7 Palletizing Cell Layout Considerations That Affect Cycle Time
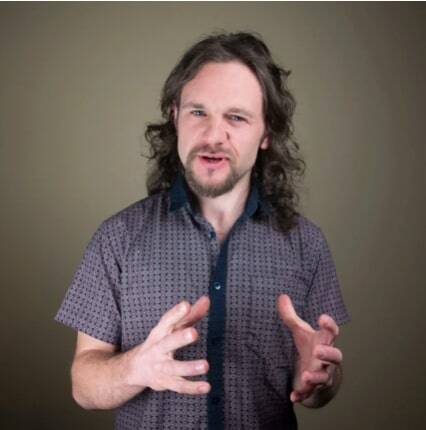
Posted on Mar 03, 2023 in Palletizing
5 min read time
There are a lot of factors to consider when you are designing a palletizing cell. Even small decisions that you make during the design phase of deployment can significantly affect the performance of the robot, including the all-important cycle time.
Palletizing cell layout has a very clear impact on cycle time. Placing the components of your cell in even a slightly different position can add or subtract seconds off the time to complete one palletizing cycle.
With the right palletizing cell layout, you can improve space utilization in your cell, achieve faster cycle times, and increase your cell throughput.
Here's how you can optimize your cell layout quickly and easily.
How palletizing cell layout affects cycle time
Palletizing cell layout is the arrangement of elements within a robotic palletizing cell. This includes factors like placement of the robots, conveyor position and orientation, pallet size, and various other factors.
The layout can significantly affect the cycle time and, thus, the performance of your entire palletizing process. For example, a robot that is placed further from the conveyor might take 2 seconds longer to pick up a box than one that is closer. These 2 wasted seconds quickly add up over the course of a work shift – for a throughput of 12 pallets per hour, it could amount to over 2 wasted hours per 24 hours.
When designing your cell, you also have to make other decisions. For example, do you want to use centralized or decentralized palletizing? Centralized palletizing involves using a single robotic cell to handle all your palletizing tasks. Decentralized palletizing involves using a different robot for each production line. Your choice will also affect cycle times.
There are various steps to design a robot cell for palletizing. Optimizing the movements of your collaborative robot is a powerful way to get remarkable gains from seemingly minor changes.
7 considerations when designing a palletizing cell layout
Designing a palletizing cell can be very easy, especially if you use a tool like our Palletizing Configurator, which does a lot of the hard work for you.
Here are 7 factors that will affect cycle time in your palletizing cell layout:
1. Positions of robot and conveyor
The position of the robot and conveyors is probably the most important consideration in any cell layout.
You should position the conveyor so that it can deliver the boxes as close to the robot as possible. Often, this means orienting the conveyor so it reaches the pallet end-on and not horizontally.
2. Safety equipment or fencing
You need to separate human workers from palletizing robots, even when using collaborative robots.
Ensure that you leave enough space within your safety fencing or sensor zone so that everything can fit, including leaving space for people to enter to handle the pallets.
3. Distances between cell elements
The distances between cell elements have a direct impact on the cycle time. Every unnecessary millimeter that the robot moves will add unproductive time to the task.
Try to reduce distances as much as possible. However, make sure to leave enough free space that you don't increase the chance of collisions.
4. Height of conveyor
The height of the conveyor, relative to the robot and pallet, can have a huge effect on the cycle time.
By placing the conveyor close to the midpoint between the top and bottom of the loaded pallet, you can make the speed of each box placement more consistent. Boxes in the center of the pallet will be placed faster and those at the top and bottom will be slightly slower.
5. X-Y distances
As well as the height, the horizontal (or X-Y) distances can also add or remove unnecessary cycle time.
Say that you add an extra labeling step to the palletizing task. It might feel natural to place the labeling machine further away from the conveyor to avoid collisions. However, this would add extra time to each box placement. Instead, it is better to minimize this distance.
6. Position of interlayer dispenser
If you are using interlayers between layers on your pallet, it is important to consider the placement of the interlayer dispenser.
Often, the best place for the dispenser is right behind the pick location on the conveyor.
7. Robotic solution used
Finally, the specific robotic solution that you use will strongly affect the performance of the cell.
One factor to consider is how easy it is for you to edit the robot programs. With a solution like the Robotiq Palletizing Solution, you can easily tweak the program if you notice an inefficiency in the cell layout. This helps you to continue to improve the program and cycle time over time.
The key to an optimal layout: minimize movements
As you can see from the list above, many of the considerations that affect the cycle time of your palletizing robot come down to one factor: distance.
By reducing the distances between components in your cell, you reduce unnecessary movements that the robot has to take between palletizing steps. You should try to minimize movements while avoiding collisions between the elements of the cell.
The simplest rule is to have the pick point as close as possible to the drop point.
By planning ahead and using tools like our Palletizing Configurator, you can ensure that the robot moves in the most efficient way.
Where to get more expert advice on setting up your robot
Do you need more information on how to set up your robotic palletizing system?
You can get a lot of detailed advice in our free eLearning courses. The course on Lean Robotics for Palletizing is a great place to start. As well as teaching you the basics of robotic palletizing, it introduces you to typical layouts and many useful tips on how to improve efficiency in your palletizing process.
What aspects of your palletizing cell do you think are least efficient? Tell us in the comments below or join the discussion on LinkedIn, Twitter, Facebook, or the DoF professional robotics community.
Leave a comment