Automated Palletizing: How it Works and How to Get Started
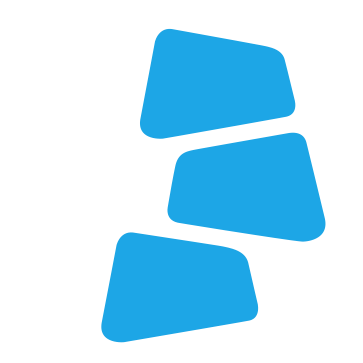
Posted on Oct 02, 2024 in Palletizing
12 min read time
Did you know that 80% of all goods are transported on a pallet at some point in their journey?
If you're relying on manual labor to place your products on pallets, you're not alone. However, the last decade has driven factories of all sizes in various industries, such as food and beverage, pharmaceuticals, and general manufacturing, to rethink workforce utilization and adopt palletizing robots.
Whether you're facing labor shortages, high insurance costs due to workplace injuries, or the need to close efficiency and productivity gaps to ensure growth, automating your end-of-line processes is a crucial transformation project to prioritize.
This article provides an overview of the types of automated palletizers, how they operate, their impact on your business, and the steps to implement one.
What is an Automated Palletizer?
An automated palletizer is a robotic system designed to automatically arrange and stack products or packages onto pallets for shipping, storage, or distribution. It uses advanced technology to perform tasks traditionally done by manual labor, such as picking up items from a conveyor belt and placing them in specific patterns on a pallet.
The 2 Types of Automated Palletizers
Automated palletizers can be categorized into 2 main categories: Traditional robots or Industrial robots and collaborative robots (cobots)
Traditional robots (industrial) excel in high-volume, repetitive tasks, handling heavy payloads at high speeds. They require significant investment, large footprints, safety fencing, and specialized staff for operation and maintenance.
Collaborative robots (cobots), on the other hand, prioritize flexibility and adaptability. They work safely alongside humans (with a proper risk assessment) without extensive barriers and are easily reprogrammable for different tasks. Cobots are generally more affordable and space-efficient, making them suitable for smaller operations or limited floor spaces. However, they typically have lower payload capacities and operate at slower speeds than traditional robots.
The choice between traditional robots and cobots depends on specific operational needs. Factors to consider include production volume, task variety, available space, budget, and workforce skill level.
Traditional robots suit large-scale, high-speed operations, while cobots offer versatility and accessibility for diverse or changing production environments.
Benefits of Automating Palletizing
Cut Labor Costs and Overcome Employee Scarcity
Manual palletizing incurs significant labor costs, including wages, benefits, overtime, and expenses related to hiring and training due to turnover. Factories also face higher maintenance and downtime costs from worker absences, vacations, and departures, leading to production delays. The recurring expenses of recruiting and training replacements add substantial overhead, particularly in high-turnover industries.
There's a clear trend away from jobs involving strenuous manual tasks like heavy lifting, which are both physically taxing and mentally unfulfilling. This preference is reflected in economic data, according to the U.S. Chamber of Commerce, 45% of durable goods manufacturing jobs in the United States remain vacant.
The labor shortages manufacturers face today are likely to persist. Deloitte predicts in its 2024 manufacturing industry outlook report that even if every skilled worker in America were employed, there would still be 35% more unfilled job openings in the durable goods manufacturing sector than available skilled workers. By 2030, they project a shortage of more than two million American manufacturing workers.
Automating palletizing enables your valuable employees to do more and grow with your company. As an employer of choice, reduce your dependency on hard-to-find labor and create jobs that people want to do.
Gain productivity and efficiency
Automated palletizers can operate 24/7 which greatly increases output compared to manual processes. This boost is vital for meeting growing demand or seizing new market opportunities. Manufacturers unable to invest in automated palletizing may lose market share to more agile competitors.
By adopting advanced automated systems, you'll outpace competitors with superior efficiency, quality, and cost-effectiveness. This enables you to offer better prices and higher quality products with pallet consistency, securing your market position and winning more contracts.
