Robotic Product Testing with Force Torque Sensors
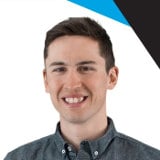
Posted on Feb 24, 2015 in Robotics
3 min read time
Bench testing is probably the best way for a company to test and have quick feedback on a given product's durability. Preliminary testing can be done using this method. During a production run, a sample can be tested to make sure the product is still corresponding to the final specification requirements. With the availability of automation for many companies, robotic bench testing is becoming more and more a necessary part of assuring quality control.
With a constant interest for mechanical egineering applications, I have been looking at different product testing processes over the years. Some have held my attention for good or bad reasons. Here are a couple of interesting ones.
Santa Cruz Aluminum VS Carbon Frame
Anyway, what I want to talk about is a new way to test products. To have a complete product sample throughout the whole production, the routine test that is done on a product has to be done with precision and consistency. In fact, to determine the life cycle of a product, the exact same force has to be applied at a very specific spot to make the test accurate. This is what robotic product testing is all about. With precise tool localization and force feedback, the robot can monitor the whole bench test routine.
Position/Motions
The main interest in using a robot for product testing is to repeat a given motion or to monitor forces. In this case, the robot is repeating the same motion and the vision system is monitoring the tests. The test can then determine the number of cycles that the product can withstand. Introducing a vision system into the robotic cell makes life easier for the operator since he can run the cell around the clock and look at the video if something goes wrong when he is absent. It also helps to pinpoint any mechanical or electrical defect that might have occurred in the production, as by replaying the video over again you can see what really happen during the production error.
The advantage of using a robot instead of a rigid automated system is that the robot can be reprogrammed for a new product. And with a few modifications to the cell, when it's time to test the new product, the robot can be used for this as well. This flexibility allows your production to be back on track faster without spending a lot of time re-designing a new cell.
Force Limitation
The other interesting aspect of using a robot is the possibility to pair a Force-Torque Sensor to it. This device allows you to monitor the force exerted on the item produced. Either by limiting the force applied on the product directly during the production process or by simply telling the test program what force needs to be applied. By doing this you can build a solid database of the amount of force applied per cycle and then you can determine the exact number of cycles that are expected under normal use. Take a look at the following video to have a better idea of what force limited robot product testing might look like.
Force Torque Sensor
This device allows you not only to monitor or limit force on a robot, it also allows you to hand-guide the robot when reprogramming it. When you need a flexible robotic cell that can allow you frequent changeovers, it can be useful to have this type of device to help you program your robot more easily.
This is just the beginning of robotic product testing. These methods will get more sophisticated as the technology continues to evolve. The very rigid bench test tends to be changing for more flexible robotic cells. To have more information on the force torque sensor, make sure to follow the link below and to subscribe to our blog for news on this constantly evolving technology.
Leave a comment