7 Ways to Prevent Operator Injury With Sanding and Polishing
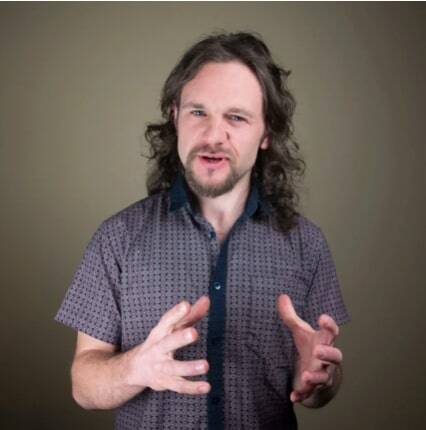
Worker injury can be a major drain on a business. Finishing tasks like sanding and polishing are more dangerous than you'd think. Here's how to prevent injury.
The simple task of sanding a surface… it doesn't look like a very dangerous job, does it?
Sure, sanding and polishing might not be as dangerous as, say, juggling with flaming knives, but they have their own share of dangers which can impact heavily on a business in the long term.
A large proportion of the 35% of workdays lost to injury are the type of injury that can be caused by performing finishing tasks with a power tool.
How can you avoid this operator injury to reduce these work days lost?
In this article, we'll introduce 7 ways that you can prevent injury in finishing tasks.
1. Use robotic finishing
One of the most effective ways to reduce injury — or even eliminate it — is to stop doing your sanding and polishing by hand. Instead of having your operator use manual power tools, they can program a robot to do the sanding or polishing task.
Robotic finishing is not suitable for every sanding or polishing task, but for those it suits it has a dual benefit:
- It moves the operator away from the dangerous part of the job.
- It allows them to move to more interesting, value-added tasks.
Until recently, automated finishing was completely unreachable for most businesses. It involved investing big in huge finishing machines. These CNC-like machines were costly, inflexible, and took up a lot of space on the workfloor.
With robotic finishing, the bar of entry is much lower. Here are 5 Questions to Ask Yourself Before Using Robot Finishing.
Saint-Gobain reduced injuries and increase productivity with the FT 300 Force Torque Sensor
2. Wear the right protective equipment
It might seem obvious but one of the most common (and effective) ways to reduce harm with manual finishing is to wear the right personal protective equipment (PPE).
I know, you've heard it all before.
The main types of PPE are:
- Respiratory protection — Sanding and finishing dust can be extremely damaging to health, especially when exposure is prolonged.
- Eye protection — Flying bits of material can easily jump from the sanding machine and fly into your eye, even if you're wearing spectacles.
- Hearing protection — Most finishing machines are relatively quiet, but the louder ones may produce dangerous noise levels.
- Foot protection — In general, foot protection is just a good idea in manufacturing. I don't advise wearing open-toed sandals in a machine shop.
- Hand protection — Sanding machines can, and often do, cause skin burns. It's too so easy for a tool to jump suddenly, lightly touch the skin on your hands, and cause a cut, scratch, or burn. In fact, it happened to me just the other day.
We know all this, but sometimes we don't protect ourselves as much as we should when performing finishing by hand.
3. Improve task ergonomics
Bad ergonomics is one of the most common causes of workplace injury. Tendinitis, carpal tunnel syndrome, DeQuervain’s Disease… the list of potential injuries is rather shocking when you consider that the actions that cause them are so common in the day-to-day life of a finishing operator. They contribute to tens of millions of doctor's appointments every year.
Improving the ergonomic design of the cell is an important step to reducing these risks. However, due to the nature of the work, not all risks are completely avoidable when performing the tasks manually.
4. Minimize harmful vibrations
Anyone who has used a power sander for more than an hour at a time has experienced the unusual feeling of pins and needles in their hands after turning off the machine. Although the feeling usually goes away eventually, this prolonged exposure to vibration can cause serious damage when you are performing sanding operations every day.
In the most serious cases, "hand-arm vibration syndrome" can require amputation of the operator's hand. While sanding is not as dangerous as, say, using a pneumatic drill, it is still a risk.
The only reliable way to reduce this risk is to minimize the amount of time that the operators are performing sanding or polishing tasks.
5. Ensure workpiece is fixed down
When we are doing sanding jobs all day, it's so easy to forget to secure our workpiece properly. Unlike some more accurate and/or aggressive manufacturing tasks (e.g. machining), it's not usually a big deal if we don't fix down the workpiece completely when we are sanding, even though we know that we should.
One danger of this is that the workpiece could move unexpectedly, fall and harm the operator or other people in the surrounding area. Worse would be if the sanding or polishing machine then fell from your hand whilst it was still running, causing further damage.
The solution to this is, of course, to ensure that the workpiece is firmly fixed in a jig or holding device, even for small sanding jobs.
6. Reduce dust in the environment
The dust produced by sanding and polishing can be particularly harmful to health in the long term. As mentioned above, this risk can be reduced by using the right PPE but it is also possible to reduce the dust in the environment with on-tool dust extraction and/or dust extractors in the workplace.
Dust extraction is not just beneficial to the health of sanding operators. It also allows you to ensure that there is a clearer work environment that requires less cleaning once the jobs are all over.
7. Limit hands-on time
Although we have listed some ways to reduce injury in sanding and polishing tasks, you can never remove all the risks to health. The only real solution — particularly with tool vibration — is to limit the time that operators are performing manual finishing tasks.
The problem with limiting hands-on time is that it also limits the productivity of your operation. When finishing tasks are not being carried out, there is no production…
… unless you use robotic finishing.
Robotic sanding and polishing allow you to have a more productive, less dangerous, and more efficient finishing operation.
How could you use robotic finishing in your business? Tell us in the comments below or join the discussion on LinkedIn, Twitter, Facebook or the DoF professional robotics community.
Leave a comment