulation software. A lot of robot manufacturers are providing simulation software when you purchase your robot. This type of software allows you to better visualize the motions of the robot. But it can also prevent potential crashes, singularities and self-collisions. It could also be useful to program different paths and patterns off-line without stopping the robot's production.
Safeguards
Yes, safeguards. You thought, collaborative robots meant the complete elimination of any kind of protection. Well, you are right in some cases. In some other cases, safeguarding is more an available function than a requirement. In fact, take the example of a Baxter working on an assembly line that reproduces the exact same motions again and again; a worker bumps it for a random reason and the robot is off-set. The worker then has to reprogram it: 5 minutes. The robot is back to work and it gets bumped again, again it gets reprogrammed: 5 min. The production has been stop for at least 10 minutes without counting all the bad parts that have been produced. The best way to eliminate this problem would be to ''fence'' the collaborative robot. I am not talking about big metal fencing, but just a physical wall that keeps the employees away from the robot, but not the robot away from the employees. ie. something easily accessible.
Vision systems can also be installed in the robot cell. Using this principle, the robot can detect when a human is in a certain zone and can slow down or stop if the worker is too close. Take a look at the following video to have a better idea.
Training
Make sure everyone who's working with the robot or robotic cell is receiving regular training. By doing so, employees will be up to date in the latest technology and will understand the eventual risks that are involve with working alongside a robot. An aware worker is better than an unaware worker.
Robot Speed
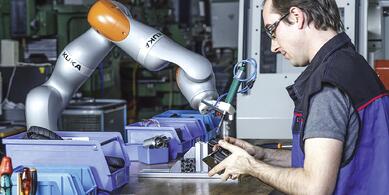
Speed has to be regulated to ensure worker security. Even if the collaborative robot is force limited, a robot arm at full extension can harm a worker at regular robot speeds. Make sure to test and judge what would likely be a decent speed for your application. Notice that the vision system in the video above can eliminate these types of questions.
Stay up to Date
Like any aspect of the manufacturing world, to be competitive you have to stay up to date. Make sure to keep abreast of the latest software and security updates for your robot.
As I said these tips are only a baseline. Now to go further into your safety analysis you need to question your robot integrator, applications engineer and whoever else is involved in your robotic integration. To get further information on collaborative robots, follow the link below.
Leave a comment