Automated cobot palletizers are known to offer flexibility and adaptability - they are usually easy to program to changing needs. This flexibility keeps you agile in a dynamic market, ensuring long-term growth and competitiveness.
Provide a safer workplace
Automating your palletizing cell can significantly reduce the risk of injuries related to repetitive motions, heavy lifting, and exposure to hazardous materials. Manufacturers who do not automate may face higher insurance premiums and potential costs related to workplace injuries and associated litigation.
Manual material handling, which includes palletizing, is a significant risk factor for MSDs. According to the National Institute for Occupational Safety and Health , about 30% of overexertion injuries in the workplace were associated with lifting tasks
Automating your palletizing process reduces costs, addresses labor shortages, boosts productivity, and creates a safer work environment. This enables your employees to take on more meaningful tasks and ensures consistent pallet quality, prioritizing your customer and brand.
How to Get Started with Automated Palletizing
Step 1: Outline your business needs
Automating your palletizing cell process starts by outlining your business challenges and opportunities. At Robotiq, we have developed a comprehensive grid, the Strategic Imperative Framework.
Designed to be a thought-provoking process, it guides stakeholders in ‘scoring’ their challenges to solve and covers different aspects of automating tasks (process, engineering, maintenance, people and finance). Spending time at this step is encouraged to align the decision process in the right strategic direction.
Step 2: Select the right solution
Understanding the current market landscape is a critical step. Selecting an option without considering all available solutions might result in overlooking viable alternatives. It is essential to undertake this step before committing to any one solution.
For a general overview, the available solutions can be divided into two major categories: Traditional robots and Collaborative robots.
Traditional Robots |
Collaborative Robots |
|
Best solution for factories with .. |
- a high volume of the same product to palletize - a constant production volume throughout the year - more than 1 shift of operation - boxes to palletize weighing over 30kg (66 lbs) - more than one operator doing manual palletizing |
- a low to medium volume of production |
Benefits and advantages |
- High efficiency and speed |
- Small footprint |
Drawbacks |
- Large footprint |
- Very limited throughput and pallet height (unless a vertical linear axis is used) |
Each of these categories includes various palletizing solutions, each with its own unique benefits and risks. For a detailed analysis of the solutions available on the market, we invite you to download the Automated Palletizing Buyer’s Guide.
Step 3: Evaluate the Cost
As a general estimate, a collaborative robot palletizer for a small to medium-sized operation can range from $50,000 to $150,000, while the traditional robot palletizer can cost upwards of $500,000 or more. When evaluating the total cost of an automated palletizing system, you should adopt a comprehensive approach that considers both initial and ongoing expenses, as well as future scalability and flexibility.
Here are the key points to consider:
1. Cost Components
- Initial Investment: Includes the purchase price, integration with existing systems, customization to meet specific needs, and potential vendor lock-in.
- Operating Costs: Encompass energy consumption, maintenance and repairs, training for staff, and software updates or licensing fees.
- Additional Costs: Consider expenses related to downtime and the cost of scaling or adjusting the system in the future.
2. Budget Considerations
- Budget Pricing vs. Quoted Pricing: Distinguish between estimated budget costs and actual price quotes to ensure accurate comparisons. Be aware of vendors' recommended contingency funds for unexpected expenses.
- Essential vs. Nice-to-Have Features: Clearly define which features are necessary for your operations and which are optional. Use detailed specifications to prioritize essential features and eliminate unnecessary ones, potentially requesting revised quotes from vendors.
3. Initial Investment Factors
- Integration: Assess how well the palletizing system will align with your factory layout, processes, and existing systems. Ask vendors about compatibility, required modifications, and examples of successful integrations.
- Customization: Determine if the system meets your essential requirements out-of-the-box or if additional customization is needed, both initially and over time to maintain functionality.
- Vendor Lock-In: Consider the long-term implications of relying on a specific vendor, including how it might affect scalability, flexibility, and future costs.
- Scalability: Evaluate whether the system can grow with your needs, the costs associated with upgrades, and if it allows for incremental investments as requirements evolve.
