Robotic Gripper Repeatability Definition and Measurement
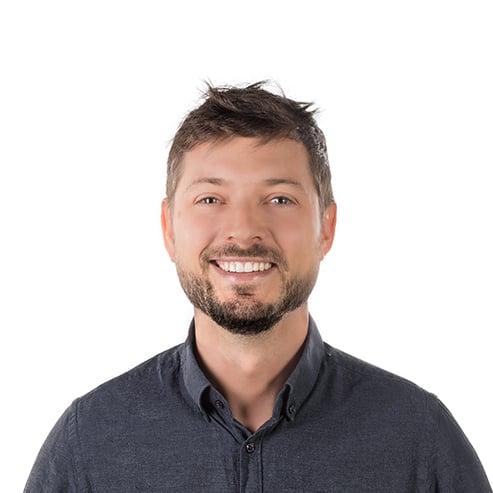
Posted on Jul 08, 2014 in Robot Grippers
3 min read time
On any robotic gripper spec sheet, you will find a measure of the repeatability. What does that term really mean? This blog begins by introducing the repeatability ISO standard used for robot arms, and then explains how gripper repeatability is usually measured in industrial scenarios. As you will see, there is no standard for testing repeatability of robotic grippers, so engineers must ask questions to understand what the repeatability value on a spec sheet really means.
The ISO 9283:1998 Norm for Industrial Robots (Manipulating industrial robots -- Performance criteria and related test methods)
This is the norm used to define the repeatability and accuracy for the end-of-arm position of robots. Let’s start by clarifying some definitions.
-
Repeatability: positional deviation from the average of displacement.
-
Accuracy: ability to position, at a desired target point within the work volume.
The ISO 9283:1998 standard measures the repeatability and accuracy at pessimistic values, using maximum speed of operation and maximum payload. Here is a simplified summary of the protocol:
-
Warm up the robot before testing until steady state conditions are reached (i.e. thermal stability of motors and gearboxes) under a normal 71 degrees F environment.
-
Send identical commands to bring the robot to 3 different positions in sequence.
-
Measure the reached position using 2 cameras and an optical target carried by the robot, or other instruments.
Here is the calculation method to be used to obtain the repeatability from the data:
For N measurements, with commanded position (Xc, Yc, Zc) and reached position (Xr, Yr, Zr):
According to statistics theory, using this formula, it means that the position of the robot will be 99.8% of the time inside the repeatability range.
Repeatability of Robotic Grippers
The methods and testing conditions of the ISO norm are elaborate and complete but they are not meant for grippers. In fact, gripper manufacturers can still use some parts of the ISO norm but each of them adapts it their own way. Even for robots, only about 10% of companies use the complete ISO norm since it is a complex (and costly) method. So we can assume that compliance is even less for grippers.
There are two major differences between robots and grippers when it comes to repeatability:
1. Robots have many axes while grippers only have one. This in fact only simplifies the equations above, but they still hold true. The number of cycles N used in the industry varies from one to another but the ISO norm specifies that excessive testing is not good since command conditions can vary - that said, minimal testing will not provide a strong reliability reading in the results. The ISO norm specifies a minimum of 10 measurements for each axis. For example, Schunk's method of testing their grippers specifies 100 consecutive strokes, while some other companies testing will be based on 10 strokes (minimum) or some others on 40 hours of testing (way too much).
2. Most grippers only have open and closed positions and no intermediate positions, so the ISO method can not be used. In this case, they compare the closed position of the jaws with a fixed datum point. For electric grippers with position control, the ISO method can be used directly.
In conclusion:
-
As there is no official standard to measure gripper repeatability, be sure to compare repeatabilities on how they were tested. Ask the method used by the different manufacturers to determine repeatability so you have apple-to-apple comparisons.
-
Keep in mind that if you have larger repeatability at the robot and / or vision level, they will dominate the overall repeatability. In the end, no simulation will tell you the overall repeatability, you will have to test the integrated system.
Leave a comment