What is a Cobot (Collaborative Robot)? Types & Applications
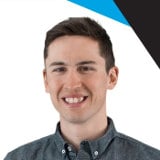
Posted on May 25, 2015 in Collaborative Robots
6 min read time
The word “cobot” has been widely used for different things. In this article, we elaborate on its meaning and the variations on its use.
What is a Cobot (Collaborative Robot)?
A cobot is short for collaborative robot. It is intended for direct human-robot interaction within a shared workspace, or where humans and robots are in close proximity.
A cobot enhances productivity and safety. Unlike traditional robots, cobots are equipped with advanced sensors and programming to enable safe, adaptable interaction with human coworkers.
So basically, it is a device that helps you accomplish your day-to-day job using user-friendly automation.
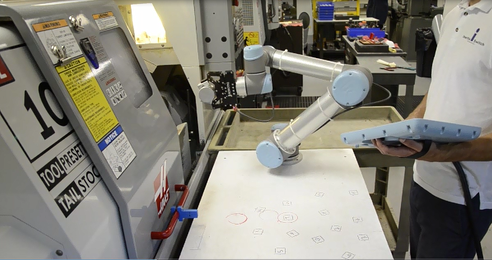
Safety Features of Collaborative Robots 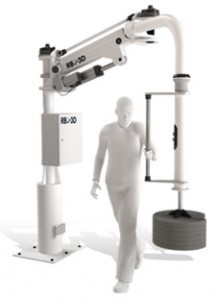
What makes a robot a cobot? What makes a robot ''collaborative'' is that it can detect abnormal activity in the environment through force limitation or vision monitoring.
Sensors allow for cooperation between humans and robots without any physical separation. Most importantly, a cobot answers to the 4th criteria of safe collaboration, which is force and power limitation.
In fact, all collaborative robots have force sensors in their joints, which stop their motion in case of an impact in real-time.
In other words, if the robot touches a human or if a coworker enters a specific zone, the cobot is programmed to either stop entirely or to slow down to avoid injury to the human or damage to material in the cobot’s way.
This allows you to run the robot at full speed without worrying about the potential danger of the kinetic energy being carried by the robot arm.
There are various models of cobots on the market. From small tabletop robots to cobots capable of carrying heavier payloads. To get a better idea of the different cobots available take a look at our cobot comparative chart.
Types of Cobots
There are four types of cobots: power and force limiting cobots, safety rated monitored stop, hand guiding, and speed and separation monitoring.
All types of cobots allow for shared workspaces between robots and human workers. Let’s take a closer look at each type.
- Power and force limiting: Designed to work safely alongside human coworkers, these cobots are limited in the amount of force they can apply to their surroundings. They have rounded corners and no sharp edges, which reduces the chance of injury to humans and eliminates the need for additional safety barriers, vision systems, or external scanners. These cobots also feature enclosed motors and lack pinch points where a person or clothing might get caught. Equipped with intelligent collision sensors, these collaborative cobots automatically stop when they make contact with a human coworker. While they tend to be more flexible, they are also smaller, slower, and less powerful than traditional robots.
- Safety rated monitored stop: These cobots use sensors to detect the presence of humans and automatically stop when a worker enters a designated zone. Workers can easily resume operation once they have left that area. These are ideal for industrial tasks with minimal human intervention, and these cobots are equipped with safety sensors, ensuring they stop when they get too close to a human worker.
- Hand guiding: These cobots allow human operators to physically guide them through tasks. These are user-friendly as the programmer can simply demonstrate how to perform a task by manually guiding the cobot. This feature makes it easy to reprogram the cobot without altering the software. The short learning curve helps these cooperative cobots minimize downtime.
- Speed and separation monitoring: These cobots use sensors to maintain a safe distance from human workers, offering safety features similar to safety-rated monitored cobots but with added capabilities. For example, a machine vision system constantly monitors two operational zones: the warning zone and the stop zone. If motion is detected near the warning zone, the cobot slows down to a safe speed. If a person enters the stop zone, the cobot halts immediately and resumes operation once the person has moved out of the area.
The Load Handling Assistant
Historically, when talking about a cobot, people were referring to a load-handling assistant developed by RB3D.
In 2008, the company focused widely on ergonomics and Muscular Skeletal Disease (MSD) risk reduction. The first audits led to the need for a ''collaborative robot'' to reinforce users with extra strength.
Consequently, after its study was launched, the company purchased assembling and controlling tools for its manufacturing. The first Cobot was delivered in 2011.