4. Operating Costs Details
- Energy Costs: Vary based on system efficiency, usage duration, and local electricity rates.
- Maintenance and Repairs: Regular upkeep is essential. Understand who will perform maintenance, the terms of service contracts, and the availability of spare parts.
- Training Costs: Factor in the expenses for training employees to operate and maintain the system effectively.
- Programming and Software Updates: Account for software licensing fees, subscription costs, and whether updates or programming changes require external support.
5. Practical Tips for Evaluation
- Vendor Questions: Prepare specific questions about integration capabilities, customization options, scalability, and support services to ensure the system meets your needs.
- Cost Tracking: Keep a detailed record of all potential expenses to achieve a more accurate estimate of both initial and ongoing costs.
Step 4: Calculate your ROI
Now, understanding the initial and ownership costs from the previous chapter, the next logical step is to project the Return on Investment (ROI). Here are the formulas and factors that should be considered to calculate your return on investment:
PRODUCTIVITY GAINS
- Cycle time: Duration to complete a specific task or produce an item.
- Output: Number of units processed per unit of time.
- Scalability: Ability to increase volume with minimal additional cost.
LABOR IMPACT
- Labor costs: Current manual labor costs, including wages and benefits.
- Labor efficiency: Productivity and efficiency of manual labor.
- Labor flexibility: Ability to reassign labor for various tasks.
COST OF OWNERSHIP
To define the total cost of ownership, the operation costs should be added to the initial investment by considering a specific period (typically predefined by the business) for each solution in the comparison.
INVESTMENT RISK ASSESSMENT
Any investment can have risks. It is important to consider them and have a mitigation plan if they happen.
- Identify risks: Potential risks such as technological failures, market changes, or regulatory issues.
- Risk mitigation: Document strategies to mitigate each risk and calculate the potential cost associated with mitigation.
- Include a risk factor in your ROI comparison: Look at your factory's previous, large-scale, cross-functional investment projects. Were they on time and on budget? If not, add that risk factor to your ROI calculation for traditional robots palletizing solutions.
INTANGIBLE BENEFITS
These may not be clear numbers, but they are qualitative gains that need to be considered in your decision process.
- Safety: Decrease costs associated with workplace accidents, medical leave, injuries, and near-misses.
- Employee engagement: Evaluate the influence on workforce morale and the increase in employee retention.
- Quality improvement: Calculate the reduction of costs related to errors.
- Market reputation: Estimate the positive impact on the company's reputation (both with customers and job candidates) for innovation and efficiency.
Depalletizing: What You Need to Know
Depalletizing is the process of systematically removing boxes, bags, or other packaged items from a loaded pallet. It is often the first step in a manufacturing or distribution process, where raw materials or finished goods arrive on a pallet and need to be unpacked.
Key Differences Between Palletizing and Depalletizing:
- Unloading Challenges: With palletizing, the robot has full control over the placement of items on the pallet. Depalletizing involves unloading a pallet that was loaded by someone else, so the item positions may be unpredictable.
- Item Movement in Transit: Pallets can shift during transportation, causing the items on the pallet to move from their original positions. Depalletizing systems must be able to account for this movement, unlike palletizing.
- Robot Vision Requirements: Depalletizing often requires the use of robot vision systems to adapt to the uncertainty of the pallet layout, whereas palletizing can sometimes be done without vision.
- Upstream/Downstream Processes: Palletizing typically occurs at the end of the production workflow, while depalletizing happens at the beginning, interacting with different processes.
- Facility Layout: Palletizing and depalletizing systems are often placed in different locations within a facility to optimize their integration with upstream and downstream operations.
Understanding these key differences is important when deploying robotic automation for palletizing and depalletizing tasks.
Conclusion
Automated palletizers boost productivity, address labor shortages, and enhance workplace safety. They increase throughput, remove physically demanding tasks, and reduce injury risks - providing a competitive edge for factories. Investing in automated palletizing is a strategic move to streamline operations and position your organization for long-term growth.
Leave a comment