Avoid Common Robotics Hazards by Following These 6 Rules
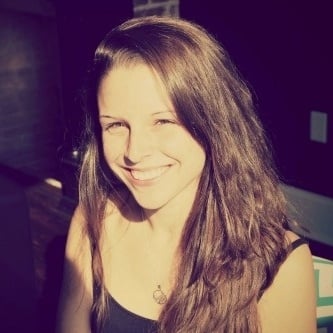
Safety first! Pay attention to these six rules when installing and taking care of your robot.
Next-gen robots are taking the manufacturing industry by storm.
Citing growing concerns over their workers' job security, some manufacturers are embracing cobots – or collaborative robots – as a means of raising productivity while ensuring there will still be jobs for human workers.
At Assa Abloy, robotics expertise was built around engineers and technicians in charge of automating processes with new technologies.
This is a great idea, but there are some common hazards. Here are six some fundamental rules to follow when introducing AI-driven robots in the workplace:
1. Regulate self-learning robots
Self-learning robots are a significant step forward in robotic technology. Instead of being limited by their initial programming, next-gen robots are capable of observing their environments, monitoring the activities of others, and even learning new, more efficient ways to complete tasks.
This has the potential to create a whole generation of self-aware, self-learning robots; but there are some hazards to consider, too.
How will programmers and manufacturers regulate the robot's ability to learn? How will the robot know when it's learned enough – and how far does its curiosity go?
Questions like these must be answered before robots go mainstream.
2. Examine mechanical parts for wear and tear
Mechanical failures represent a significant portion of robotics hazards in the workplace. As such, it's important that all robots are regularly inspected for signs of damage.
It's not enough to examine the robot's outward appearance. To properly diagnose any potential issues, inspectors need to get inside the machine and examine the mechanical parts that make the device tick. Any problems here must be addressed immediately and before production resumes.
3. Inspect electronic components for authenticity
Like almost everything of value, electronic components are sometimes faked. Considering that many robots originate overseas, where vendors and suppliers aren't always verifiable, it's all too easy to fall victim to such a scam.
Counterfeit electronics are more prone to serious malfunctions or programming errors. They're almost impossible to detect in preassembled machines — which would require complete disassembly and reassembly.
For individual or replacement pieces, examine the packaging. Look for any misspellings or errors, as these are obvious signs of a forgery or counterfeit merchandise. Authenticate parts by verifying their OCM codes and check that the country of origin matches the country code on the part itself. While these steps won't always guarantee that you'll detect counterfeit parts, it will be harder for counterfeiters to sneak them past your watchful eyes.
4. Prevent unauthorized or improper maintenance and installation
The installation and maintenance of robots pose concerns, too. If technicians don't receive proper training, or if they fail to follow the necessary safeguards, serious repercussions could follow.
A robot recently malfunctioned during installation and killed one of its installers in a Volkswagen assembly plant in Germany. Although this unfortunate incident did not involve any wrongdoing on behalf of the human installers, and tragedies like this one are rare, it highlights the severity of the risks involved with industrial robots.
5. Ensure the safety of nearby workers
It's up to individual business owners to ensure the safety of their workers, but next-gen robots introduce new challenges. Like all electronic devices, robots are prone to malfunction. What happens if a machine malfunctions and injures a nearby worker?
Not only is it important to provide human workers with training and guidelines regarding working around robots, but it's also critical that robots are aware of their human counterparts and take necessary safety precautions whenever applicable.
It's one thing to assign a robot to the most dangerous jobs on the factory floor, but they still need to complete the task safely.
There are already multiple examples of robot malfunctions resulting in injury or fatality. In early 2017, a robotic arm struck and killed a worker from Michigan. Minimizing the threat to human workers should be the top priority of any workplace that combines robots with a traditional human workforce.
6. Watch for basic human errors
Although many first-time robotics users are concerned about errors during the initial programming or installation stage, human mistakes during operation are just as costly. If an operator lacks the proper knowledge to run a robot on a day-to-day basis, or if they aren't familiar with the proper safety protocol, a basic error could easily become a catastrophe.
Workers who attempt to apply a quick fix to a machine, for example, put themselves and others at serious risk. A passing worker who intervenes in an attempt to help others might end up risking their own safety, too. Common human errors are responsible for a large number of avoidable incidents in the workplace.
Robots don't yet know right from wrong
While robots and cobots can boost productivity and efficiency in nearly any factory setting, they're not perfect.
They're still prone to mistakes – either as a result of erroneous programming or a basic malfunction – and not all of them are intelligent enough to identify errors.
By making workers aware of this fact, company owners can help mitigate the risks of working with robots.
Leave a comment