However, for our purposes, this isn't a robot. It is a handling assistant. In other words, it cannot be programmed or work autonomously, it simply helps workers transport heavy payloads from one point to another. So the human hand guides the structure (and load) where s/he wants to move it to and the ''cobot'' absorbs the load.
It works like an exoskeleton where loads are absorbed by a mechanical structure that monitors your body motions and works in coordination with your movements.
Personal Interface
CoBot robots is a project from CORAL (Cooperate-Observe-Reason-Act-Learn). The CORAL group is a group of students and professors from Carnegie Mellon University.
The CoBot project is basically a mobile platform designed to execute localization, navigation and multi-robot task planning using a web interface.
The robots are now able to navigate and localize themselves autonomously. The robot has to collaborate (or navigate) around human workers and monitor their position to avoid them.
Cobots vs. Industrial Robots
Cobots and traditional Industrial robots have several similarities as well as a few differentiators. Let’s take a look at the main differences between a cobot and a traditional industrial robot.
Industrial robots are designed to operate independently, while cobots are built to work alongside humans. Unlike industrial robots, which excel in speed and precision for repetitive tasks, cobots are equipped with sensors and safety features that allow them to interact safely with human workers.
Cobots are generally more lightweight and flexible than industrial robots, which tend to be larger and more powerful. Cobots are commonly used in tasks like assembly, packaging, and quality control, while industrial robots are often deployed for specific tasks in highly automated, structured environments like in the automotive industry. Industrial robots generally have higher payload capacities and speed than cobots, but are less user-friendly and more rigid.
While industrial robots are typically enclosed in safety cages to protect workers, cobots can operate alongside humans without physical barriers. Most industrial robots are large, autonomous, and expensive, while cobots are a more flexible and cost-effective solution, particularly for smaller businesses.
Another reason to choose collaborative robots is to counter the cultural fear that robots will replace human workers. Rather than replacing human workers, cobots are meant to enhance their abilities. Often, cobots are designed as robotic arms, effectively giving human workers an extra pair of hands.
Collaborative Robot Applications
So how and where are cobots actually used? Here are the four most common applications of cobots:
- Assembly. Cobots are utilized in precise and repetitive assembly tasks, including screwdriving, part fitting, and insertion.
- Dispensing. By using torque sensing, cobots are used for dispensing projects such as gluing, sealing and painting. This reduces waste and increases the accuracy of dispensing.
- Finishing. Cobots use force control to automatically adjust to the required pressure, ensuring consistent polishing, sanding, and buffing of materials.
- Machine tending. Cobots are employed in machine-tending tasks such as computer numerical control (CNC) operations, injection molding, and in-circuit testing, where individual components are inspected for damage.
Cobots generally have lower power requirements than their larger, autonomous counterparts, are often mobile, and use collision detection to prevent injury to their human colleagues and other cobots. They are used in different industries including Electronics, Automotive, General manufacturing, Supply chain management, Healthcare, Plastics, Food and agriculture, and more.
Some popular robotics providers and cobot manufacturers include FANUC, Yaskawa Electric Corp., Universal Robots, KUKA, Rethink Robotics and Techman Robot.
Cobots and AI
Artificial Intelligence (AI) is elevating cobots to new heights.
Until recently, cobot technology mostly concentrated on singular functionalities, like aiding workers in tasks such as lifting and packaging products.
The integration of Artificial Intelligence brings forth numerous advantages for cobots.
AI-powered collaborative robots (cobots) are transforming industries by enhancing their ability to perceive and adapt to their surroundings. Through technologies like 3D machine vision, cobots can detect an object’s size, shape, orientation, and depth, enabling safer and more efficient operations in complex environments.
These capabilities make cobots ideal for tasks ranging from repetitive manufacturing to dynamic navigation in shared spaces, where they autonomously adjust speed and avoid obstacles.
AI also ensures cobots can collaborate effectively with humans, augmenting productivity while prioritizing safety.
Beyond manufacturing, these advancements pave the way for cobots to play critical roles in construction, security, and beyond.
While some worry about job displacement, AI cobots are creating new opportunities by reshaping the nature of work. They take on repetitive, labor-intensive tasks, freeing human hands for more engaging roles and driving innovation in human-machine collaboration.
With ongoing research into conversational AI and intuitive interfaces, cobots are set to revolutionize industries, offering safer, smarter, and more productive solutions for the future.
Leave a comment